Mills BJ GT3100LBowers & Jones Ltd, a market-leading design and manufacturing specialist of high-precision roll tooling and equipment, established in 1954, has recently purchased with a Puma GT 3100L box guideway lathe supplied by
Mills CNC, the exclusive distributor of DN Solutions’ and Zayer machine tools in the UK and Ireland.
The new machine was installed at the company’s modern 15,000ft
2 manufacturing facility in Bilston, near Wolverhampton, in August 2023 and a Puma 5100B lathe and a DNM 750 II vertical machining centre equipped with a 4th-axis unit – in 2020 and 2021, respectively. The company has also ordered a new DN Solutions’ VTR 1216F large-capacity, heavy-duty vertical turning lathe, which it expects to be delivered and installed in the spring of 2024.
With business returning to pre-pandemic levels and the company winning new contracts to supply replacement roll tooling and associated equipment to steel and copper mill customers worldwide, Bowers & Jones is on a mission to streamline and strengthen its in-house machining capacity and capabilities to achieve real, tangible and sustainable growth.
The company, under new ownership since 2020, and led by managing director Jane Sommerville, is committed to continuous improvement and, as such, regularly monitors and benchmarks the performance of its manufacturing operations in order to identify ‘pinch points’ and production bottlenecks. A recent internal audit, undertaken at the start of the year, revealed an issue within its ‘small roll’ production operation and, in particular, highlighted the under-performance of an older mill-turn machine acquired some years earlier.
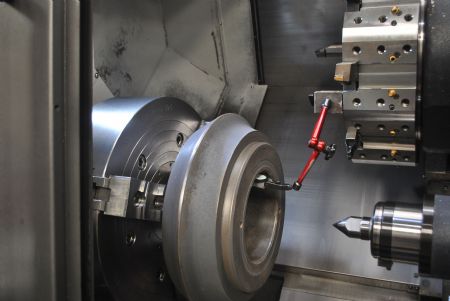
Ms Sommerville said: “The machine was purchased for a specific application we no longer manufacture. This meant that the machine, with its relatively small working envelope, had limited value going forwards and, owing to its age, was also unreliable and prone to break down.”
As a consequence, the company made the decision to trade in the machine, not for a replacement mill-turn model as one might expect, but for a new, two-axis horizontal lathe instead. Ms Sommerville explained: “Firstly, mill-turn machines are expensive. Secondly, the parts we manufacture, and the processes we have developed to manufacture them, means that it is often more efficient and effective for us to have standalone, independently-operated lathes and machining centres at our disposal. If and when required, parts can be easily transferred between our machines.”
Available for immediate deliveryAt the time, when Bowers & Jones was contemplating replacing the mill-turn machine by investing in a new machine tool, the company was approached by Mills CNC regarding a new Fanuc-controlled Puma lathe it had in stock. The machine in question was a 15in chuck Puma GT 3100L long-bed, box-guideway lathe equipped with a powerful, high-torque, belt-driven 35kW/2, 800rev/min 1613N-m spindle and a 12-station turret with a maximum turning length of 1,275mm and a maximum turning diameter of 481mm. Furthermore, it was also available for immediate delivery.
Ms Somerville added: “Although somewhat fortuitous in retrospect, the GT 3100L fitted the bill perfectly for machining our ‘small/medium-size rolls’ and components, so we decided to place the order for the new lathe once we had sold the mill-turn machine and secured the appropriate funding.”
Having previously invested in DN Solutions’ machines (formerly Doosan), the company had an already established relationship with Mills CNC. Ms Sommerville said: “We like Mills CNC’s proactive and informed business approach. The DN Solutions’ machines it sells and supports are technically excellent, reliable and competitively-priced, and the after-sales services they provide cannot be faulted. We rely on Mills to service our existing Doosan machines and use their ‘Mills CNC Finance Operation’ to help fund our machine tool investments too.”
Since being installed the GT 3100L has been put through its paces machining a range of high-performance, highly customised and application-specific replacement rolls and parts for new and existing steel mill customers. Characterised by their high-precision, tight geometrical tolerances and superior surface finishes, rolls designed and manufactured by Bowers & Jones are typically machined from high-quality forged tool steel billets in a range of batch sizes — from one- and two-offs, through to 200-off, depending on customers’ requirements. Rolls can also be manufactured from special quality iron and cast steels as well as aluminium bronzes and PM grades.
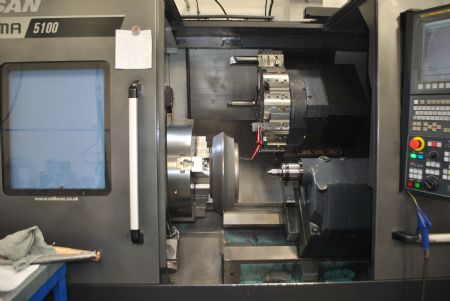
The rolls are first roughed-out on the Puma GT 3100L before being sent out for heat treatment to a number of hand-picked preferred suppliers, and is a process carefully managed by Bowers & Jones. After treatment, parts are returned and are then finish-machined back on the Puma, and if required, undergo secondary surface treatments — coatings, plating, shot peening and nitriding — before being dispatched.
Cycle times vary depending on the size of each roll and the required profiles and features to be machined. Larger and more complex rolls can involve more than 20hr machining time — roughing and finishing operations combined. Rolls are performance-critical components and are also consumable items. They are used in metal forming processes to enable steel stock to pass through one or more pairs of rolls, located on stands, in order to reduce the materials’ thickness, making it uniform and consistent and, where required, give the rolled material additional mechanical and application-specific properties required by the ultimate end-user.
The rolls are used to process the material into different products such as bar stock, rails and structural steel beams, angle stock and channel stock, which are used across many industries and sectors, includig construction, rail, energy, oil and gas, and automotive.
Harsh and demanding environmentsHowever, because rolls operate in steel and copper mills’ harsh and demanding environments, they are subject to high wear, thermal stress and mechanical fatigue. As a consequence, they need to be replaced regularly to maintain product quality and consistency, and ensure that the mills hit their own production targets and customer deadlines.
With almost 70 years’ experience of designing and manufacturing high-precision rolls for steel mill customers involved in the production of steel tubes, pipes, rails and sections, and rolls and wheels for customers producing copper rods and wires, Bowers & Jones works closely with all customers to design and manufacture bespoke and tailored replacement roll tooling and equipment.
The company’s success is built on its considerable know-how and expertise, and the care and attention it brings to roll design, the quality of roll material selected and machined, and the methods of manufacture adopted — all are critical to a roll’s performance and to its lifespan.
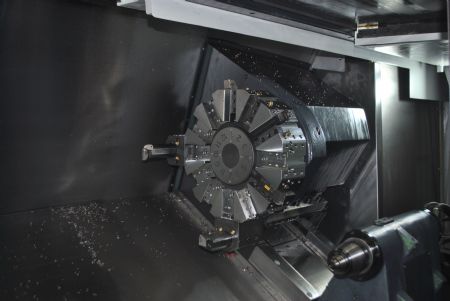
The company works in partnership, and collaboratively, with its customers and can design, manufacture and test (via simulation) roll tooling for customers’ new products, as well as helping improve established and existing product lines. The bottom line is that Bowers & Jones’ roll tooling solutions last longer and perform better than its competitors.
Ms Sommerville explained: “High-quality designed and machined rolls may cost a little more, but they are an investment and help customers save time and money by reducing re-profiling and replacement costs, limiting potential downtime caused by tooling changeovers, and by ensuring that customers’ mills keep rolling.”
Although the Puma GT 3100L has only recently been installed, such has been its performance over the last two months — and the performance of its two previously-acquired machines from Mills, that Bowers & Jones is continuing its investment programme by placing another order for a new DN Solutions’ VTR 1216F vertical ram-type lathe. This represents the company’s first vertical lathe investment. With its fixed cross-beam, wide-column and box guideway design, large 1,600mm turning diameter and 1,250mm length, and 45kW 400rev/min spindle, the VTR 1216F will enable Bowers & Jones to machine larger and heavier roll and ring-type components, including larger piercing rolls.
Ms Sommerville concluded: “Instead of clamping larger diameter rolls in a horizontal lathe which takes time and, if not careful, can lead to deformation and out-of-roundness during machining, the investment in the VTR 1216F, with its rigid design and large chuck, will enable us to machine these larger components much more effectively and help us to significantly reduce set-up and part-cycle times.”