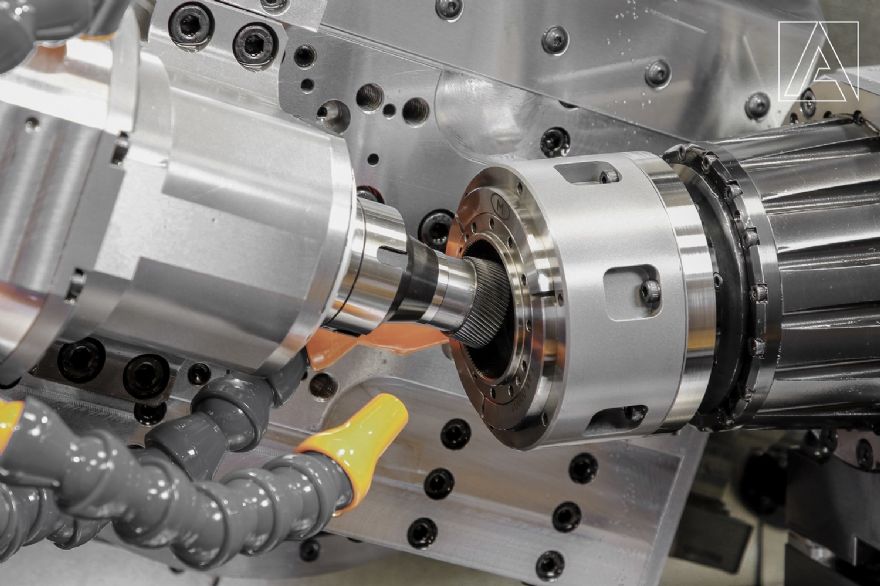
When the Swiss
Affolter Group was developing its AF160 — an eight-axis CNC gear-hobbing machine for producing a wide variety of gears and worm screws (up to DP 12.7) for applications in the automotive, aerospace, gearbox, medical, and robotics industries — maximum versatility was the key goal.
Vincent Affolter, the Affolter Group’s managing director, said: “The AF160 is designed for high-precision manufacturers that need flexibility and efficiency. With its eight axes, advanced automation solutions, and an innovative quick-change system that gives three hobbing configurations, the machine provides exactly that.
“With the optional quick-change system, machine operators can switch from one configuration to the next in only 30min. In configuration I, both the C axis and the C’ prime axis are equipped with driven spindles. This setup offers an A-axis swing of ±50deg and results in optimised cutting quality, torque, and rigidity; it is ideal for producing spur, helical, bevel, crowned and face gears.
“Configuration II gives the operator even more flexibility. It sees a tailstock on the C axis, a spindle on C’ prime, and an A-axis movement from -50 to +115deg, making worm milling possible — along with all the gear types mentioned above. In configuration III, the C axis remains empty, and the C’ prime axis is equipped with a driven spindle. This configuration is designed for the power skiving of internal gears, as well as the production of face gears.”
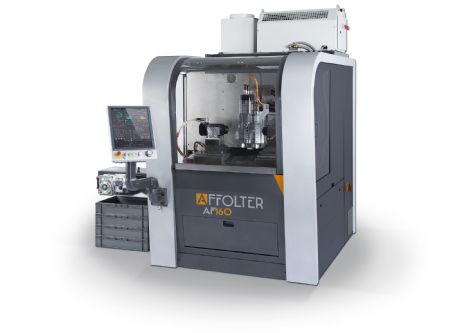
Mr Affolter said that regarding automation, the AF72 part loader has been designed specifically for the AF160. “With its double gripper system for parallel loading and unloading, and a telescopic arm, different configurations can be chosen to suit the volume, product and application.
“Moreover, the AF72 can be equipped with up to five feeding rails, allowing the machine to work autonomously for more than 24hr. The telescopic arm also ensures that the working area in the machine remains clear, retracting after loading a part to give the operator a good view of the processes during machining.”
The AF160 offers options that maximise flexibility. For example, hobbing options include skiving by sensor detection, integrating the deburring process into the gear production with the addition of the AF54 deburring unit, as well as part orientation and part presence control. Also available are different clamping systems, customisable coolant systems, and chip extraction conveyors.
Mr Affolter added: “The intuitive Pegasus CNC system controls all machine axes, as well as a multitude of peripherals. Programming via the 19in touchscreen is simple, intuitive. Moreover, data can be shared on the cloud, streamlining after-sales service support and preventive maintenance — and software updates can be done remotely.
The Affolter Group will showcase its innovative technologies at the
EPHJ high-precision exhibition (Hall 1, Booth E55) taking place in Geneva, Switzerland, 6-9 June 2023.