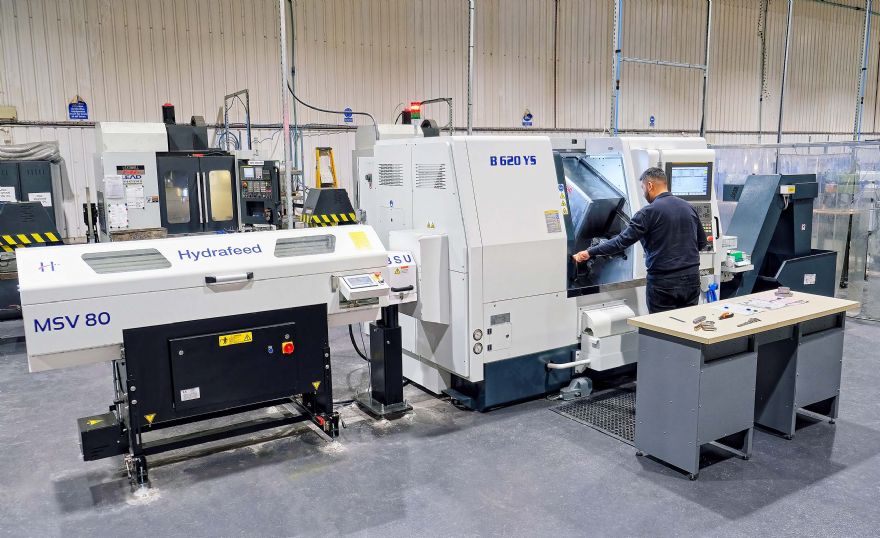
Birmingham-based architectural ironmongery manufacturer
Instinct Hardware has spent more than £500,000 in the last two years on a manufacturing execution system, a powder coating plant, a water jet cutting machine and an Italian-built Biglia bar-fed, twin-spindle lathe with a turret having a ±45mm Y axis and 15 driven tools.
It is the sixth CNC lathe and by far the most capable to be installed in the 68,000ft
2 factory in Stirchley, where premium quality (commercial Category A fit-out) door knobs and handles, door stops and accessories are manufactured, predominantly from 316 stainless steel.
The latest Biglia turning centre was sourced in May this year from Kenilworth-based
Whitehouse Machine Tools, the sole UK agent for Biglia, which supplied the machine as a turnkey package with a Hydrafeed short bar magazine for feeding 1.5m long stock up to 80mm in diameter, and a gantry-type system for unloading components onto a conveyor.
Instinct Hardware director Nil Chohan in front of the Biglia latheThis handling method was chosen to prevent damage to the surface of components and hence preserve their aesthetic appearance after they have subsequently been polished by hand to a mirror or satin finish. Supplied also by Whitehouse were programs and tooling for the production of two key components and their prove-out in Kenilworth, plus the provision of comprehensive training, which is unlimited and free-of-charge for the lifetime of the machine.
Instinct Hardware products, which are either standard catalogue items or manufactured to customers' bespoke designs, have been or are being used in many prestigious projects. They include the ongoing refurbishment of Citibank UK’s London base, Google’s new headquarters in King’s Cross, various London Underground stations, the recent renovation of Wembley Stadium and Liverpool FC’s modern training centre.
Conveyorised handlingUntil now, stainless steel has accounted for 80% of production, with the remainder mainly brass and bronze. However, an increasing amount of aluminium is being processed due to its easy recyclability, a material that will benefit even more from the careful, conveyorised handling. Timber handles with stainless steel cores are also on the rise. Marketed under the Mirage brand name, 25% of production ends up in overseas markets, exported either directly or indirectly.
Working area of the twin-spindle, single-turret Biglia B 620 YS, in which components are turned, milled, drilled, tapped and broached from bar, exiting the lathe after reverse-end operations are completed in the sub spindle, without ever needing to be set up again on another machineNil Chohan, one of the manufacturer’s second-generation directors, said: “Since we moved to our current premises, we have been steadily increasing our machining capacity with a view to reducing our reliance on sub-contractors, which is now virtually zero. All of our lever handles require a square hole to be broached. This has always been done here in a separate operation on a hydraulic press, as before the Biglia B 620 YS was installed, we did not have a lathe on the shopfloor rigid enough to perform this operation.
“We bought the Italian turning centre specifically because it is able to broach our stainless steel handles, which Whitehouse demonstrated to us before we committed to the machine. So we can now perform all operations in ‘one hit’, rather than in five or six operations using our previous production process. It significantly reduces scrap rate by avoiding repeated manual setups and greatly speeds manufacturing time, enabling us to fulfil more easily our promise to customers of a 10- to 14-day order turnround.”
A case in point is the machining of a component that is assembled into a stainless steel, oval-profile, mitred lever handle. It previously required six machining operations: turning on a two- or three-axis lathe, milling and drilling on one of four vertical machining centres (VMCs), broaching on a hydraulic press, further prismatic machining on a different VMC, slotting on yet another VMC (which could have been carried out on the previous machine, but the overall cycle would have been too long to achieve the required takt time), and mitring on a bandsaw prior to welding.
Eight-fold time savingAll of this consumed a total of 15min machining time plus 10min or more handling and set-up for each of the five additional operations, amounting to well in excess of 1hr overall. On the Biglia, the part comes off complete in 8.5min, representing about an eight-fold time saving, with the added benefit of elimination of in work-in progress and the attendant potential for damage to components.
Mr Chohan visited the Biglia factory in Italy with a Whitehouse sales engineer to see the lathes being built and get a sense of the quality of manufacture. Needing a strong, powerful machine capable of broaching stainless steel, he was impressed by the specification of the B 620 YS, in particular the 30kW direct-drive, liquid-cooled main spindle motor offering 700Nm of torque.
Part of a stainless steel, oval-profile, mitred lever handle is shown in the background. It is pictured with the constituent component (front right) that is now machined in one hit on the Biglia lathe rather than in six separate operations. Front left is a stainless steel coin slot bathroom release rose, whose slot is milled using the Biglia's Y-axisHe was told that the latest design of this 6.5-tonne machine incorporates a massive, cast iron machine bed that has been reinforced by 20% compared with the model it superseded. It is notable that to promote rigidity and accurate machining, the lathe has box ways in the X and Y axes, with a linear guide rail in the Z-axis for speed of traverse.
In a recent development, he mentioned that under the trading name of Instinct Hardware’s parent company,
Creative Manufacturing, a sub-contract prototyping and manufacturing venture has been embarked upon. A full service is offered encompassing design, machining, powder coating, shot blasting, assembly and packaging. It is early days and projects completed so far have involved waterjet cutting and painting, but all of the current 10 CNC lathes and machining centres on the shopfloor are also available for deployment.
Mr Chohan concluded: “Reputation is hard to establish but even more difficult to maintain. Through hard work and endeavour, we have become a leading European manufacturer of bespoke architectural ironmongery. Today, our team is committed to continued investment and developing our range and brand further, with increased focus on sustainability of materials and logistics. We are constantly looking at new machinery like the Biglia to develop and enhance our offering, while maintaining our passion to continue driving the company and our industry forward.”