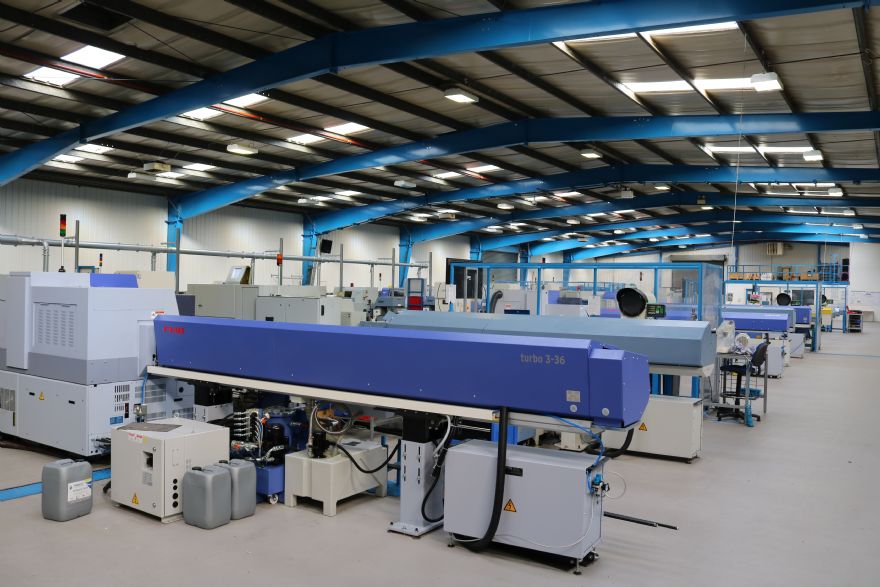
Dundee-based engineering firm
GA Engineering Sliding Head has invested a six-figure sum to boost its existing inspection capabilities. Part of
Pryme Group, an integrated manufacturing specialist, the company installed ‘state of the art’ inspection equipment earlier this year at a cost of £100,000.
It takes the total amount invested in new machinery at GA Engineering Sliding Head’s facility on the West Pitkerro Industrial Estate close to a million pounds over the past four years.
The company, which has provided CNC machining to support clients in critical industries throughout the pandemic, purchased and installed two new inspection units which has allowed its quality team to increase productivity of inspection reporting while maintaining dimensional control directly on the shopfloor.
Designed for high-volume inspection of precision cylindrical parts, a Vicivision M306 Techno allows for the fast, accurate inspection of components up to 300mm in length, 60mm in diameter and 10kg in weight.
In addition, an OGP SmartScope Flash CNC 200 with 3-D CAD-based ZONE3 is an automatic measurement system that uses high-resolution optics and touch probe capability to ensure accurate, reliable inspection of components. It is equipped with a 12:1 zoom lens that automatically compensates for magnification changes; reducing operator inspection times.
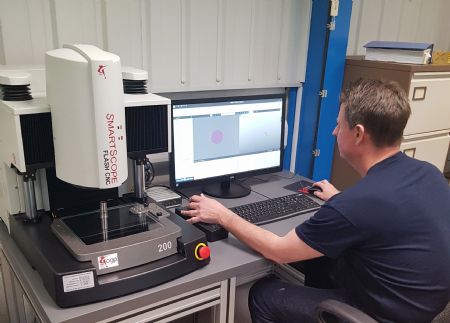
Whereas previous quality inspections required manual report creation, the new systems use networked QC-CALC data collection and statistical process control (SPC) software to manage, analyse and report inspection data from both machines.
The generation of instant, detailed reports speeds up the inspection process and reduces the potential for human error. Switching between inspection batches is also faster with the new equipment, freeing up operator time for more frequent inspections during production runs, allowing for any issues to be addressed.
Jim Stuart, GA Engineering Sliding Head operations manager, said: “The new inspection equipment has increased production and improved efficiency as well as significantly improving the workflow of our quality department.
“While the industry is still overly reliant on manual processes, these new systems give us an important differentiator in the current market by helping to reduce process and inspection costs.
“This allows us to be more competitive and, such is the quality of our reports, customers have complete confidence in the information that we provide as a supplier, often without the need for further inspection.”
He added: “Looking ahead, we expect that the company’s operations will benefit greatly from these enhanced capabilities – particularly in terms of time savings when you consider the vast quantities of machined parts that we deal with every day.
“We have been successful in our diversification strategy, with between 30 and 40% of our client base consisting of oil and gas customers – both in the North Sea and further afield. Increasingly, we are experiencing strong demand for cable assembly for the defence, space and satellite sectors.
“This year has also seen the team machine vital components for motors, ventilators and other healthcare equipment. We are extremely proud to have played our part in supporting the country’s key workers.”
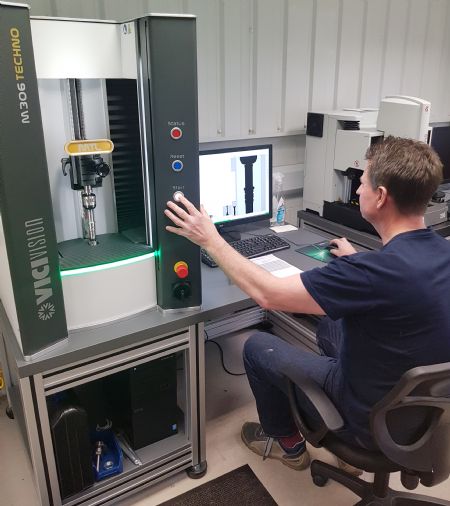
GA Engineering Sliding Head anticipates additional work orders from clients due to these improved capabilities. The company continues to experience strong demand for its precision machining capability from a diverse client base, including space, oil and gas and general engineering.
Continuous investment in new equipment has added to the company’s already extensive suite of market-leading technology; bringing a range of benefits including greater speed and efficiency for client projects and the ability to cater for ‘exotic’ materials including Super Duplex, titanium, Inconel and other nickel alloys.
Pryme Group CEO Kerrie Murray said: “Despite challenging market conditions, our Dundee operations – including GA Engineering Sliding Head – have performed well in the year to date and I would like to take this opportunity to pay tribute to my colleagues for their continued efforts and dedication.
“We continue to enjoy demand for our services from a broad customer base, including those operating in aerospace and defence, which gives me cause for optimism.
“Meanwhile, the pandemic has accelerated our entry into new markets, such as the pharmaceutical and healthcare equipment sectors, which present significant opportunities for the business.”