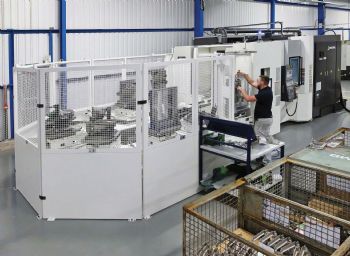
Sub-contract machinist BCW Engineering has installed a Japanese-built Okuma MB5000H horizontal-spindle machining centre (HMC) with a 10-pallet pool, thereby adding to its capacity for producing high-precision components for the aerospace, automotive and off-road vehicle sectors. The machining cell was installed by UK agent NCMT Ltd, Thames
Ditton (
www.ncmt.co.uk), to BCW’s new 30,000ft2 unit in Burnley, which was opened in October 2014.
Group engineering director Tony Kilfoyle said: “One aluminium aerospace part that we machined on another make of twin-pallet HMC took 23min to complete, whereas the Okuma finished it in just 11min.
This is partly due to being able to present a component on its pallet to the spindle more quickly, as it comes out of the pallet pool already fixtured, so set-up does not delay the start of the next cycle. Change-over is therefore limited to the automatic pallet change time, which is no more than 35sec.
“Once the part is being machined, the cycle is quicker because idle times are short due to the 60m/min rapids in the linear axes and the 2.5sec tool change. Additionally, the in-cut elements of the cycle are shorter, as the 40-taper 26kW 15,000rev/min spindle means that metal removal is fast.”
The performance of the new four-axis MB5000H, which has 500 x 500mm pallets and a machining volume of 760mm cube, has been so impressive that the sub-contractor has standardised on Okuma for all future HMC purchases. Mr Kilfoyle points out that most of the group’s 70 machine tools are hard-working production centres that run 24hr a day, which is why the company looks for robustness of build, not only of the structure but also of the spindle, tool changer, rotary axis and coolant delivery system.
BCW is building another new factory adjacent to its current Burnley premises; this is due for completion next month and will be dedicated to aerospace machining. Its centrepiece will be the group’s biggest machine to date, a 70-tonne Makino MCD2016 twin-pallet five-axis HMC with a 2,000 x 1,600 x 1,500mm working envelope.
It was bought at auction and coincidentally, the Japanese manufacturer also employs NCMT as its sole UK agent, which will be responsible for providing spares and service to BCW.