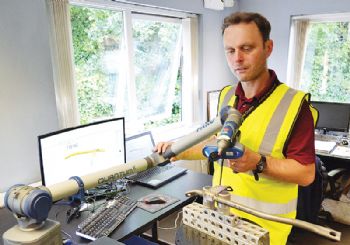
Located in West Bromwich, 130-employee Metal Assemblies Ltd produces high-quality stampings and assemblies for customers that are mainly involved in the global automotive industry.
About 25% of the company’s production is exported; and while most of these sales are made in Europe, it also has customers in Asia, as well as South and Central America.
Continuous investment in the latest ‘production aids’ means that Metal Assemblies’ 75,000ft
2 factory can undertake a wide range of procedures; these include pressworking, machining, tube manipulation, robot welding and tool making.
The high-yield capability of its modern plant allows the business to continue to thrive in what is an extremely competitive environment.
Metal Assemblies’ comprehensive production facilities and the autonomous nature of these mean that it can undertake the vast majority of its customers’ requirements in-house, with only a small amount of specialist work sub-contracted to a few trusted suppliers.
However, when the volume of out-sourced work reaches significant levels, Metal Assemblies pursues (where possible) a policy of sourcing the required equipment and bringing the work in-house.
A case in point was the recent purchase of a 2.5m-capacity eight-axis QuantumE ScanArm with a Laser Line Probe SD from Rugby-based Faro Technologies UK Ltd (
www.faro.com).
Simon Bullows, Metal Assemblies’ quality manager, said: “Although we have a high-specification co-ordinate measuring machine, it cannot make the surface scans that we need when performing work such as product development, so we were out-sourcing this work; but the volume of sub-contracted 3-D scanning recently reached a level where it became feasible to purchase our own scanning device.
“Having considered equipment from several metrology companies — and following an excellent demonstration — we concluded that the Faro eight-axis QuantumE ScanArm fitted with the company’s FaroBlu Laser Line Probe best met our needs.”
‘Seamless integration’
This recently launched Faro product seamlessly integrates a QuantumE FaroArm with an eighth axis, making it ‘the world’s first eight-axis portable co-ordinate measuring machine’.
Faro says the QuantumE is “the ideal portable solution for companies that are looking for a cost-effective, user-friendly and efficient factory inspection system.
“The accurate yet robust FaroArm has been tested to withstand the harshest shopfloor environments, while delivering market-leading portability and ergonomics.”
The first portable CMM arm in the market to be internationally certified to ISO 10360-12 standards, it ensures maximum measurement consistency and reliability.
The Faro scanning system can also operate in a wide range of conditions, including extremes of temperature and shopfloor environments.
Furthermore, the integrated eight-axis rotary scanning platform can cut scan times by up to 40%, as there is no need to move around an object to scan it; instead, users simply rotate the platform as they probe or scan the part under inspection.
Mr Bullows concluded: “After our Faro training sessions, we quickly became competent in use of the QuantumE.
“In addition to performing all of the 3-D scanning tasks that we previously out-sourced, the ScanArm is now being used for a range of tasks — including first-article inspection (FAI).
“Given the speed and accuracy of our new Faro device, once parts pass FAI our production processes can proceed with confidence.
“Also, when a production run is underway, the QuantumE is ideal for quickly identifying component features that begin to deviate from nominal conditions, allowing prompt machine adjustments to be made before out-of-tolerance situations occur.
“Although purchased mainly for use in our QC department, because the QuantumE is portable, quick and easy to set up, we can also perform in-process component inspection on the shopfloor.
“While not currently used for this application, we anticipate using our ScanArm in the future to capture precise digital measurement data for the reverse engineering of parts for which there are not relevant blueprints or CAD drawings.”