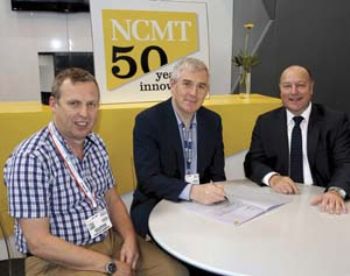
#MACH2014 A highlight on the stand of NCMT Ltd, Thames Ditton (
www.ncmt.co.uk), was the receipt of an order from Magellan Aerospace UK for a Makino MAG3 five-axis horizontal-spindle machining centre; the machine, which is being purchased with support from Invest Northern Ireland, will join six similar machining centres — and two smaller MAG1s — at the sub-contractor’s recently acquired factory in Greyabbey, near Belfast. The machine has a 3m X axis, a 120kW spindle and ‘intelligent’ workpiece weight sensing, which allows the axes to move faster when lighter components are being machined.
Haydn Martin, business development director at Magellan Aerospace UK, said: “We needed extra capacity in our Northern Ireland facility for the production of complex monolithic aircraft parts from aluminium billets, in particular in response to the ramp-up by Airbus of A350 production.
Making its UK debut on the NCMT stand was the Okuma MU-6300V-L — a five-axis vertical-spindle mill-turn centre with a working volume of 925 x 1,050 x 600mm and a capacity for workpieces up to 830mm in diameter, 550mm high and weighing 600kg. It is suitable for multi-sided machining of complex parts ‘in one hit’, especially in the energy and aerospace industries. Rapid traverse of 50m/min in the orthogonal axes minimises non-cutting times, while a double-column structure supports a +90/-120deg trunnion table that features twin roller gear cam drives on the trunnion (A axis) and a direct-drive motor for the 630mm-diameter rotary table (C axis).
Furthermore, the centre of gravity of the trunnion table (and hence of the workpiece) is low, enabling both heavy-duty cutting and high-speed finishing. The L variant of the machine demonstrated at MACH includes the ability to turn components on the table at up to 700rev/min using a static tool in the spindle. Either a BT40 (HSK-A63) or a BT50 (HSK-A100) taper can be specified, the respective maximum speeds of the 11 kW spindle motor being 10,000 and 6,000rev/min. More-powerful and faster spindle options are available, while the tool magazine capacity is 32 pockets (48 is an option). The OSP-P300M control, which provides fully interpolative five-axis machining, features built-in collision avoidance, as well as geometric error measurement and correction with the new Five-Axis Auto Tuning System: when the operator instigates the auto tuning cycle, the machine automatically measures geometric error using a touch probe and datum sphere and performs compensation, using the measurement results to tune the movement accuracy.
Taking centre stage on the NCMT stand was the 18.5-tonne Multus U4000-1SW mill-turn centre with B-axis turret, 22 kW counter-spindle and a capacity for components up to 2m long. Its 22kW main spindle has a 91mm bore (optionally 112mm) and generates 700Nm of torque at up to 4,200rev/min (alternatively, a 32kW drive can be specified, providing a torque of 955Nm). The machine is fitted with Okuma’s own linear scales, while servo motors deliver feed rates up to 50m/min in the X and Z axes, and 40m/min
in the 300mm Y axis.
The swivelling B-axis (-30 to +210deg) tool spindle with HSK-A63 taper (optionally Capto C6) is rated at 22 kW and 12,000rev/min; it develops a torque of 120Nm. The tool magazine has 40 stations as standard but is optionally available with a capacity of 80 tools. Together with a C axis on the main spindle, the machine is capable of fully interpolative five-axis machining. The machine specification can be extended further to include a lower turret with 12 live tool stations and a 7.1kW 6,000rev/min drive; the 22 kW counter-spindle can be replaced by a tailstock. Control is via the manufacturer’s OSP-P300 system, which uses an industrially hardened PC to run both the Okuma operating system and Windows XP.