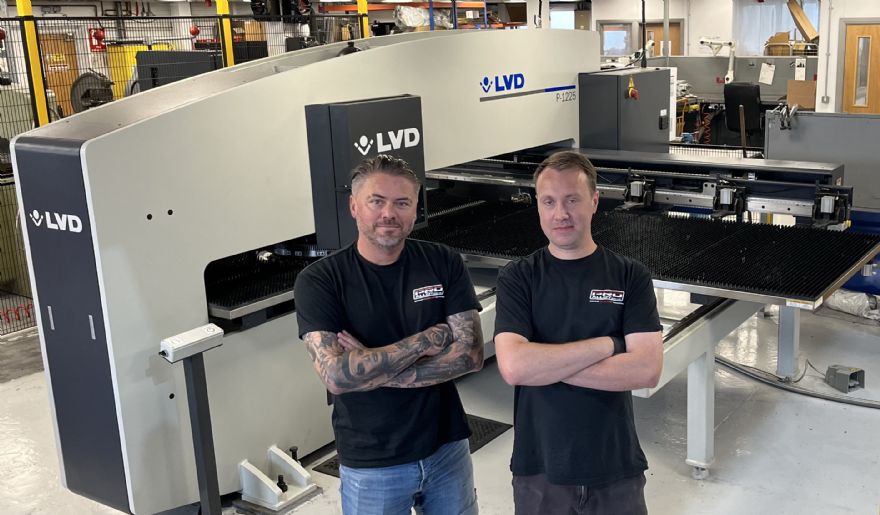
East Anglia-based
Pro Alloy Motorsport Ltd,, a UK based designer and manufacturer of alloy heat exchangers and specialist fuel system parts that supports customers in the automotive, motorsport, aviation, military, commercial and scientific research sectors, has increased production capacity at its East Anglia facility with acquisition of a new CNC turret punch from
LVD (UK) Ltd.
The LVD Strippit P 1225 machine replaces some ageing machines in the company’s heat exchanger core production department and is already providing some significant improvements to component accuracy, automation and production efficiency.
Alex Osborn, Pro Alloy Motorsport’s managing director, said: “We spent a lot of time evaluating different designs and specification of machine from various CNC punch manufactures, trying to understand which machine aligned best with our requirements and budget. The entire team at LVD provided an exceptional service from the initial enquiry stage through to final machine installation and operator training.
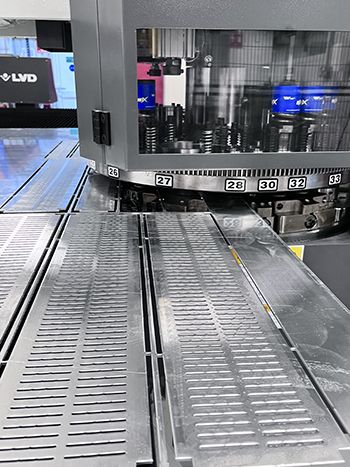
“This investment will provide us with a number of new capabilities and efficiencies in both our Heat Exchanger production facility and our main manufacturing departments. This is an exciting investment for Pro Alloy and significantly opens up a number of opportunities to further develop and expand the range and the type of products we are able to produce. This particular machine is equipped with a full 360 degree rotational head which as well as providing conventional punched components, also now enables us to produce CNC formed and rolled components very accurately and efficiently.
“As we venture further into the manufacture of cooling components for battery and EV applications, the versatility this machine is able to offer aligns perfectly with our low volume development projects as well as catering for the higher volume demands of our production parts. This combined with our in-house aluminium brazing facilities and our highly skilled fabrication team provides us with total control and amazing versatility”.
Pro Alloy production director Carl Nunn said: “Our heat exchanger production facility has already benefitted from some significant investment in new equipment, and the new punching capabilities really compliment this. Installing and commissioning the machine into our existing production areas was a challenging proposition, but the LVD installation team achieved this with very minimal disruption.
“LVD work very closely with the team at
Wilson Tool International and the collaboration between LVD and Wilson Tool ensured that our team were provided with very detailed and in-depth training and guidance on both machine operation, tooling selection and tooling use. Wilson Tool continue to provide us with very comprehensive support and advice, and the extensive range of standard tooling and custom designed tooling they are able to provide will enable us to really maximise all the features that the LVD Stippit P machine is able to offer.
“We haven’t yet maximised the full production capacity of the new machine, but the significant jump in production efficiency in just this one area of the business is already highlighting additional bottlenecks and other areas where we can streamline and improve our overall productivity with further investment in more advanced systems and technology.”