The Hermle HS Flex pallet storage system in the foreground accommodates 12 300mm square pallets and the same number of 400mm square palletsMachining contracts for the civil aviation, defence and space sectors make up about 60% of turnover at Chandlers Ford-based
Ingenieur Ltd, with oil and gas accounting for much of the remainder. Turned parts production is only 30% of throughput, the rest being prismatic machining on seven vertical machining centres (VMCs). The most recent additions to the line-up are two German-built Hermle machines supplied in 2022 by Gosport-based
Kingsbury, Hermle’s sole UK sales agent, and they are the sub-contractor’s first five-axis models.
In 2015, Ingenieur moved to a larger, 12,000ft
2 factory unit more suited to hosting visits from aerospace supply chain clients and their customers. At the time, the management considered automating some of the milling to complement bar-fed turning on site, but the volumes did not justify it. Six years later, when Covid-19 restrictions were being lifted, the company became part of the CTN group of five sub-contractors across Hampshire, Kent, Cambridgeshire and Norfolk. New work was fed in initially by other group members and the Chandlers Ford operation swung quickly from being quiet, with some operators on furlough, to extremely busy.
Unattended runningTo alleviate a bottleneck in production, a refurbished Hermle C 40 U arrived at short notice in February 2022, on loan from Kingsbury. That machine was subsequently purchased and a new Hermle C 400 followed hot on its heals in the June of that year, linked to one of the machine manufacturer’s own HS Flex systems for exchanging 24 pallets automatically, allowing long periods of unattended running. The machining centre is equipped with an 18,000rev/min spindle, through-spindle coolant, an extended magazine to accommodate 90 tools, Blum tool measurement and breakage control, and a Renishaw touch probe for workpiece datuming.
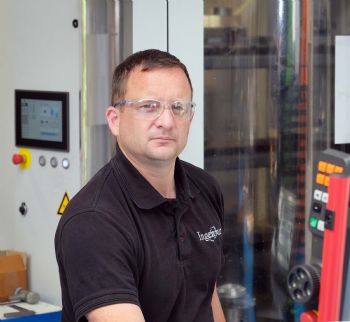
Ingenieur’s general manager Chris Barton (pictured left) explained: “Before the two Hermles were installed, we were quoting and winning a lot of new business in a number of industry sectors. In a short space of time we gained four additional contracts, so extra milling capacity was needed really quickly, which thankfully Kingsbury was able to supply.”
One of the contracts involved machining relatively large quantities, between 1,000 and 1,500, of each of 20 different parts from aluminium billet for a US firm in the security sector. However, the sub-contractor was operating only a single day shift, 39hr over a five-day week, which was not enough to cope. Consideration was given to introducing a second shift, but automation was the favoured route to increasing capacity. Five different options were considered.
The trunnion-type Hermle five-axis VMCs were chosen due to their high quality build, the proximity of Kingsbury for providing service and after-sales support, and also because the machines could be supplied with a Heidenhain 640 control to enable programs from the other VMCs on the shopfloor, all of which are fitted with the same make of CNC, to be run with very little editing.
Seamless connectionEven after the machining platform had been decided upon, there was still debate concerning whether to use an HS Flex or a third-party pallet storage and retrieval system. The former was selected owing to seamless connection with the machine, as well as the flexibility of sequence planning and order management using the touch-screen interface of the pallet store control, which is linked into the Heidenhain CNC system.
Ingenieur’s bespoke tower is able to present parts to the C 400 spindle by swivelling the trunnion through 90degOnce the new milling capacity was operational, the efficiency of production at Chandlers Ford was transformed. The security sector contract involved tens of thousands of parts requiring 30 to 90min cutting cycles to be delivered to the USA over a 12-month period. Three months in and the work was already behind. After the Hermles came on-stream, Ingenieur quickly caught up and by the 11th month, the sub-contractor had not only eliminated the backlog but was well ahead of schedule.
Mr Barton continued: “The HS Flex automation is very adaptable and easy to use. During the day when operators are present, we set it up to run components requiring fairly tight tolerances down to ±0.01mm. If a rush job comes along, it is a simple matter to load the parts into the pallet store, transfer the program and run off the parts. At the end of each day shift, we load the pallets with work and leave the system to operate unattended overnight with total confidence. Generally, during ghost shifts we process components requiring a more open tolerance, typically ±0.05mm.
“The machine works like that non-stop from first thing Monday morning until mid-morning on Saturday. I estimate that an operator is in attendance for just 3hr a day, loading and unloading pallets and transferring programs. For the rest of the time, the production cell runs fully autonomously.”
Short cycle timesProduction within the automated Hermle cell after the US contract had finished was significantly different. Stainless steel and Inconel were machined in addition to aluminium, batch sizes were smaller at 50 to 500, and cycle times were considerably shorter at about 5min.
Cycles in the Hermle C 400 are mainly 3+2, with the occasional requirement for full five-axis interpolationSo Ingenieur bought an iron casting and machined it to a bespoke design to allow a mix of multiple jobs to be mounted on each pallet for overnight processing. Normally found on a horizontal machining centre, the tower is able to present parts to the VMC spindle by swivelling the trunnion through 90deg.
The sub-contractor has found that automation allows scarce setter-operator resources to be spread efficiently throughout the factory during the day. With the current difficulty in recruiting skilled staff, few manufacturers have the luxury of deploying one experienced person onto just one or two machines. Equipment like the HS Flex allows apprentices and less proficient staff to monitor production while it is running. It also maximises productivity, as idle times are short due to quick load/unload times.
Mr Barton concluded: “You couldn't ask for a better automated production cell than the Hermle – it is brilliant. The equipment is productive, accurate and user friendly, and if we have a difficulty or query, nine times out of 10 Kingsbury sorts it out quickly over the telephone. We would have no hesitation in buying a second cell if production volumes warrant it.”