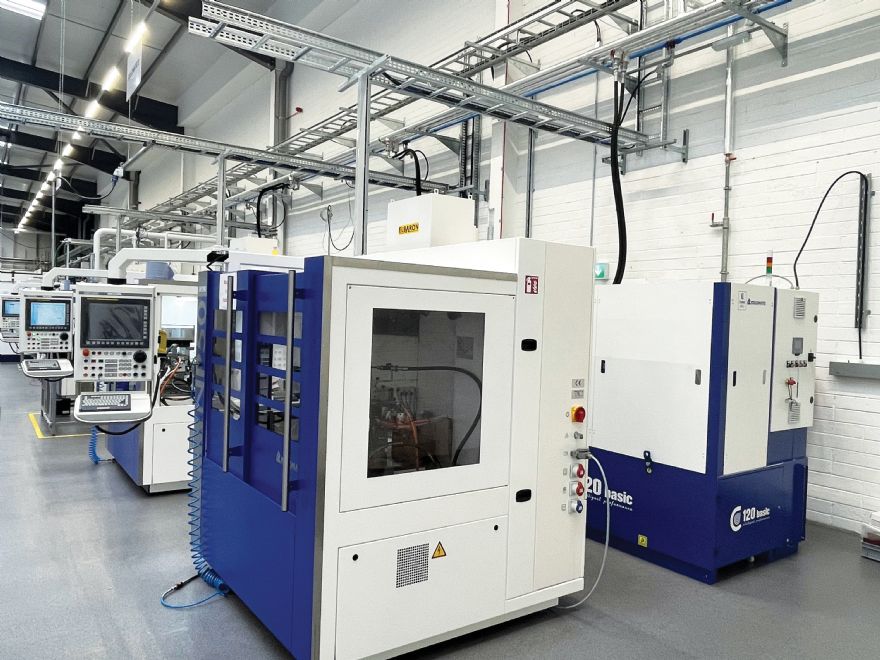
Based in Shannon, Ireland,
Smithstown Light Engineering is a leading MedTech company that provides contract manufacturing and precision engineering solutions to top medical device and orthopaedic companies globally. Customers include the likes of DePuy, Zimmer Biomet, Stryker, and Boston Scientific, and the company has grown rapidly in recent years as the larger OEM medical manufacturing companies have sought to use specialist outside providers for higher-value machining processes such as grinding and surface finishing.
Indeed, Smithstown recently ordered additional grinding machines from Coventry-based
Advanced Grinding Solutions Ltd (AGS). When installed, the new machines will mean that AGS will have supplied Smithstown with some £3.75 million worth of grinding machines since they started working together in 2021. The latest investments comprise a further Tschudin Cube centreless grinding machine, a six-axis Rollomatic 630XW grinding machine, and a large Comat filtration system. The machines will be used for producing shaft-type medical components, including those with particularly complex geometries.
Smithstown Light Engineering was founded by Brian King in 1974 as a machine shop, but it quickly moved to the design and supply of plastic injection moulds and press tools for the electronics industry, and later to contract manufacturing for the medical device sector. In 2011, the company was taken over by the founder’s son, Gerard King.
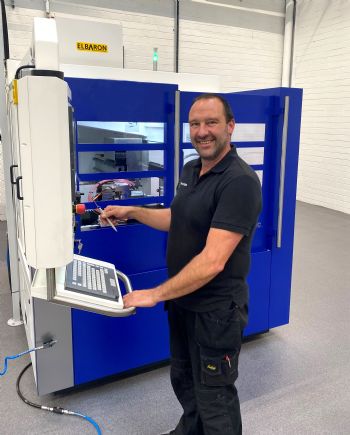
Today, Smithstown offers its medical customers a true one-stop shop for all kinds of medical component manufacture and undertakes a wide variety of processes; these include internal and external grinding, jig grinding, turning, milling, electro polishing, EDM, laser cutting and welding, 3-D printing, and heat treatment. The company has gained national and international recognition and has more than doubled in size in the last two years alone.
Mr King says his teams’ search for new and advantageous technologies is a continuous one, adding that company has a policy of continual investment. “Most of our machines are less than five years old, as we are always striving to get faster, more accurate and more cost-competitive — and the only way to do that is to increase levels of automation and be up front with the latest machining technologies as they hit the market.
“Furthermore, we are not afraid of employing new techniques. While many companies in our sector are concentrating on traditional milling and turning, which we also do, we also take on higher risk processes to give us a very wide service offering. Having a wide array of grinding disciplines is just one of the capabilities that separates us from our competitors; and the fact that we embrace the latest technology is highlighted by our new grinding processes — and our use of the latest and very fast linear-drive grinding machines from Tschudin and Rollomatic. They are a means of reducing prices for our customers and help the company to grow.
“In fact, we are growing very rapidly. We have purchased another 10 acres of land next to our main production units here in Ireland; we have also opened a facility in Poland for specific machining tasks such as five-axis machining and mill-turning.”
Factory highlightMr King continued: “The grinding machines that we have purchased from AGS and already installed have become a centrepiece for us. They demonstrate the very high level of production machining that we do here and are delivering the highest level of quality for us; and although we manufacture parts in small volumes, we also get involved in true mass manufacture for certain components. This is why our recently ordered Tschudin and Rollomatic machines were specified with robot loaders that will allow them to run 24/7 loading parts from pallets. We have to be efficient, and with these machines we certainly are.”
The Rollomatic 630XW machine that is on order for Smithstown is designed for grinding many kinds of parts with complex geometries, and it is here that its additional sixth ‘A’ axis — ‘unique within the industry’ — provides ‘improved accuracy’ and the ability to incline the grinding wheels by up to 45deg. This capability avoids collisions, allows for easier programming, and ensures that demanding and highly precise geometric forms — such as those found on special medical tools — can be machined in a single operation. This machine will soon be joining multiple Rollomatic NP50 machines that are already in use at Smithstown.
The Rollomatic 630XW grinding machine accommodates parts from 0.1 to 20mm in diameter, has a high-speed multi-pallet pick and place loader with positions for up to 1,360 blanks as standard, and a six-position grinding wheel changer holding up to 24 wheels.
Chris Boraston, Advanced Grinding Solution’s managing director, says the synchronous grinding spindle motor provides constant rotation speed and torque regardless of the load on the motor. “This capability, combined with the latest linear motor technology, provides benefits that include enhanced surface finish and reduced maintenance costs. Furthermore, the oil that is used for cooling the linear motors is the same as the coolant oil, thereby ensuring constant thermal stability during production.
“The machine is also equipped with a touch probe that determines the exact location of the blank after clamping, thereby allowing the software to grind the component geometry according to the virtual centreline, thereby ensuring that a run-out of just 2µm can easily be achieved.”
Centreless approachRegarding Tschudin Cube centreless grinding machines, which have been specifically developed for grinding small components with diameters up to 20mm, Mr Boraston said: “These enable users such as Smithstown to achieve significant productivity gains, particularly as these machines are particularly quick and flexible regarding changeover times, which helps minimise machine downtime.
However, what sets the Cube apart from other models is its compact size and open design for easy access; users only need access to the rear of the machine to perform maintenance and servicing tasks, which means that several machines can be positioned together without any gaps.
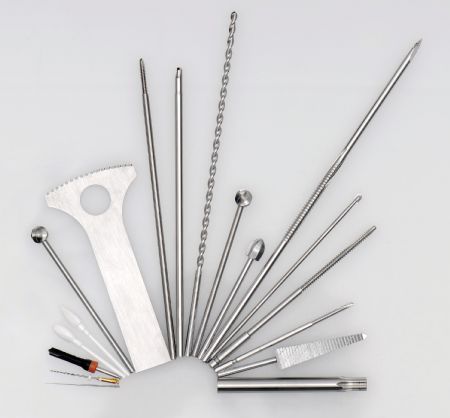
“Moreover, the Cube uses Tschudins patented W-axis, which sees the workrest blade mounted onto its own CNC axis — a design that allows parts to be loaded to the machine outside of the grinding area, making loading efficient, fast, and very safe. Traditional centreless grinding machines require parts to be loaded to a fixed work-rest blade that sits inside of the machine between the grinding wheel and control wheel, making loading difficult and changeovers more complex and therefore lengthier. In fact, Tschudin claims that the Cube is the world’s easiest and fastest centreless grinding machine to set up.
“Another huge benefit offered by Tschudin’s CNC workrest blade axis is that it allows multiple parts to firstly move to an initial position for a rough grinding operation to remove stock material quickly, then automatically be transferred to a second position for finish grinding. Indeed, it is possible to load five parts to the work rest blade and have a machine with 10 grinding wheels — five roughing wheels and five finishing wheels — with the parts being automatically transferred between the two sets of wheels.
Furthermore, with the option of workrest blade oscillation — backwards and forwards on its own CNC axis during the grinding process — fine finishes can be obtained from a ‘relatively rough’ grinding wheel, enabling high accuracy with the shortest possible cycle times.
“The Cube’s natural granite machine base and upper structure ensure high levels of thermal stability, along with high-precision for applications that include plunge-cut grinding, grinding of several parts in a single cycle, oscillation of the component during grinding, and throughfeed grinding. The Cube has a 150mm-wide grinding wheel, 205mm is an option, and the 12kW grinding spindle provide speeds up to 63m/sec. The Tschudin machines in use at Smithstown are equipped with Fanuc robots for unmanned shift work, whereby specialist medical parts are loaded from pallets, machined, and then placed back into pallets.”
Super-filtered coolantAdvanced Grinding Solutions says high precision grinding machines require the best possible filtration of the cutting oil, which is why the AGS-supplied Rollomatic and Tschudin machines were specified with Comat super-filtration systems from the Swiss company Elbaraon SA. These systems deliver ≤2-3μm filtration quality. AGS’s Mr Boraston says this level of performance makes filtered oil cleaner than unused oil as supplied new, while minimising lifetime running costs and maintaining maximum coolant consistency.
“Important for machine users is that Comat filter systems feature ‘Intelligent Performance Technology’ that allows them to be remotely monitored in real-time during manufacturing processes, with customers’ filter systems fine-tuned by Elbaron to ensure that the optimum filtration quality is obtained at all times. Today, more than 20,000 machine tools use Comat filtration systems, with some 120 million litres of metalworking oil being super-filtered every single day.”