KERAjet, a leading, international digital printing machinery manufacturer, based in Spain, has recently invested in a new, large-capacity gantry-type milling machine from Zayer, available in the UK from Leamington Spa-based
Mills CNC, the exclusive distributor of DN Solutions’ and Zayer machine tools in the UK and Ireland,.
The machine, an ALTEA 8000, with its large X, Y and Z-axis travels of 8,000 x 350 x 1,500mm, and an 8,000 x 3,000mm fixed table, is being used by the company to machine high-precision, complex components (machine frames, engine bridges and other performance critical parts) that go into its digital printing machines.
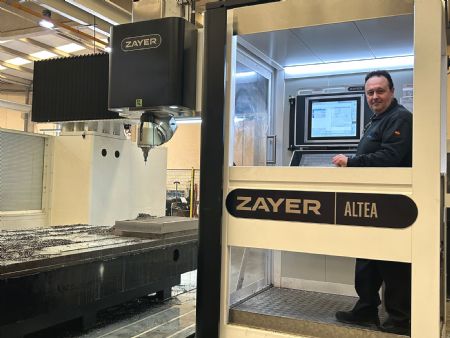
These machines, with their advanced electronics and innovative and intuitive software, are aimed at customers in the ceramics, textiles, glass and tableware sectors, and are renowned for their accuracy, flexibility, speed and reliability. There is high demand for the company’s digital printing solutions and to date, KERAjet has sold over 4,000 machines in 44 countries around the world.
The investment in the large ALTEA 8000, with its gantry configuration, has helped KERAjet’s business objective to achieve self-sufficiency, bring machining/manufacturing operations in-house, and control methods of production. The new machine enables the company to produce, more quickly and efficiently, production components, as well as wear and replacement parts.
Exacting surface finishesJose Luis Granell, KERAjet’s head of the machining workshop, said: “Our digital printing machines are accurate, but such precision can only be realised as long as the components that go into them are machined to the tight tolerances and exacting surface finishes, we and our customers expect and demand. It is worth bearing in mind that when it comes to our print head unit technology, our machines are working day-in, day-out for customers achieving accuracies in the hundredths of a millimetre, and even the nanometre range.”
Since installationm the ALTEA 8000 is working an 8hr shift but, if repeat components are being machined and the process used is secure and repeatable, it can be left to run unattended and operate through the night — significantly improving KERAjet’s productivity and its ability to hit customers’ stringent delivery schedules. In addition to its rigid design and build, and large working envelope, the ALTEA 8000 has also increased KERAjet’s machining flexibility.
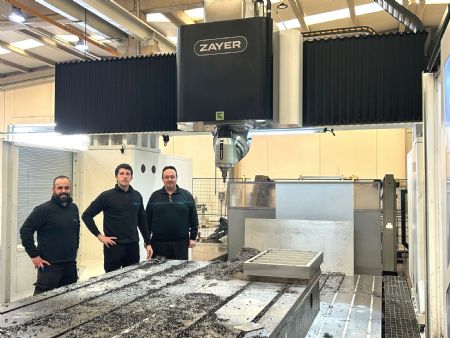
Mr Granell continued: “We can use the machine in pendulum mode machining workpieces up to 4,000mm in length in both work zones as well as machining longer parts using the full stroke of the machine. In addition, the machine is equipped with a number of heads (30 and 45deg). When machining aluminium, for example, we use the 30deg head with electro-spindle at 18,000rev/min. We use the 45deg head when machining steel and select the electro-spindle, if and when superior surface finishes are required.”
The ALTEA 8000 was supplied to KERAjet with a number of onboard software apps that have helped improve the machine’s performance and process reliability. These include the ‘iCAL’ app which, via automatic calibration, ensures the machining of highly-accurate geometries, and the ‘Fast Machine Protection’ app that eliminates spindle/tool collisions. Of particular benefit are the remote, real-time diagnostic and support that Zayer provides to KERAjet, and the HORUS NX facility that provides KERAjet with access to important machining and process data for future decision-making.
Mr Granell concluded: “We have developed strong relationships with Zayer, and they pulled out all the stops to get the ALTEA 8000 to us in double-quick time.”