
One of the UK’s largest pump manufacturers, Charles Austen Pumps ships more than 200,000 units per year and recently invested in its first sliding-headstock bar auto — a Citizen Cincom L20-X.
This was installed in the company’s Byfleet factory in June 2019 and has taken over the turn-milling of parts up to 25mm in diameter, most of which are brass.
A few aluminium, stainless-steel and plastic components are also produced.
Charles Austen Pumps was established nearly 75 years ago (by Charles Austen) and is credited with inventing the diaphragm pump, which helped John Enders to develop the polio vaccine in the 1950s.
The company’s products later assisted the development of Concorde and helped the Apollo 15 mission to put a ‘rover’ on the moon.
A wide range of pump types is now manufactured; moreover, the firm has been so successful that growth over the last six years has been 30% per annum, driven by strong home sales and a buoyant export market.
This level of success has put a strain on all areas of the operation, not least the machine shop; and while prismatic metal-cutting (this includes the milling and drilling of parts for pumps) and the manufacture of injection mould tools is largely carried out in-house, the two fixed-head 57mm-bar-capacity CNC lathes on site struggled to cope with the production volumes of rotational parts.
The result was that, until recently, as much as two-thirds of the turning requirement was sub-contracted out — at a cost of more than £100,000 a year.
Matt Wright, machine shop manager at the Byfleet facility, said: “More than 80% of our turned components are between 16 and 19mm in diameter, so we needed a lathe with a relatively small bar capacity to start bringing work back to our factory.
“Our bigger lathes are not so efficient when machining these smaller workpieces, due to their longer tool movements and slower axis travels.
“We considered fixed-head as well as sliding-head technology, as our parts are generally short compared to their diameter, but we concluded that sliding-head turn-milling would be more productive, because the tools are mounted on gang posts rather than turrets.
“As a result, they are quicker into the cuts, because they have less distance to move; also, we do not need to use the guide bush, so the bar remnants are shorter, saving money on material.
“However, should we ever need it, we also have the flexibility of quickly installing the guide bush for ‘true Swiss-type turning’ of shaft-type workpieces with lengths over 2.5-times diameter.”
Sound reputation
Mr Wright said that, while the company initially reviewed most of the sliding-head lathe providers, the choice of machines from Citizen Machinery UK Ltd (
www.citizenmachinery.co.uk) was primarily down to the latter’s reputation for high-quality machines and for providing good levels of applications support, training and after-sales service.
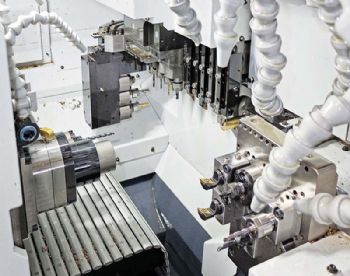
A selection of turn-milled components for the OEM’s pumps was taken to Citizen Machinery UK’s Bushey technical centre, where its engineers recommended the twin-spindle L20-X turning centre (in optional oversize configuration and capable of machining bar up to 25mm in diameter) as the best machine for producing the parts — along with an Iemca bar feeder (for 3m-long stock) and a workpiece conveyor.
The machine accommodates up to 44 cutters as standard, including rotary stations on the gang tool-post, opposing tool-post and back tool-posts — plus Y-axis movement for the first two tool carriers.
The LFV (low-frequency vibration) version of the machine with its patented two-axis CNC chip-breaking software in the control’s operating system was not specified, as the pump manufacturer mainly machines free-cutting brass.
Batch sizes produced on the Cincom vary greatly, from ones and twos for the R&D department up to 10,000-off.
The first job on the machine was a brass cam that ran continuously for 96hr (from Monday morning to Thursday evening).
Machined to tolerances of +10/-5µm in a 105sec single cycle (including in-cycle engraving for traceability), the part previously needed two operations taking three-times longer, plus additional handling for manual chamfering and stamping.
Mr Wright said that with the L20-X, machine attendance was minimal during the day and non-existent overnight. Moreover, when he arrived at the factory the next morning and measured the parts, all were not only within the 15µm tolerance band but right in the middle of it.
Another brass component, this time a 19mm-diameter disc-type part just 0.6mm thick, saw its two previous operations and 2.5min cycle reduced to a single 50sec cycle — plus the elimination of inter-operation handling.
A third example — a double eccentric with an offset hole and an offset spigot with a 5µm tolerance limit — is now produced in under 3min instead of 5min, including engraving that previously had to be done manually.
Moreover, Mr Wright says the surface finish on all parts coming off the L20-X is noticeably better.
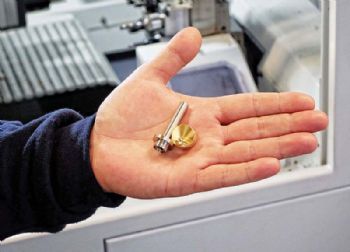
Before the machine was delivered, Citizen Machinery provided programs for machining two components.
Since then, the Cincom machine operators (including Mr Wright’s son Ryan) have been using Citizen’s Alkart CNC Wizard programming software.
They say this software is easy to learn, adding that it is a simple process to cut, modify and paste elements from an original program and add new ‘blocks’ for other features, using the Wizard’s G-code and M-code library (built into the software).
Mr Wright concluded: “We are already bringing turned-parts manufacture back in-house, and that will accelerate in the coming months.
“We have hundreds of component variations lined up to put on the L20-X; by Easter this year, we should be turn-milling them all in our factory.
“With the amount we have been spending lately on sub-contracting services, I calculate that the Citizen Cincom slider will pay for itself in a little less than two years.”