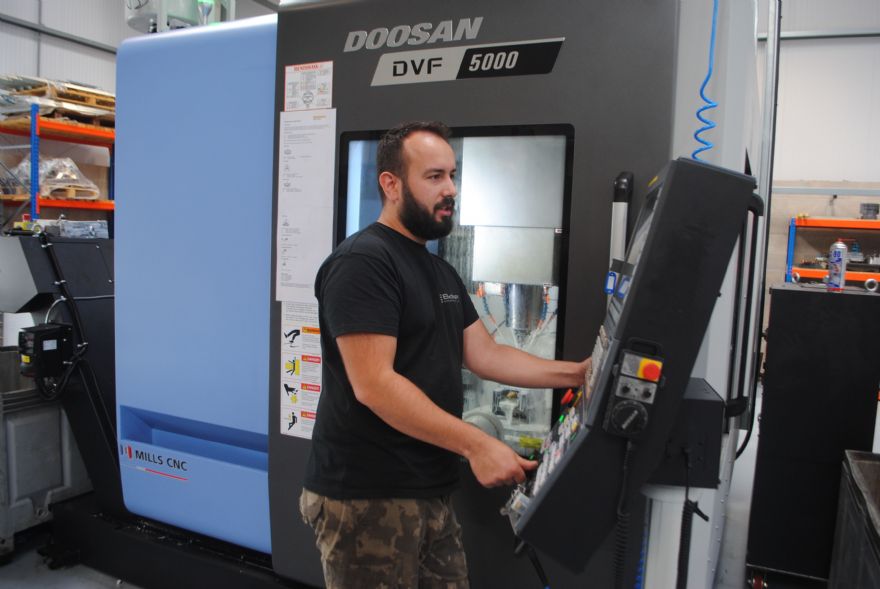
Significantly reduced machining operations leading to faster part cycle times, improved operational efficiencies and new business wins are just some of the benefits
Baker Engineering Ltd is experiencing from its latest Doosan five-axis machine tool investment.
Leamington Spa-based
Mills CNC, the exclusive distributor of Doosan machine tools in the UK and Ireland, has recently supplied the leading precision toolmaker and engineering sub-contract specialist, with a new, high-performance five-axis Doosan DVF 5000 machining centre.
It was installed in April 2020 at the company’s new, purpose-built 8,000ft
2 facility in Derby, where it is being used to machine a diverse range of high-precision components, as well as specialist tooling, jigs and fixtures for its growing UK and international customer base.
The DVF 5000 is the second Doosan machine tool Baker Engineering has invested in recent years, the first being a new DNM 6700 vertical machining centre which was acquired in February 2017.
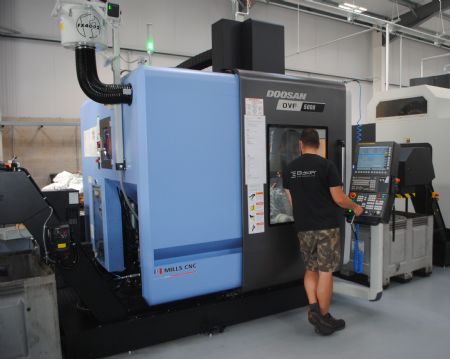
Baker Engineering is a family-owned business established in 2008 that today employs 15 people. It is ISO 9001:2015 accredited and is committed to continuous improvement making regular investment in the latest machine tool and ancillary manufacturing technologies to maintain its competitiveness and strengthen its preferred partner relationships with its customers.
The sub-contractor has a number of CNC machines at its disposal, including machining centres with integrated fourth-axis units, lathes with bar feeders and wire EDM machines.
In addition to offering precision sub-contract machining services, the company also has specific strengths in manufacturing aerospace component tooling, including jigs and fixtures for ground-support maintenance; tooling for the measurement and inspection of railway tracks; and tooling used in the power generation sector.
As a forward-thinking company the decision to invest in the latest five-axis machining technology was a natural one for Baker Engineering to make last year.
Director, Adrian Baker said: “Multi-axis and multi-tasking machine tools help manufacturers improve their productivity. Because we are a company that is looking to constantly improve, we had done our homework into the technology and could see that an investment in a five-axis machine tool would deliver significant performance benefits.
“In addition, the investment would send the right signals, externally and internally, that Baker Engineering was focused on the future.”
‘One hit’ machiningThe key advantages from investing in five-axis machine tool technology were immediately apparent to management and staff at the company and included: the ability to machine complex shapes/parts in a single set-up; the added benefit that ‘one-hit’ machining has on reducing the time and costs involved in fixturing; and the ability to improve/ maintain part accuracies owing to a reduction in work handling.
A demonstration of the machine’s capabilities and effect it has had on Baker Engineering is illustrated by the following example.
A customer electrical housing-type component was machined, prior to the arrival of the DVF 5000, in five separate machining operations with a cycle time of 2.5hr. When machined on the DVF 5000 the number of operations was reduced to two, and the cycle time was 0.75hr.
Prior to making the investment decision, Baker Engineering did its homework and investigated the market in order to help identify the type of machine that would ‘fit the bill’.
Mr Baker explained: “We had invested in a DNM 6700 vertical machining centre from Mills CNC in 2017. We have been pleased with the machine’s performance and reliability, and have been impressed with Mills’ after-sales service and support.
“When considering the five-axis machine tool investment is was natural that we approached them to discuss our requirements.”
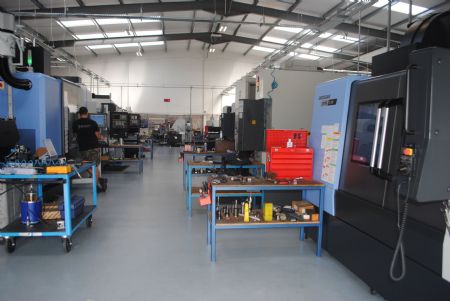
The Doosan DVF 5000, is a popular and best-selling five-axis machine supplied by Mills CNC. It is a compact and rigidly-built machine that delivers excellent cutting performance and unrivalled machining flexibility.
It offers full simultaneous five-axis machining capability as well as 3 + 2 and 4 + 1 operation. Baker Engineering is predominantly using the machine for 3+2 and five-face machining.
The DVF 5000 features a powerful, direct-drive spindle (up to 18.5kW/12,000rev/min), a generous-sized tool changer (up to 120 position), linear guides, and a 500 x 450mm work table with 400kg table load.
It also has fast 40m/min rapids and was supplied to Baker Engineering with a 60-position automatic tool changer, integrated tool measurement and the latest Fanuc 0iMF control.
The DVF 5000 has been in constant use at Baker Engineering’s facility since the end of April 2020 and as well as helping the company increase its productivity and efficiency the machine has also helped Baker Engineering win new machining work.
Mr Baker concluded: “Our decision to invest in the Doosan DVF 5000 has been vindicated. The machine has significantly strengthened our machining capacity and capabilities. It is fast, accurate and reliable, and represents great value.”