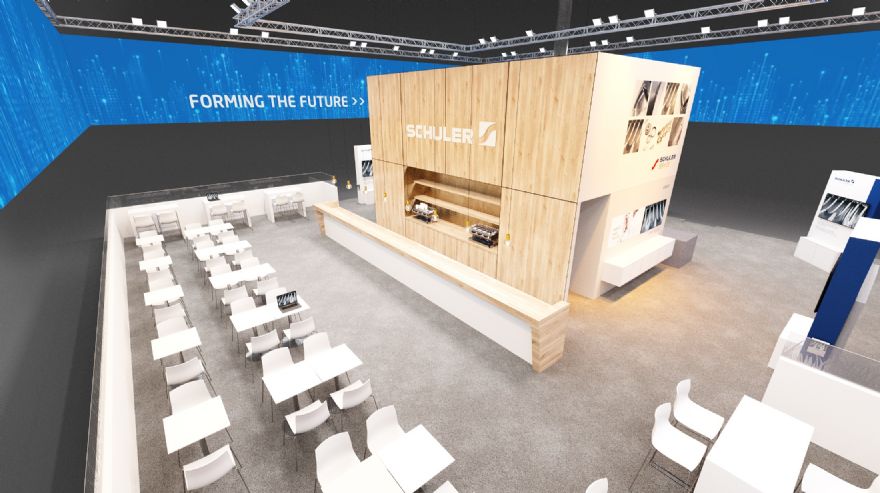
The sheet metal processing industry is subject to constant change, with production systems needing to not only run reliably and deliver high levels of output and quality but also be quickly reconfigured for other parts. Other requirements such as sustainable operation and a high degree of digitalisation have also emerged.
The global press-manufacturing company
Schuler and its toolmaking subsidiary AWEBA will be demonstrating how these goals can be achieved with their solutions at
EuroBLECH, under the motto ‘Forming the Future – Reloaded’ (Hall 27, Stand G82).
A car door made of high-strength aluminum that was produced using a new hot stamping process will be on display; and because the part is actually heated in the press, the furnace previously required for this is no longer needed — and with it around half of the energy input (an automotive supplier in Asia is already using the new lightweight construction technology on a hydraulic press line).
In the field of electromobility, Schuler now offers the Backlack process to manufacture ‘rotor and stator stacks for traction’, where the individual electrical sheets are stacked after being punched out and put into a bonding station, which joins the sheets with a combination of temperature and pressure. In contrast to other production processes, the insulation remains undamaged and therefore the magnetic properties of the drive are unaffected. Schuler says a German automotive supplier can produce up to 80,000 rotor and stator stacks per year on such a fully automated line.
Visitors to the Schuler stand will also learn about the latest digital solutions for forming technology, those that help to improve cost-effectiveness, availability and energy efficiency in the press shop — even if the individual systems are from other manufacturers.