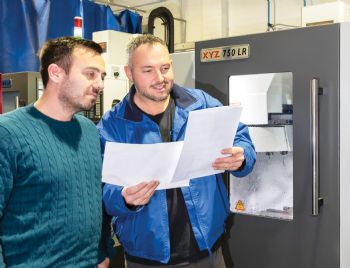
Carney (UK) Ltd started in 2014 as a business development consultancy offering the project management expertise of founder Simon Carney to small and medium-size engineering companies.
While working on a business turn-round project for a fabrication company, Carney (UK) was invited to project-manage the design and development of powertrain assembly fixtures for a luxury vehicle manufacturer.
This opportunity initiated the transformation of Carney (UK) into a designer, developer and manufacturer of bespoke equipment for the automotive sector, including assembly jigs and fixtures, production line equipment (such as end-effectors for robots), pneumatic handling systems and special-purpose machinery for assisted assembly.
Mr Carney said: “Through hard work and dedication to delivering projects on time and to budget, we overcame the challenges faced by small businesses trying to ‘break into’ large OEM automotive manufacturers.
“We are extremely proud of what we have achieved.”
With UK customers ranging from prestige low-volume manufacturers through to high-volume vehicle producers, Carney (UK) develops solutions to meet their assembly and automation needs.
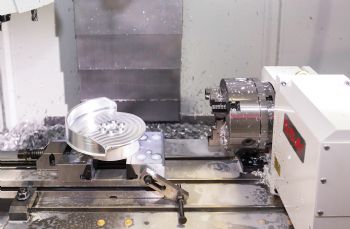
Moreover, demand looks set to grow, thanks to significant interest generated by products such as multi-purpose jigs that can be used on more than one model of vehicle — plus the rise in start-ups in the electric-vehicle sector and interest from as far afield as China, with its burgeoning automotive industry.
Initially, the machining required by Carney (UK) was undertaken by sub-contract machine shops near the company’s Runcorn base, but as demand grew and time pressures from customers increased, these sub-contractors began to struggle to deliver what was now many batches of low-volume parts.
When the company relocated to its current premises, Mr Carney decided to start bringing machining in-house.
Initially, this involved “using a few old manual machines” as a stop gap, but he knew that investment in new machining technology was necessary and sought the advice of his technical manager Edward Hibbert, who recommended XYZ
Machine Tools.
Sound recommendation
Mr Carney said: “While working with sub-contractors, I had seen XYZ machines almost everywhere I went; it was this fact, along with the trust Mr Hibbert put in them, that convinced me XYZ was the way to go.
Our first purchase was a 500LR vertical machining centre, which was quickly followed by a CT65 turning centre. We then added another VMC — a 750LR with fourth-axis capability — followed by an XYZ 1330 manual centre lathe to cover the requirement for smaller turning work.”
The two LR machining centres, which use the latest linear rail technology, were the ideal starting point for Carney (UK), with the Siemens 828D system not only providing straightforward conversational control but also allowing the business to develop its use of CAD/CAM systems to generate programs (avoiding the problem of trying to find skilled machine operators).
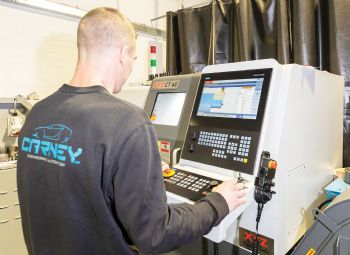
The machines also have the capacity to accommodate most of Carney (UK)’s components, with the 500 LR and 750 LR offering work envelopes of 510 x 400 x 450mm and 750 x 440 x 500mm respectively; both machines also feature the same 8,000rev/min 13kW BT40 spindle and 20m/min feed rates in all axes.
Meanwhile, the CT65 has a 17kW spindle, a 65mm bar capacity, and a maximum turning diameter and length of 200mm and 260mm; it uses the ShopTurn version of the Siemens 828D control.
In conclusion, Mr Carney said: “The XYZ vertical machining centres and the addition of the fourth axis on the 750 LR machine, along with the CT65, give us the versatility and competitive edge that we need; but most importantly, we now have total control over our machining requirements.
“While we initially programmed at the machines, the move to using OneCNC CAD/CAM software was a further step in developing and streamlining our machining capability.
“Indeed, we are now confident that we can machine anything that falls within the capacity of the XYZ machines; and as we move forward as a business, we are also confident that XYZ will continue to provide the support we need to meet our future machining challenges.”