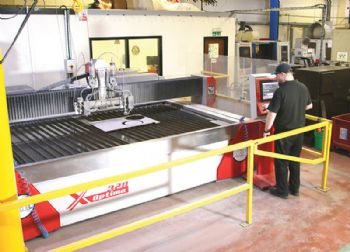
When Alun Hobbs identified a way to “revolutionise” the design of butterfly valves some 12 years ago, his employer was reluctant to pursue the opportunity on offer.
Believing in his design, Mr Hobbs set up Hobbs Valve in Caerphilly to meet the requirements of the offshore, power generation and general-industry sectors.
His patented triple-offset butterfly valves provide a more-efficient, safe and cost-effective solution that reduces down-time and maintenance times, while also eliminating leaks.
They incorporate patented seat and seal technology to enhance reliability, and they are the mainstay of the company’s success.
This has seen Mr Hobbs expand the original business, with Hobbs Valve now part of the Great British Valve Group, which also encompasses Hobbs Precision Engineering, Cambrian Valves Ltd and HVG Techno.
Founded as a sub-contract machining business to mainly produce components for Hobbs Valve, Hobbs Precision Engineering recently bought an Optima 320 twin-head water-jet machine from Rochdale-based Kerf Developments Ltd (
www.kerfdevelopments.com).
The founding of Hobbs Precision Engineering resulted from the need to reduce Hobbs Valves’ sub-contract machining costs by bringing the manufacture of valve components in-house.
There are three variants in the valve range: lugged valves; double block and bleed valves; and ‘cryo’ valves.

Currently, Hobbs Valve manufactures more than 3,000 triple-offset butterfly valves a year; and with more than 40 machined parts per valve and hundreds of variants, the machine shop has reduced average lead times from 12 weeks when the company was founded to just four weeks.
The Optima 320 twin-head water-jet machine from Kerf has further reduced these lead times since its recent introduction.
Moreover, the short turn-round times on high-value niche market valves has won the business high-profile customers — including the likes of Shell, BP, Ineos, BNFL Conoco Phillips, Exxon Mobil, Maersk, Amec and Total.
Why water-jet?
Explaining why Hobbs Precision Engineering opted for a water-jet machine, machine shop manager Craig Llywellyn said: “We identified that we could produce over 1,500 clamp-ring parts in-house every year — something that would reduce our reliance on sub-contractors, while at the same time cutting costs and improving both production scheduling and lead times.
“Moreover, water-jet was the only feasible option for our components, as cutting with laser or plasma would introduce heat to our components.
“With complete certification, traceability and standardised conformity of all valve parts — from the steel mill through manufacturing to delivery — heat would impact the properties and conformity of our parts.”
The clamp rings are manufactured from aluminium bronze and a variety of stainless steels that range from 316 to super duplex; their sizes vary from 50 to 1,200mm for diameter and 4 to 12mm for thickness.
Mr Llywellyn added: “By bringing the production of clamp ring parts in-house, we have reduced our sub-contracting costs by over £30,000 per year.
“Furthermore, we have gained greater control over our processes and quality, while reducing our lead time for these parts from four weeks to just one day.

“Triple-offset butterfly valves are bespoke products that are not volume-manufactured, so the ability to produce clamp rings when required in volumes of one to 10-off gives us the flexibility and reaction time we need.”
Hobbs Precision Engineering is now also using the Kerf Optima 320 to produce end plates for its butterfly valves.
Made from the same materials as the clamp rings, the in-house production of these plates, which range in diameter from 25 to 100mm, has cut sub-contracting costs by a further £20,000 per annum.
Mr Llywellyn said: “While the Optima 320 water-jet machine has reduced our sub-contracting costs by over £50,000 a year on just two component types — and is alleviating supply chain issues — the machine still has a long way to go before reaching full capacity.
“We are now looking at other Hobbs Valve components that can be cut using water-jet, to achieve further savings; we are also selling our water-jet capacity to create additional profits for the business.
“The Optima 320 is an extremely flexible machine that has a cutting envelope of
3 x 2m and can cut materials up to 125mm thick.
“Furthermore, it is not limited to the steel and aluminium bronze that we’ve been cutting.
“Indeed, it can cut just about any material within its dimensional capacity; we have even used the machine to produce 40mm-thick foam in-lay cards for insertion in toolboxes — to protect the tools.”