
Bridlington-based BW Industries, a steel-processing specialist, has invested in two LVD 4.5m 320-tonne Easy-Form press brakes from Banbury-based LVD UK Ltd (
www.lvdgroup.com); these can work together (as a tandem machine) to form components up to 9m long and 8mm thick. The company has also installed a fast electric-drive LVD Dyna-Press to boost productivity on smaller components.
BW Industries was established 45 years ago; and following a management buy-out in 2016 it is currently run by Gareth Rounding (managing director), Neil Pilling (director of operations), Dan Smith (finance director), and Steve Smith (general manager).
The company has around 150 employees, and its turnover has increased by £7 million in the last three years (to more than £25 million).
It is unusual in having both press brakes and roll-forming lines, as well as lasers and fabrication facilities.
Mr Pilling said: “We produce anything to do with steel products — pressed, rolled, laser-cut, assembled and painted. We are, in essence, a ‘one-stop steel shop’, processing around 25,000 tonnes of steel a year.”
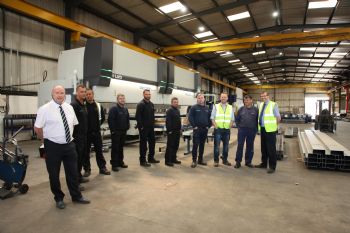
Many of BW’s customers are in the construction sector, where the off-site manufacture of modular buildings is a strong and growing area.
With its laser and press braking capabilities, the company also supplies customers producing commercial vehicles, motorway signage, crane booms and shipping containers.
It recently upgraded its EC certification of conformity and can now supply fabricated structural steel purlins, mezzanine steel channels, engineered wall panels and fabricated structural steel assemblies up to Execution Class 3 (in accordance with BS EN 1090).
Pre-fabricated modulesMr Rounding said that the move to off-site construction is significant, as the use of pre-fabricated modules produced in factory conditions gives major time and cost savings on-site and ensures high levels of accuracy and quality.
BW can offer customers: a kit of parts (including beams and cleats); fabricated floor and ceiling cassettes that can be bolted or welded together on-site; or complete fabricated cubes that could be used for anything from a drive-through coffee shop to a school classroom, a multi-storey office building or a hotel.
When you look at a building that was constructed off-site you would not know that it had been. The only thing you might notice is that the bricks are too straight!”
While the decision to invest in new bending capacity started with the need to replace some older machines that were becoming difficult to support with spares and service, it also gave BW the opportunity to bring its bending
facilities up to date.
Mr Pilling said: “We set out to purchase new machines that featured the latest technology and would be supported with spare parts, maintenance and service.
“We wanted to give our operators the best equipment and tools for the job. Previously, we only had a 7.3m press brake, whereas our laser capacity was 9m, so we decided on two 4.5m machines that could run in tandem and complement the laser.”
The design of its press brake frames means that LVD can build machines up to (and beyond) the size of the two at BW without the need to ‘dig a pit for the foundations’.
The key benefits of these machines for BW are their accuracy, the speed of set-up and the flexibility of having either two 4.5m 320-tonne machines or one 9m 640-tonne machine.
This gives the company effectively three machines in one, with a minimal change-over time when moving to tandem operation.
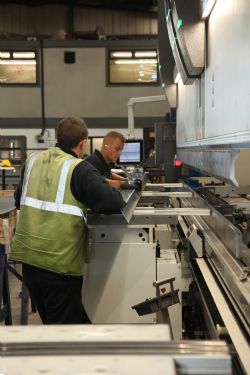
Mr Pilling said that the first test part produced was accurate to 0.3mm over 9m, and that the machines give a consistently accurate bend on every component.
“This is due to the Easy-Form angle-monitoring systems, automatic crowning and precise control of the Y1 and Y2 axes on each of the two machines when working together.
“The parts we produce generally have fairly simple geometries, so they are very straightforward to program at the machine, thanks to a very user-friendly interface.
“This, along with the hydraulic tool-clamping system, allows for very quick set ups.
“For the new machines, we purchased 200mm-long top and bottom tooling.
“Changing tooling is now a one-man job; before, we were using 4m- and 6m-long tooling, which had to be craned into place by two people. Set-up times have now comes down dramatically.
“The tandem press is also fitted with four CNC sheet followers — two on each machine — that support the material during bending. When you are forming a 9m beam you need to support it for health-and-safety reasons alone.”
Speed and accuracyThe recently installed LVD Dyna-Press is a small, fast and accurate machine (with an electric drive system) that is suitable for bending small parts and is very easy to use.

Mr Pilling said: “We were producing large numbers of small parts on our larger press brakes. These parts were taking up capacity and wearing out the centre of the bed, so we looked for a machine that would be suitable for producing all the cleats and brackets.
“The Dyna-Press is very efficient and has certainly increased our production efficiency and capacity; and because it is so easy to use, we can run the machine during our night shift as well, if we need to.
“The investment in the LVD machines is certainly paying off in terms of new business.
“We recruited a dedicated salesperson to sell the capacity for the laser and press brakes, six months before the Easy-Forms were installed, so that we could ‘hit the ground running’.
“They have brought in a lot of work that we could not have undertaken before.”