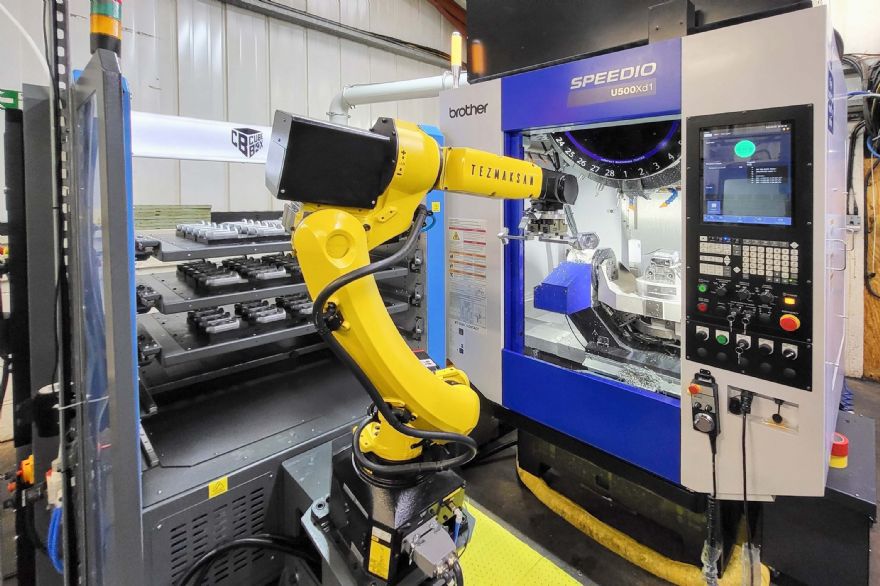
Wiltshire-based
Atkinson Equipment Ltd, a leading OEM specialising in the design and production of equipment for oil heating and diesel tank applications, in addition to being a sub-contract engineering firm, has dramatically reduced its lead times following investment in a Brother Speedio U500Xd1 five-axis machining centre equipped with Tezmaksan CubeBox automation supplied by
Whitehouse Machine Tools (WMT), Kenilworth.
Adam Walford, Atkinson Equipment’s engineering group sales manager, explained: “The automation solution from WMT has increased our productivity dramatically. We have typically halved lead times from 12 weeks down to six for complex sub-contract parts and reduced them even further when making components for our own products, say from a month down to one week.
“Since automating the milling side of the business, we have also seen a reduction in the bottleneck we previously had when parts arrive from our turning section for prismatic machining. Our ability to get product out of the door to our customers is through the roof. It is helping us to win new business in the sub-contract area, as well as to grow our OEM division.”
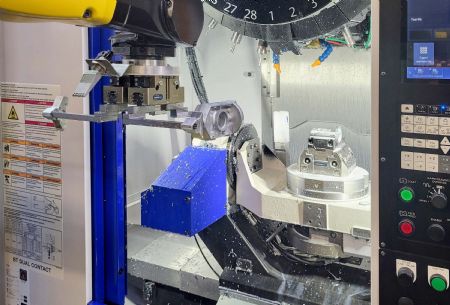
Atkinson Equipment, which is based in Westbury, is required to manufacture large volumes of parts for its own refuelling and liquid transfer products, which it has been doing for over 50 years. It also needs to produce a high mix of smaller volumes for the sub-contracting division, which has been running for half that time, but which is growing rapidly. This dual role places significant demands on its manufacturing capabilities and was pivotal in the decision to invest in an automated Brother-Tezmaksan cell.
The relationship with WMT began in 2019 with the purchase of a Brother five-axis CNC machining centre, a Speedio S700X1 equipped with a Lehmann rotary-swivelling compound table. This initial investment allowed the company to machine complex parts on multiple faces in a single setup, significantly improving efficiency. Having experienced the benefits, Atkinson Equipment went on to buy a Brother Speedio M200Xd1 trunnion-type five-axis machining centre in 2023, initially to manufacture a complex aerospace part.
Potential of automation realisedAt first, the idea was to automate the existing S700X1 on-site with the Tezmaksan CubeBox, but this would have necessitated an upgrade to the Lehmann equipment to provide pneumatic supply for automatic clamping of parts. However, a visit to the WMT showroom in Kenilworth revealed the potential of automating a Brother U500Xd1 five-axis machining centre instead, as this was the configuration being demonstrated.
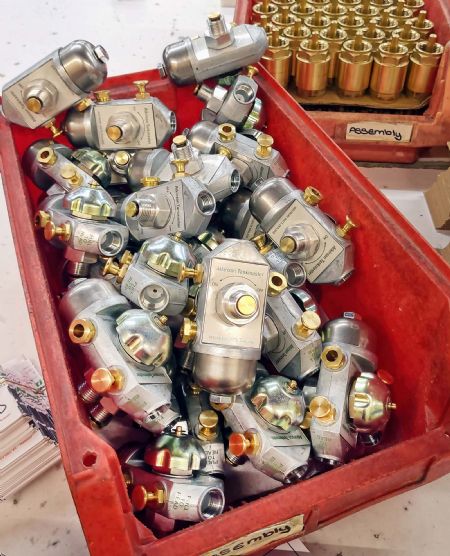
Mr Walford explained: “Looking at the cost differential between just the Tezmaksan compared with the automation plus the U500Xd1, it made sense to go for the automated set-up complete with the new five-axis machine. We needed extra capacity anyway, so it made absolute sense for us, especially as it was more affordable than we anticipated.”
The Brother U500Xd1’s large working volume for the compact footprint, 28-tool automatic toolchanger (ATC) capacity and integrated rotary joint for pneumatically actuating the fixtures proved ideal for Atkinson Equipment’s production needs. WMT provided comprehensive support during the set-up process, assisting with tray template design for holding raw material and finished components, as well as the end-of-arm tooling with double grippers for handling them. The automated cell’s sensors create a safe working environment, without the need for traditional guarding.
Mr Walford concluded: “It was quite daunting at first taking on a completely new piece of technology like this, but we were confident with the support that we would get from WMT and its ability to guide us through the process to where we are now. The relationship with this machine supplier is key. We are very happy with WMT’s service and support, it is excellent, and gives us confidence to keep buying from them.”