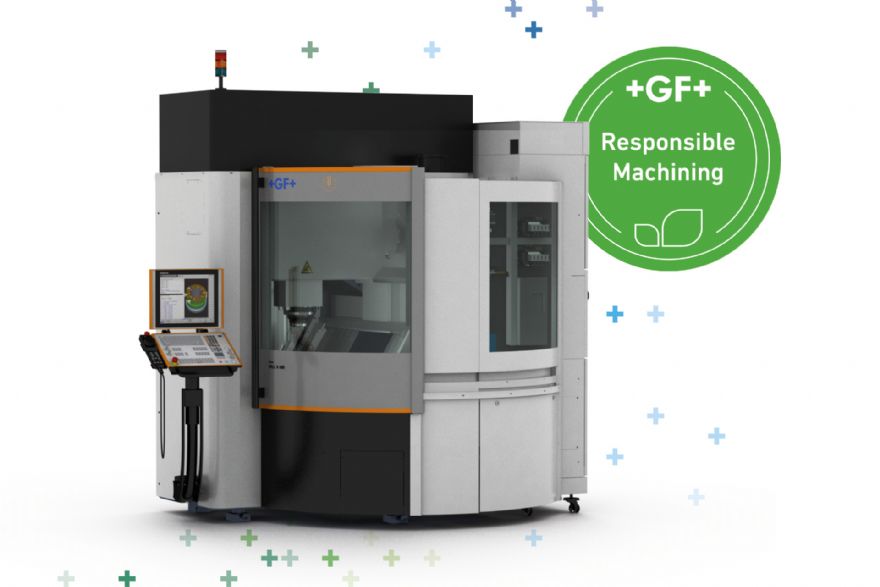
As a manufacturing concept, high-speed machining (HSM) was first conceived by Dr Carl J Salomon during a series of experiments he undertook in 1924. Fast forward 101 years, and HSM has moved from being a theoretical concept to one that, if done correctly, can provide component manufacturers and mould makers with exceptional surface finishes and increased productivity.
GF Machining Solutions provides component manufacturers and mould makers with a range of high-speed three- and five-axis machining centres, all of which have a rigid design and build and feature high-speed Step-Tec spindles up to 42,000rev/min, linear motors and generously-sized tool changers (up to 220 tools), thermal compensation, as well as impressive rapids up to 100m/min. Furthermore, the machines are geared up for HSM operations and for delivering superior surface finishes — irrespective of the application.
So, what exactly is HSM?A general misconception is that HSM and high-performance machining (HPM) are the same. But this is not the case. HPM is characterised by high chip removal rates, using trochoidal (circular cutting) tool paths with long tool engagement, while HSM combines a number of factors, such as the use of higher speeds and feeds, to increase and improve productivity and surface quality.
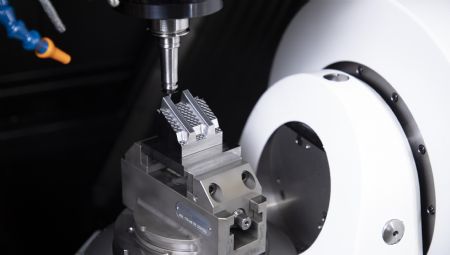
As a consequence, HSM requires higher spindle speeds, typically above 15,000rev/min, the use of smaller tools, and the taking of lighter cuts than traditional milling operations. With HSM there is a balancing act that needs to be achieved between a number of different machining elements — tool capabilities, machine tool capabilities, work-holding, tool holders and, of course, the material being machined.
These variables mean that there is ‘not a one size fits all’ approach to HSM, but rather it is more the case of having a good understanding of the process itself and adapting it to handle the materials being machined to obtain superior surface finishes. By managing chip load, heat generation and vibration, consistent surface finishes can be achieved.
Reduced chip loadWith HSM faster speeds and feeds, and reduced depths of cut are employed. The ability to ‘go faster’ delivers good material removal rates, even though less material is being removed per pass and can, in some instances, eliminate the need for a semi-finishing pass. When adopting a HSM approach it is important to consider feed rates. A larger feed per tooth will leave a rough surface finish as opposed to a smaller feed per tooth.
However, slow feeds can cause burnishing and a poor surface finish. Running at a higher rev/min means that the chip load is reduced, and the chips that are produced tend to be smaller and more easily removed, resulting in a smoother surface finish.
Machining at high speed does not necessarily generate excessive heat build up because with HSM the cutting tool spends less time engaged with the workpiece during the cutting process. A significant advantage of HSM therefore is heat dissipation: heat never really gets a chance to build up into the workpiece and is dissipated by the chips.
However, there are differences that need to be noted when machining different materials. For example, aluminium doesn’t act the same way as hardened steel. So, it’s important to know about a material’s machinability in advance in order to optimise the machining process.
A goal of HSM is to get the heat and chips away from the part as quickly as possible. Chip shape and colour are good indicators of how successful this has been done. When machining hardened steels, chips that are blue or purple indicate that the heat is reaching the chip and is not being retained in the part.
Successful HSM requires the right combination of a number of factors. The sharper the cutting tool, the better. A sharper cutting tool will result in an effective shearing action, moving chips away from the cutting zone (and thereby removing heat). But that is not always the case as anyone machining carbide will know.
One of the factors that determines HSM’s effectiveness is the machine itself. Today’s machine tools, designed specifically for HSM, are often extremely robust and feature linear guideways that enable faster feeds. The machine should have a strong frame to withstand the high forces and vibration generated. Machine tools with a polymer granite base, for example, can absorb vibrations.
Vibration in any capacity hampers the ability to achieve high-quality surface finishes. For example, when the cutting tool vibrates, it can leave marks on the workpiece, which may require additional passes to reach the desired finish requirements.
Cutting tool and workpiece stability all play a role in achieving good surface finishes. Well-balanced tools with limited runout are essential and a rigid spindle with a quality tool holder will also limit chatter. Using a thin holder with the tool sticking way out and running it at a high speed is going to result in deflection and a reduction in surface finish quality.
Additional considerations for improved surface finishesEffective HSM depends on a number of different elements and features. Any one aspect of the process can be a limiting factor to its success. Spindle speed, feed rates, stepovers, step downs, cutting tool geometry, tool holders, tool runout, tool length-to-diameter ratios, will all come into play, and this is especially true when machining hard materials. Stepover, a term to describe how far the tool moves over between each pass, also plays a big role in surface finish quality and productivity. One of the advantages of HSM is the time savings it takes to produce a part.
However, if the stepover is too big, there will be a cusp between the toolpath that becomes visible. To achieve a polished-like surface finish, lighter cuts and smaller stepovers are required, and this can be effectively achieved through employing higher spindle speeds. For example, when roughing a 3-D shape, there can be big steps, known as stair-stepping, in the part geometry. When working with HSM, the depth of cut can be reduced and the speed increased, meaning that smaller passes are taken, leading to less visible stepovers.
Additionally, cutting tool characteristics play an important role in achieving good surface finishes. A quality cutting tool will be able to perform at high spindle speeds and the cutting edge will machine uniformly on the surface. This is also dependant on having a good, rigid spindle that can hold the tool concentrically to the workpiece.