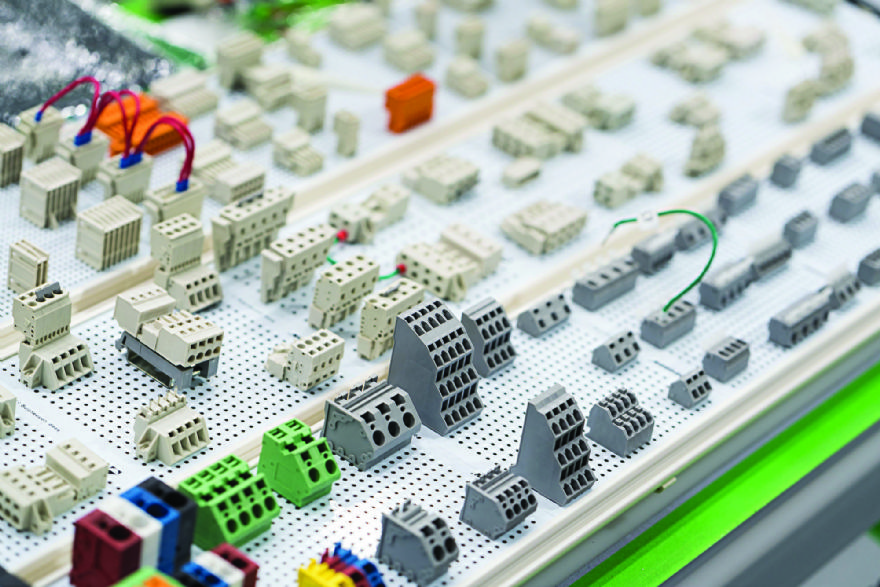
Laser ablation technology is providing a distinctive edge in the manufacture of electronic components for the ICT (information and communication technology) industry, which — like the medical sector — is under increasing pressure to constantly miniaturise components while at the same time increase their performance. This constant pressure has repercussions for the entire production chain, and on the manufacture of tools required for producing electronic micro-components.
As a result, companies are looking for solutions that allow them to simplify increasingly complex processes, reduce ever rising costs, and support an increasingly scarce skilled workforce, with many adopting laser ablation technologies and advanced processes of the type offered by Coventry-based
GF Machining Solutions Ltd (GFMS).
The company said: “The growing complexity of electronic components is pushing some traditional technologies like EDM and milling to their limits. For the most complex applications, laser ablation technology — used either in combination with these more traditional machining technologies or replacing them altogether — seems to offer a viable and profitable way forward. This technology is even more relevant with micro-machining applications and the machining of micro-cavities used in the manufacture of those micro-components that play an essential role in the mass production of electronic devices.
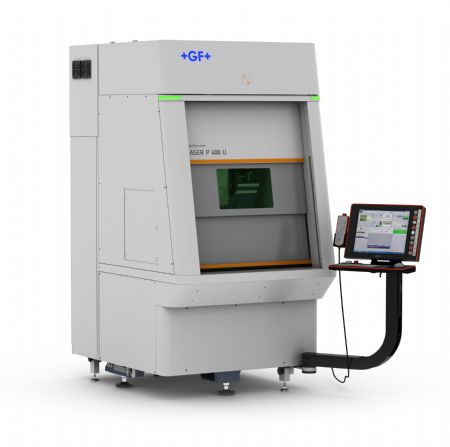
“In the highly competitive world of mould making, the traditional process of manufacturing mould tool inserts for electronic components combines milling with wire-cutting EDM and/or die-sinking EDM. This typically requires multi-step operations, along with the production of many electrodes, each of which can require long set up and machining part cycle times, and the skills of experienced operators.
“With companies having to design and manage multiple processes involving cutting tools, electrodes and handling equipment, each individual step within these processes can produce mistakes and alignment issues; and the use of die-sinking machines or high-precision five-axis milling machines requires operators with experience, knowledge and skill — capabilities that can be difficult to attract and retain.”
Time-consuming processesGFMS continued saying that traditional processes, like EDM, can be long and costly due to the machining of electrodes and hard metals. “Moreover, traditional technologies focus on one type of machining only, making it difficult to jump quickly to new applications, new materials and new processes, and this is a barrier for OEM customers looking to produce new types of parts faster, better and economically.
“Then there is the processing of non-conductive materials. These include ceramics, such as silicon carbide, which are increasingly used in the EC industry; and while it is difficult to keep this material smooth and consistent without deviation — and even be impossible to machine using traditional technologies — advanced laser technologies can offer a solution by either combining with, or replacing, traditional technologies.”
GFMS says laser technologies have already begun to enhance tooling applications with their ability to create complex, high-quality moulds not only for connector parts used in the electronics industry, but also in the manufacture of micro-cavities or micro-components, with laser technologies using nanosecond and femtosecond pulses dominating laser machining.
“Nano-lasers with nanosecond pulse technology have been around for a while and still have many uses, but it is femto-lasers with femtosecond pulse technology (a femtosecond is one-billionth of one-millionth of a second) that look set to dominate the electronics sector in the future, having the ability to combine high precision with burr-free ablation.
“Moreover, lasers offer many advantages over EDM, including: no consumables such as electrodes being required; the ability to machine non-conductive materials; being able to achieve uniformity and consistency over large machined areas; and the ability to reproduce functional textures. Likewise, lasers offer advantages over milling. Again, no consumables are required; and being a contactless technology, hard and brittle materials can be machined with burr-free results — plus small, intricate features and details can be machined.”
Effective combinationGFMS says the combination of laser roughing and machining with die-sinking EDM enables manufacturers to shorten production times and reduce costs while reaching the desired part surface qualities. “This combination of technologies delivers the optimum results when engraving deep cavities that cannot be reached by traditional subtractive processes.
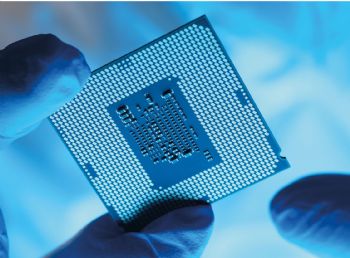
“With a combination of femtosecond laser and die-sinking EDM, manufacturers can achieve much faster and more economical processes that eliminate the need for milling operations, cutting tools, and many of the electrodes that an EDM process requires. Indeed, lasers achieve highly repeatable quality in engraving mould cavities, with none of the associated risks of tool breakage that traditional subtractive processes can encounter.”
One combined technology solution that highlights the benefits of combined laser and EDM processing applied to electronic connector moulds is GF Machining Solutions’ five-axis AgieCharmilles Laser P 400U machine. Capable of single-setup operations that can include laser texturing, blasting, engraving and marking, the system is designed for an easy transfer of workpieces using the company’s System 3R automation and workholding technologies.
Indeed, using one of these machines in conjunction with EDM finishing, an automotive customer revamped its production processes and shortened its lead times on moulds for electronic connectors from roughing to pre-finishing by a factor of five.
“This manufacturer’s previous EDM process to create electrodes for its die-sinking operations required a total of 15hr. The new process, using laser ablation, delivered the same accuracies but took only 12min to rough and pre-finish the moulds, and a further 4.5hr for EDM finishing.
Moreover, customers that purchase femtosecond laser equipment for one application — such as producing electronic connectors — can use the same equipment to tackle other projects that previously exceeded their capabilities. Furthermore, typical femtosecond laser equipment occupies a small footprint, which not only saves space on the factory floor but also enables customers to upgrade their procedures and still make room for other operations or processes.
“In conclusion, our Laser P 400U, LaserCAM software and femtosecond technology can help customers to reduce the die-sinking EDM process or avoid it completely; and thanks to a fully digitalised process, 80% of the job is done on the CAD/CAM and on the laser parameter development.”