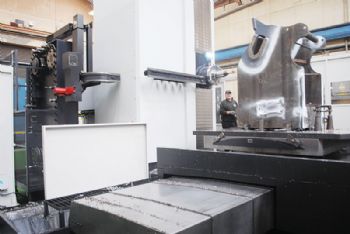
When Coalville-based
Terex Pegson — part of the Terex Corporation, and a leading manufacturer of mobile crushers — found out that Doosan made a horizontal boring machine that exactly met its requirements, the decision to buy one was immediately taken.
As a result, Mills CNC — the exclusive distributor of Doosan machine tools in the UK and Ireland — installed a Doosan DBC160 between July and October last year.
The massive borer is now being used to machine high-accuracy bores, holes and threads — as well as other features — in the fabrications that form Terex’s mobile crushers.
These fabrications are made from steel plate sections that are first plasma-cut and then welded together before being loaded onto the DBC160 for machining; and while the weight of these fabrications varies according to the type and size of crusher being produced, they typically weigh from six to 30 tonnes.
Machining operations on the DBC160 can be relatively long, and the need to maintain high levels of productivity means that ‘aggressive’ rates of metal removal are required.
Up to 70 mobile crushers are made at the Coalville facility every month, and the last 12 years have seen something of a renaissance there.
The company has increased its head-count, which currently stands at 100, and demand from around the world for its range of machines — impact crushers, jaw crushers and cone crushers — is at an all-time high.
‘Lean journey’
Jason Toon, operations and facilities manager, said the change in fortunes has not happened by chance: “We have been on a ‘lean journey’ for the last 12 years, and because continuous improvement is not a finite destination, we are still on it.
“We have rigorously applied lean-manufacturing principles and methods across our operations, and we are committed to driving out waste and inefficiency.”
He went on to say it is estimated by ‘lean-manufacturing aficionados’ that 60% of production activities in a typical manufacturing operation are wasteful and do not add value for the customer.
“For us, the introduction of lean manufacturing has helped to galvanise and motivate the workforce.
“It has had a dramatic and significant impact on quality and productivity levels — and, not surprisingly, on the company’s sales growth and profitability.”

While the increase in demand experienced by Terex for its mobile crushers was clearly ‘good news’ for the company, it did highlight a capacity problem that would only get more acute if not addressed.
“We undertook close examination of our machining capacity and capabilities, including an analysis of our weaknesses and where bottlenecks were occurring — or could occur in the future.
“It became clear that a new large-capacity horizontal boring machine was needed to satisfy our immediate and future machining requirements.”
Terex had previously bought a horizontal boring machine; and while it seemed likely that the order for the new machine order would be placed with the same supplier, it did not turn out that way.
The company is ‘no stranger’ to buying Doosan machine tools from Leamington Spa-based Mills CNC Ltd (
www.millscnc.co.uk); it has bought four new Doosan machining centres since 2012.
These include two large-capacity Mynx 7500/50 machines, as well as a Doosan Puma 400 (long-bed) lathe with driven tooling, and they are being used to machine crusher components in small batches.
‘Off the radar’
However, Mills CNC was not on ‘Terex’s radar’ for the new horizontal boring machine, as Mr Toon explains: “The machine tool specification we had drawn up included the requirement for a 3m Y axis.
“At the time, we didn’t realise that the new Doosan DBC160 borer could be supplied with such a large Y axis.
“However, when we found out — somewhat fortuitously, it must be said — that Mills could indeed supply us with such a machine, we were naturally interested.”
As part of the purchase process Mills invited representatives from Terex to visit the Doosan factory in South Korea to see DBC160 machines being built — and to see the results of a factory acceptance test.
Mr Toon said: “The DBC160 is a new machine, and we were going to be the first customer in the UK to buy one.
“This, plus the performance-critical nature of the investment, meant we had to get it right first time.”
The performance of the DBC160, its cost, availability and the fact that it was backed by Mills CNC’s ‘best-in-class’ after-sales services and technical support were all key factors in concluding the sale.

The specification of the machine was also of paramount importance.
The DBC160 is a large-capacity moving-column borer equipped with a 45kW 2,000rev/min high-torque 160mm-diameter spindle “that takes heavy-duty roughing operations in its stride”.
Moreover, the machine’s design and structural rigidity help to minimise vibration and maintain high levels of part accuracy and surface finish.
The DBC160 has a work envelope of 4,000 x 3,000 x 1,600mm and can accommodate workpieces up to 3,400mm in diameter (and weighing 20 tonnes) on its B-axis rotary table.
Before the DBC 160 machine was delivered to Terex, a significant amount of pre-installation work was undertaken at the Coalville facility by Mills CNC’s projects team.
This included digging out the existing floor and foundations of the machine shop, laying new foundations and a new floor, and installing drainage systems and coolant channels, plus new guarding.
Moreover, the floor itself was lowered by 1m to allow the machine to operate at its full height (and therefore at full capacity) without colliding with the machine shop’s overhead crane.
Mr Toon concluded: “It was an involved and complex installation — certainly with regard to pre-installation — but the Mills CNC engineers did a great job.”