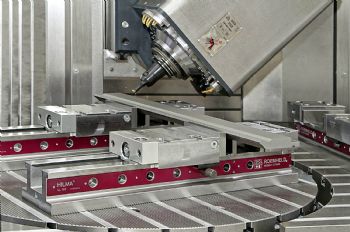
UKB Uwe Krumm GmbH, a German press brake tooling and guillotine shear blade manufacturer, makes products ranging from 60 to 6,000mm long and weighing from a few hundred grams to several tonnes.
Based in Burbach, the company has 14 machining centres on its shopfloor and uses only two types of vice — regardless of the size and geometry of the component and the material being processed.
These work-holding devices are supplied exclusively by the Hilma division of the Roemheld group, whose factory is in nearby Hilchenbach.
UKB is currently using around 90 vices from the firm’s NC160 and VL160 series.
These products are supplied to customers in the UK and Ireland by Roemheld UK Ltd, Hitchin (
www.roemheld.co.uk).
The standard base length of the vices is 750mm, providing a clamping range of 508mm (sufficient for most of UKB’s workpieces), while various top jaws enlarge the range to a maximum of 772mm.
Configurations vary from five vices on UKB’s smaller milling machines to 14 vices on a DMG Mori DMF 600 linear five-axis model with a 6m X axis.
Peter Diehl, head of production, said: “We use the vices for everything from simple three-axis operations to complex five-axis machining applications requiring multiple set-ups.
“They are highly precise, always dependable and easy to use.” In view of the requirement for high-precision machining — typically to within ±0.01 mm — Mr Diehl attaches special importance to process reliability.
“Clamping components with minimum deformation is of major importance to us.
“With Hilma machine vices, we can hold the workpiece at maximum pressure for roughing — to reduce a tough Hardox steel blank for a 5m tool weighing six tonnes to just 1.5 tonnes, for example — then lower the clamping force for finish-machining.”