From left to right: Studer’s management team: Stephan Stoll - COO; Sandro Bottazzo - CEO; and Daniel Huber - CTOStuder, the Swiss manufacturer of high-quality precision cylindrical grinding machines, improved its market position worldwide in 2024, driving forward technological innovations and further increasing operational efficiency. A press conference was held live from the Fritz Studer AG studio in Steffisburg on 27 March with an online audience of international media representatives in attendance, including
Machinery Market’s online editor John Hunter.
Jens Bleher, who has been CEO of Studer since 2018 and has just joined the management of the
United Grinding Group as COO (effective 1 April), said: “Thanks to the high diversification of our portfolio, we can look back on a solid financial year with growth in several markets and industries.”
“The challenging economic and geopolitical environment required particularly intensive efforts, as Mr Bleher explained: “In addition to quality, the focus of activities at Studer is on increasing productivity, intensive cost management, and the introduction of new, innovative technologies. Studer remains a reliable partner for our customers and sees itself in an excellent position to face global competition.”
Mr Bottazzo, who has now replaced Mr Blher as CEO and chairman of the management board, explained that Studer maintained its market share worldwide and even expanded it in some countries and regions. He said: “We are continuing to expand our leading position in the universal cylindrical grinding machine market step by step.”
He explained that the development of new customers was very positive, with a year-on-year increase to around 43%. Strong segments were the Asian automotive and supplier industry, tool and die, and the machine tool industry. Studer also continued to expand its presence in the aerospace sector and strengthen its market position, similar to the previous year. Overall, order intake was only slightly below last year‘s figures, as the company had anticipated.
Studer received strong orders from North America, while Asia, which remains the largest sales region, and the Latin, and some European countries also posted strong results. By contrast, Central Europe, and Germany in particular, fell short of expectations.
Mr Bottazzo said that Studer’s customer care division performed very well, again posting record sales in 2024. The consistent expansion of international and multilingual service coverage with customer-facing and decentralised service specialists proved to be a complete success. The spare parts business, maintenance and machine overhauls and conversions achieved record sales, and the service business also remained at the previous year’s very high level of capacity utilisation.
Particularly strongAn important element of Studer’s success in 2024 was its broad portfolio. The CNC universal cylindrical grinding machine segment was particularly strong, with the S33 as the best-selling machine, followed by the S31, and the favoritCNC. Sales of the ultra-modern S41 in the premium segment were also solid. The second strongest segment was machines for internal cylindrical grinding with a robust sales performance. However, sales of production and conventional machines fell short of expectations.
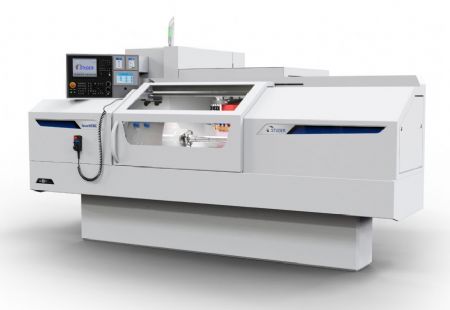
CTO Daniel Huber said that innovation and the development of modern and reliable grinding technologies for the benefit of customers remained the focus for Studer last year. One of the main development projects was the new generation of the popular favoritCNC universal cylindrical grinding machine (pictured left). Among other things, it now features the latest Fanuc controls and a ‘Conventional Mode’. This mode gives customers the option of working as they would on a conventional grinding machine, making the transition to CNC particularly easy. The many other new features include the option of automation and more powerful grinding spindles.
Another development focus is the new universal W-axis, which will be available for the S33 and S31. This is integrated onto the Z-slide and enables different workpiece lengths to be ground automatically and without operator intervention. The two main components — the tailstock with fixed centre and the tailstock spindle with driven centre as well as other assemblies such as measuring heads — offer innovative grinding technology advantages. As an absolute innovation, the direct force measurement allows a real force-controlled clamping process and thus maximum precision, repeatability and enables small clamping forces for fragile parts.
Mr Huber was delighted with the industry-wide success of the SmartJet coolant concept developed by Studer. Last year, the field of application of this particularly efficient and sustainable system was further expanded, including optimisations for thread grinding and plug-in coolant nozzles for different grinding wheel profiles. There are also new developments for the innovative WireDress dressing process developed by Studer for metal-bonded CBN and diamond grinding wheels. Mr Huber continued: “We have further developed WireDress for dressing internal grinding wheels.” This means that the innovative non-contact dressing system can now be used for external and internal grinding wheels in the same setup.
In addition, the CTO emphasised that the conversion of all relevant CNC platforms to C.O.R.E. has now been completed. The United Grinding Group’s modern and uniform hardware and software architecture is revolutionising the operation and capabilities of grinding and machine tools. Based on C.O.R.E., the Group will continue to develop ‘state of the art’ software and features for the benefit of customers in the future.
Successfully implementedStephan Stoll, COO of Studer, then gave an overview of the operations division. Despite the generally tense market situation, the manufacturing and assembly resources were largely utilised with the Studer machine business, the extensive inter-company activities within the United Grinding Group, and the development of future-oriented prototype systems.
Several relevant optimisation projects were successfully implemented, such as the strategically important expansion of internal spindle expertise. In addition to the commissioning of an automated, highly efficient spindle shaft production facility, all assembly processes were consolidated and enriched with ‘state of the art’ inspection and testing equipment. Highly specialised engineers and powerful assembly, data analysis, and diagnostic tools, allow the group-wide competence centre, to produce and further develop Studer spindles to the highest standards.
Meanwhile, the internal electrical pre-assembly has also been completely renewed. Mr Stoll said: “We are now able to produce everything from individual cable sets to fully wired, complex electrical control cabinets in a highly efficient, order-specific, and just-in-time manner.”
In addition, intensive planning for the comprehensive redesign and automation of the internal logistics infrastructure was completed last year. The implementation of this major Studer project is already in full swing — commissioning is scheduled for December 2025.
Studer was also committed to increasing sustainability and efficiency in its own operations in 2024. The switch to LED lighting was largely implemented and various systems for operational supply were replaced with the latest-generation of energy-efficient devices. The new logistics facility will also make a significant contribution to reducing energy consumption at Studer.
Mr Stoll emphasised that in addition, a wide range of digitalisation projects are being driven forward to tap into further efficiency potential in all areas of operations.
Mr Bleher concluded by emphasising the great importance of excellently trained and motivated employees for Studer’s long-term success as a technology company. He said: “We are fully committed to vocational training — more than 11% of our workforce are apprentices.”