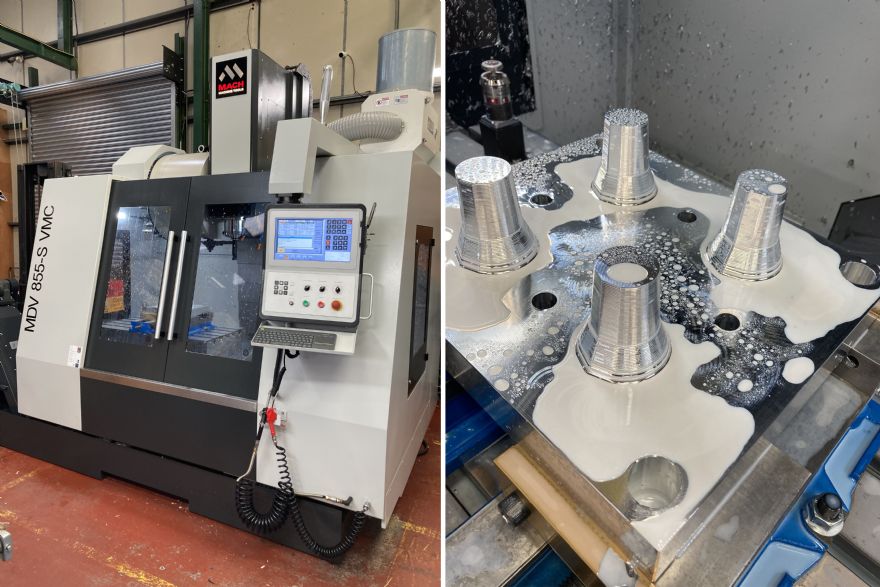
Northamptonshire-based
Great Central Plastics Ltd (GCP), a leading sustainable injection moulding specialist, has recently invested in a new three-axis vertical machining centre (VMC) supplied by
MACH Machine Tools Ltd,, the CNC and manual machine tool and machine shop equipment supplier to UK, Irish and European component manufacturers and mould tool and die makers.
The new machine, a DynaPath-controlled MACH MDV 855-S, was installed at GCP’s 10,500ft
2facility in Woodford Halse in December 2024, and had a direct and immediate impact on the company’s toolroom productivity, improving floor-to-floor times and optimising process efficiencies.
The MACH MDV 855-S is the first, production-oriented CNC-controlled machine tool GCP has acquired in its 27-year history and has been positioned in the company’s toolroom adjacent to a number of manual and semi-auto machines. Since being installed, it has been put through its paces machining a range of high-precision mould tool components, including bolsters and plates, cavity and core inserts and supporting fixtures, for GCP’s custom-designed and built mould tools which are designed and manufactured in-house in close collaboration with its customers.
Furthermore, the company offers expert Design for Manufacturing (DfM) consultancy services to customers in the planning and pre-production stages of every project to ensure that desired plastic parts can be manufactured quickly, easily and cost effectively. Pre-production services also include rapid prototyping utilising 3-D printing technology for design validation and testing and, in some cases, as a cost-efficient solution for low-volume production runs. For higher volumes, metal mould tools are designed and machined from a wide variety of materials that include aluminium, P20 steel, hardened steel (H13), and corrosion-resistant stainless steel.
‘State of the art’ mould shopGCP’s mould tools are complex, high-precision and performance-critical engineered solutions renowned for their innovation, accuracy and reliability. They are characterised by their tight, tied-up geometrical tolerances and exacting surface finishes and, having been machined, inspected and signed-off, are moved from the toolroom to the company’s ‘state of the art’ mould shop which is geared up to manage quick tool and material changeovers.
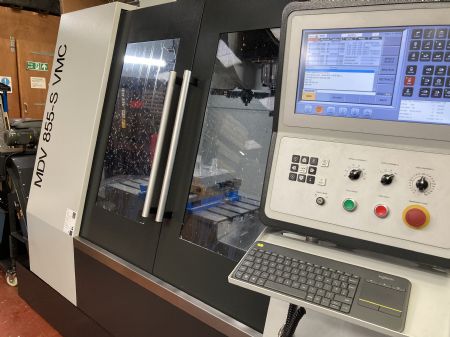
The manufacturer’s mould shop has 14 injection moulding machines at its disposal with different capacities and capabilities, and it also features a range of finishing equipment, such as pad printing systems and hot foiling machines.
GCP’s investment in its new MACH MDV 855-S VMC followed a company-wide review, conducted last autumn, into all aspects of its design and production operations and processes. The review highlighted that the company’s toolroom operation needed to be strengthened and, in order to improve existing mould tool manufacturing efficiencies and throughput, as well as being able to handle new and more complex mould tool manufacturing in the future, the machining capacity and capabilities of its toolroom needed to be improved.
Kiron Phillips, GCP’s business development director, said: “We are a successful company committed to growth through continuous improvement. As such, we regularly monitor and benchmark operational performance against KPI’s to identify actual and potential pinch-points and bottlenecks, and to address any issues that can or could affect quality, lead time fulfilment and cost efficiencies.”
‘Right-first-time’ mould toolsHe continued: “Our toolroom is pivotal to our success and is the place where new mould tools are manufactured, and older tools are maintained and repaired. The toolroom effectively ‘feeds’ our injection moulding machines with high-quality, ‘right-first-time’ mould tools. If the toolroom’s not working to full capacity – neither are our moulding machines.”
As a consequence, following the review, the company made the decision to invest in a new CNC machine tool because, according to Mr Phillips: “We simply could not allow our toolroom to be the weakest link in our process chain, moving forwards.”
Prior to investing in the MACH 855-S, the company first did its homework and researched the market. Phil Brown, GCP’s toolroom manager, said: “We talked to lots of people including other toolmakers about the type of CNC milling machine we were looking to acquire, and also about the CNC machine tool supplier we would be acquiring it from.”
GCP drew up a technical specification for the new machine that included: the preferred table size to comfortably handle GCP’s standard 20 tonne (246 x 246mm) and 50-tonne (346mm x 296mm) mould tool plate sizes; the optimum spindle power and speed range that would enable the company to machine the different materials used for its tools and cope with its high-speed mould tool engraving requirements; and the ideal tool changer size that would help GCP improve part cycle times and reduce time and costs associated with tool changeovers and labour interventions. Mr Brown added: “As this was going to be our first CNC machine we were also interested in the scope and scale of the different suppliers’ after-sales services and support that could be provided.”
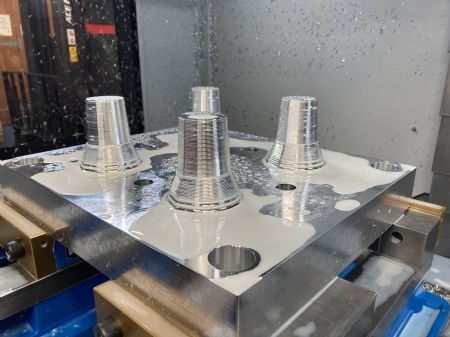
One of the companies GCP contacted was MACH Machine Tools. Following a visit to MACH’s Bristol facility, where an ex-demo MACH MDV 855-S was introduced to GCP representatives, the company was invited to take part in a ‘test cut’ - machining a complex mould tool cavity on the proposed MDV 855-S. Mr Brown continued: “We were impressed with the machine’s ability to deliver the accuracies, surface finishes and processing speeds we were looking for and, once the finance and delivery details were agreed, placed the order for the MDV 855-S.”
MACH Machine Tools’ MACH MDV 855-S is a rigidly-designed and built, high-precision and flexible three-axis VMC supplied with the advanced DynaPath CNC control. The machine is equipped with a generous-size worktable (1,100 x 500mm) and a powerful 11kW/12,000rev/min BT40 direct-drive chilled spindle, with a through-spindle coolant capability, as well as a 24-tool position ATC and impressive 36m/min rapids on its X , Y and Z axes.
Inherently versatile Dynapath controlThe machine’s user-friendly and powerful DynaPath control with 15.6in LCD touchscreen is inherently versatile and is capable of accepting multiple program formats via its in-built USB, ethernet and wireless interfaces. It can be used for conversational programming (as well as ISO programming), and has 8GB of memory and a 10,000 block look-ahead capability for fast and smooth contouring and profiling. The control also enables customers to access MACH Machine Tools’ 24/7 (Wi-Fi) remote service and support facility for real-time diagnostics, trouble-shooting and for application help and advice.
Mr Brown said: “The remote assistance function is really useful, and I have had occasion to use it when I had an issue with the machine’s ATC. I had made a programming error but, after logging into our company’s account was able, via the ‘What’s App’ link, to talk directly to MACH Machine Tools’ technical support to solve the problem quickly — minimising downtime and negating the need for a service visit.”
Although the MDV 855-S has only recently been installed in GCP’s toolroom, it is already making a big difference to the company’s productivity and process efficiencies. Mr Phillips concluded: “The new machine is proving to be a great investment. We are now able to manufacture our mould tools, and their constituent parts, faster than before. This has helped improve our floor-to-floor times and customer lead times too as our injection moulding production operation is no longer ‘waiting’ for mould tools to be finished.”