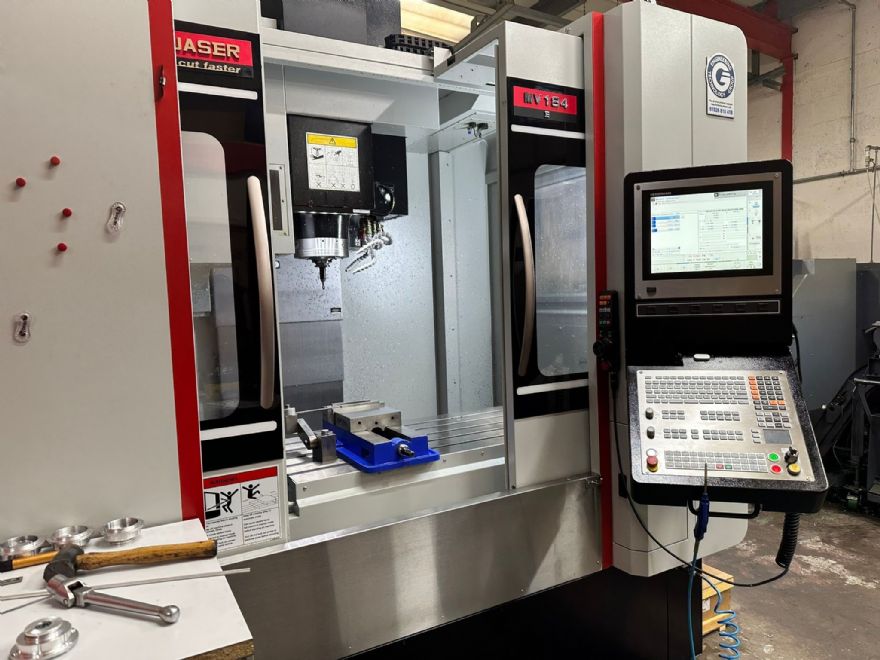
It is often the impulsive decisions in life that create an impact, and this was certainly the case for Chris Smedley, the managing director of Malvern Engineering Ltd. When he was made redundant over 14 years ago, he walked out of the factory and 45min later signed a contract for an industrial unit and thus Malvern Engineering was born.
This entrepreneurial spirit and level of determination have served the company well since its inception and they are still imbued in the ethos of the small business to this very day. So, when his regular machine tool dealer couldn’t offer the solution the business required, he approached the
Engineering Technology Group (ETG) and bought his first fourth-axis machining centre – a Quaser MV184 EV.
The journey for Malvern Engineering has seen the company manufacture everything from motorsport parts to military components. The company currently works with leading manufacturers in the automotive, aerospace, food and pharmaceutical sectors, through to the toolmaking and extrusion die industry – like a typical sub-contract manufacturer, Malvern Engineering will take on virtually anything that is thrown its way. This is why the company has opted to invest in a new Quaser machining centre.
Mr Smedley, who now employs seven people, said: “We are typically loyal to our suppliers, providing that the quality and service is to the levels we require. We were recently on the cusp of winning a large contract that required a fourth-axis machine for producing complex components – but our existing vendor didn’t have the solution we needed. We investigated the market and found a couple of suppliers, but it was ETG and the Quaser that won the day.”
Greater flexibilityHe continued: “We looked at a couple of machines, but when we visited the ETG technical centre and demonstration facility in Wellesbourne, we were impressed by the quality, service and the set up of the company. The Quaser MV184 EV offers us greater flexibility than our existing machine tools and it enables us to also reduce the number of required setups on complex parts. This is subsequently improving our quality, our throughput and creating greater efficiencies throughout the business.”
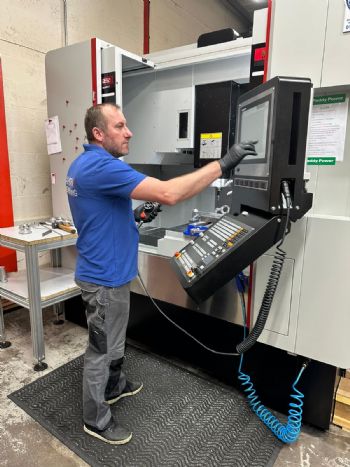
As a sub-contract manufacturer with four three-axis machining centres and two turning centres, the new Quaser opens the door to new types of work that wouldn’t have previously been possible. Mr Smedley continued: “The Quaser has a more compact footprint than our existing machines, which is invaluable to a small business where space is at a premium. Like our existing machines, the Quaser was supplied with a Heidenhain CNC control which creates familiarity for our team to interchange between machines. With the latest generation of control, we are finding a lot of new features that will help create even greater efficiencies as and when we gain familiarity with the system.”
The MV184EV incorporates a 1,200 x 600mm table with X, Y and Z-axis travels of 1,020 x 610 x 610mm and a maximum table load of 500kg, which can accommodate a wide range of components. With 40m/min rapids and a positional accuracy of +/-0.003 and repeatability of +/-0.002mm, the MV184EV is a fast and robust workhorse with impressive precision that ticks all the boxes for Malvern Engineering. The BT40 spindle taper and 30-position ATC enable Malvern Engineering to undertake robust machining cycles of all the diverse materials it processes.
Energy efficientETG machines everything from 304 and 316 stainless steel, mild steel, aluminium, titanium and many more challenging materials in quantities that range from a one-off prototype to small production runs. Alluding to how the attributes of the compact Quaser machining centre are enhancing component quality, Mr Smedley continued: “As a new machine, the Quaser is certainly more energy efficient while the kinematic movements of the machine and the fourth axis are also reducing cycle times and removing non-cutting time from component production.
“Added to this, the speed, efficiency and robust build quality are extending our tool life, improving our surface finishes and enabling us to essentially manufacture better quality parts with more aesthetically attractive surface finishes. We also do the majority of our programming offline with One CNC and the post-processors were readily available for the Quaser, making the integration of the machine into our business completely seamless.”
He concluded: “The machine has been a fantastic addition to our business and we haven’t had to lean on the ETG team that much so far. When we have needed their support, an engineer is available to resolve our queries almost immediately – as a sub-contract manufacturer that needs to get parts out of the door, that level of service will prove invaluable.”