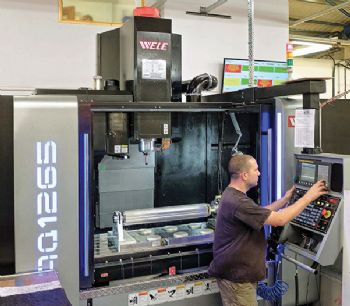
Crediton-based Adaero Precision Components has always carefully assessed its machining needs when buying new equipment, and optimising price and performance is something the company has done well over the years; its latest
purchase — a WELE AQ1265 three-axis vertical machining centre with Nikken rotary-table fourth axis — is no exception.
The provider of this Taiwanese-built machine — the Kenilworth-based sole agent Whitehouse Machine Tools Ltd (
www.wmtcnc.com) — has delivered numerous other machining centres to the sub-contractor during the last decade, sourced from Brother (Japan) and Akari (Taiwan), so Adaero had confidence in the supplier’s advice this time around, despite not being familiar with the WELE brand.
The requirement on this occasion was to replace an ageing four-axis machining centre that had become unreliable. The new machine is mainly devoted to carrying out cycles of relatively low complexity on simple parts, such as large aluminium plates.
A moderate level of investment was appropriate in a machine fulfilling this type of work.
Nevertheless, dimensional accuracies of typically ±0.01mm need to be held; and while three-quarters of the factory’s output is based on aluminium parts, the machine needed to be robust to perform arduous cutting cycles continuously — every day — from 8am to 5pm.
David Smith, Adaero’s finance manager, said: “The WELE met our requirements and cost significantly less than other machines we reviewed.
“Our engineering director, Jack Wilson-Hill, had visited a Whitehouse customer to see a similar machine in action and was impressed with its rigidity and build; and the fact that WELE is part-owned by Toyoda — a Japanese manufacturer of top-end machine tools — pointed to production equipment that was of high quality, added to which the AQ1265 was competitively priced, so we placed the order.”
Extended capability
The rationale for opting for a fourth axis was to extend the machine’s capability, enabling it to produce more-complex components in the future, if required.
The rotary table is also needed in the short term to drill and pocket-mill lengths of aluminium extrusion on four sides in one hit. Single set-up machining is a goal throughout Adaero’s factory.
The AQ1265, which is equipped with linear roller guideways and features a hand-scraped finish on every major contact surface, has a work envelope of 1,200 x 650 x 610mm, a one-tonne maximum table load, a ‘two-speed direct-drive BT40 spindle’ to optimise roughing as well as finishing at speeds up to 15,000rev/min, a 40-station tool magazine, a cutting feed rate up to 15m/min, and 36m/min rapids in X and Y (30m/min in Z).
The ‘judicious use of automation’ in the Crediton factory — including robotic load/unload — is another indicator of Adaero’s adeptness in matching investment to need.
As far back as 2011, the company purchased (from Whitehouse) a Brother 30-taper four-axis machining centre with twin-pallet changer (the 3.4sec pallet change takes place simultaneously with tool change and axis positioning, minimising idle times).
Automation was advanced further in 2014 by the arrival of a Brother multi-level automated storage and retrieval system for 84 machine pallets.
It proved ideal for Adaero’s high-precision high-mix production of hundreds of different prismatic parts in batches ranging from 300-off to just six.
More recently (in 2018), an Akari machine was installed. Capable of long periods of uninterrupted unattended running, it joined an almost identical cell — installed two years previously — that has proved highly productive for machining components that can be accommodated in its work envelope of 640 x 610 x 680mm.
Both cells are run by a single operator in a second factory unit; opened in 2016 on the same industrial estate in Crediton, this doubled Adaero’s factory space to 15,000ft
2.