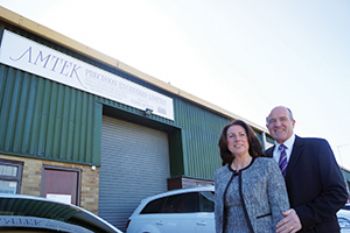
After 30 years, Amtek Precision Engineers (
www.amtek-precision.co.uk) finds itself in a strong position, with orders and enquiries for high-precision multi-cavity caps and closures injection mould tools and complex CNC components that the company specialises in at an all-time high.
Moreover, investment in staff and manufacturing technology is on-going. Occupying 21,000sq ft premises in Totnes, Amtek has come a long way since it was founded in 1984.
Back then, the fledgling company was struggling to find suitable facilities for its machine tools, as managing director Mike Jones recalls.
“I had been searching for suitable premises for a while, when my wife Helen — now the company’s financial director — found what we needed in the fishing village of Stoke Gabriel. We managed to secure a 1,000sq ft unit for £21 a week. We later moved to Totnes, when the owner of the units in Stoke Gabriel put forward plans to develop the land for housing.”
Mr Jones says that establishing the company’s reputation was down to a number of factors. First was the choice of materials, for which he used his aerospace experience gained in the Middle East.
“I looked at the other mould-making companies; and while their moulds were good, I thought we could do better. We invested in the highest-grade steels and the best-standard components, which resulted in zero repairs coming back from the customers. From there, we really took off.”
Next was his staff — such as Danny Grant, who joined in 1997 and is now senior development manager. He says: “Just because you can make something a certain way it doesn’t mean you should. There are many considerations that should be looked at before a choice is made.
The initial cost of producing a mould tool is relatively high, and its size has a direct impact on the price of both the injection moulding equipment and the tool, so the customer will expect us to keep everything as small as possible.
“We have to work outwards from the cavities, ensuring that there is enough material between the high-pressure injected plastic material and the heating and cooling channels to prevent ruptures. We provide a million-shot warranty on our tools.”
Mr Jones is also fully aware that ‘new blood’ is required to support his plans for the business. “We see apprenticeships as an important step towards addressing the skills gap in engineering. We already have a number of
apprentices here and are looking to start three more. The Government has been very pro-active in its support, and it is good to see that we are starting to get intelligent youngsters back into engineering.”
The final part of the equation is the machine tools that Amtek invest in. Typically, the company will purchase Japanese or Swiss technology with an emphasis on automation for unmanned overnight operation — such as the 20-pallet Mikron HSM 400 — to support the 22 staff working during the day.
Mr Jones says: “We purchased the first HSM 400 produced; I believe that machine can do the work of 20 good men with 20 milling machines. The quality and accuracy are phenomenal, so we followed that with a Mikron Graphite Master, which has a 65,000rev/min spindle and has allowed us to switch from copper to predominantly graphite EDM electrodes for our die-sink machines. This machine also allows us to create highly detailed mould cavities and mirror-like finishes.”
Although most of the programming for the die-sink machines is done at the controller, the complexity of the NC code required for the Mikron machines, the Mazak Integrex mill-turn centre and the wire EDMs means that it is more efficient to create programs in the company’s CAD/CAM office, which is equipped with AutoCAD, SolidWorks and
Delcam’s FeatureCAM.
In conclusion, Mr Jones says: “Industry figures show that around 800 million caps and closures are made every year. While the sector that demands the majority of our capacity varies each year, we do know that the suites of tools we manufacture here in the UK are used by customers across the globe. At our level of quality, we don’t have much of a threat from China; the best of the Swiss and the German mould tool makers are our competition.”