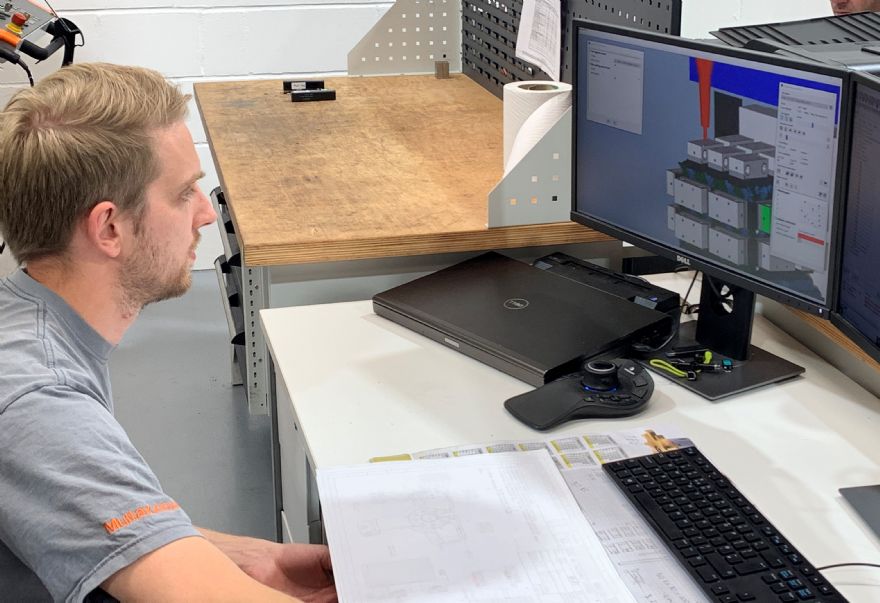
Buying its very first machine in December 2016,
Multax Engineered Precision Ltd’s turnover has already reached £3 million, a feat it puts down to its philosophy of investing in automating production, reducing man hours, and investing in industry leading technology.
Like any small business start-up, nothing would have been possible without the dedication and sheer determination shown by company founders John McNab and Ashley Mizen, two ex-work colleagues that were working around the clock in their respective posts while setting up the new business.
To achieve the company’s vision of automated production, the first machine installation was a 10-pallet five-axis Mikron HSM600U that was supported with a Widia cutting tool voucher promotion scheme from
Industrial Tooling Corporation (ITC) and CAM software from
Open Mind Technologies.
The ISO 9002-certified Andover company now has 17 staff and has invested close to £3 million on 10 machine tools and supporting equipment since its inception. This investment level has been acknowledged with the company winning accolades including Test Valley ‘Business of the Year’ with industry recognition coming from the Mercedes-AMG Petronas F1 Team that named Multax ‘Metallics Supplier of the Year.’
This is a credit to the ability of Multax to manufacture anything from simple to complex components with ‘unparalleled’ quality levels. The company is now taking this expertise which has been widely recognised in Formula One circles and is now actively winning new customers in other industry sectors.
The Ventilator Challenge for the Covid pandemic is a prime example of how this agile business can support a variety of customers across sectors.
Maximising automationDirector Ashley Mizen said: “Five of our six five-axis machines are automated, and we try to maximise our automation as much as possible. We have a skeleton staff working overnight and we offer nightshift programming, so we can deliver jobs ‘next-day’ if we need to.”
He continued: “I was an Open Mind user before we decided to start the business. It is a ‘game-changer’ for us and we now have seven seats of HyperMILL. We have integrated machine models, and as it is so simple to train a non-CAM user, we now have our setters and operators using the software as a setting and programming tool. It allows staff to check the datum of the part, produce the tooling sheet, put the NC code into the machine and also run the verification software to prevent collisions.”
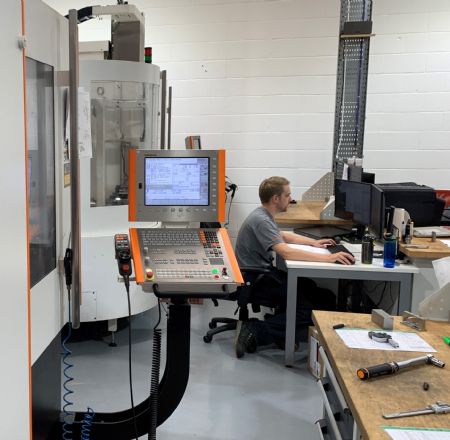
“Our team will always use HyperMILL for everything from the simplest of parts to the most complex. From a company prospective, it is great to have parts programmed with the software as this means we have then have them stored on our central server.
“If we get a repeat order, we can revisit the program, see what tools we have used and how the part is clamped, which gets us up and running quickly. HyperMILL has been a revelation to our business, and we definitely would not be where we are today without it.”
Mr Mizen added: “We are a medium to high complex component supplier and the strategies we use means that we use a lot of ballnose tools for five-axis cutting. With HyperMILL, many of these strategies can be created in seconds. We also have a lot of like-for-like components coming through our facility and we can overlay the models and use them as templates to enable quick set-ups.”
Multax is also adopting the groundbreaking Virtual Machine platform from Open Mind. Mr Mizen continued: “From my understanding, HyperMILL will now replicate the machine control, so it runs the NC programme rather than using POF files. It also provides fully integrated models in the simulation package. In addition, we have also invested in the hyperMILL Optimisation Package which looks at the tool paths generated by the software and creates optimisations.
For example, HyperMILL has historically moved the cutting tool to a ‘home’ or ‘safe’ position while the machine table is indexing; to optimise that position, the ’Optimiser’ will just move the tool to a clearance height and then bring the tool back to the workpiece, reducing movements and non-cutting times. HyperMILL has always been able to do this, but previously it was a lot of effort to get there.”
The catalyst for investing in Virtual Machine and the Optimiser software was the Covid-19 pandemic and the ‘Ventilator Challenge’ work the company received.
Mr Mizen said: “We were extremely proud to be involved in the ventilator project and we received an order for four different parts with an overall quantity of 31,000 that needed to be machined within eight weeks.
“To achieve this, we designed our own fixturing that allowed us to clamp 10 parts on each face of a tombstone. With 40 cmponents on each of the seven pallets, we had 280 parts in each of our five-axis seven-pallet GF Mikron machines.
“By developing our fixturing system and using the HyperMILL job linking feature, we reduced cycle times from 9min per part to just over 2min. This gave us the realisation that with incremental optimisations in a machine shop that runs 24/7, the benefits of Virtual Machine and the Optimiser could potentially be huge.
“So, instead of investing in another five-axis machine, we invested in optimising what we already had. Taking receipt of parts for the fast-turnaround Ventilator Challenge is a huge testament to how our business can adapt to the needs of customers, regardless of what industry sector they are in.”
He continued: “If the retraction and return of the cutting tool to the home position take 20-plus secs, we only have to consider the complexity of our parts and the number of pallet indexes plus the number of tool changes to see how this will boost our cycle times.”
Additional savingsMultax programmer Michael Pede said: “Virtual Machine is already bringing additional savings with relation to the time the part is actually on the machine. This is largely credit to the simple fact we can speed things up by linking parts together.
“We also have the Optimiser strategy that works with ‘Virtual Machine’, which will work on the individual tool paths and then link the individual tool paths together using five-axis movements, this is all done automatically.
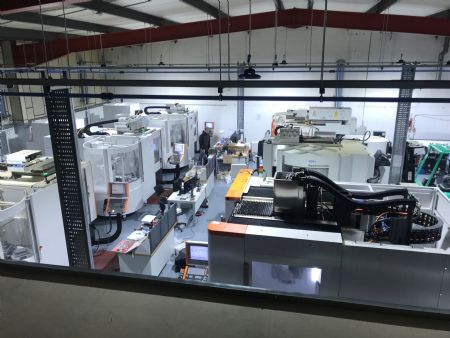
“It takes the time and effort away from the user and does everything automatically based upon the information you give HyperMILL regarding each machine. To get the most out of the software, you need to know what you are doing, but it is remarkably intuitive.”
Mr Pede added: “It is very simple to use, we have had several people with no experience join the company and we teach them in-house and send them on courses.
“It would be impossible to do what we do without a system like HyperMILL. We utilise it to the point that we can program something as soon as we receive the work and then run production and even the first-off part, lights-out with nobody here.”
He explained: “From a programming perspective, some of the biggest gains from HyperMILL are the time savings that come in terms of it being an all-in-one-package where users can design and manufacture in one ecosystem. We can also use the HyperMAXX strategies to optimise productivity and tool life.
“We get real benefits through the simulations we have while the graphical illustrations of the machines allow us to get as close as we absolutely can to the table with the cutting tools.”
Part of the company’s 10-machine inventory includes a Goodway GLS2000 turning centre and a GLS2000LYS Y-axis machine and the HyperMILL software package has been installed to help here too.
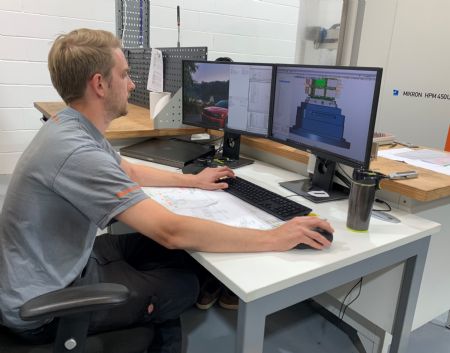
Mr Pede concluded: “We recently invested in the turning modules to expand our capabilities and also help with more complex strategies where we can use the high-performance turning package within the HyperMAXX bundle that can be applied to some of the harder materials we are turning.
“We have managed to use this on materials like Inconel and this has dramatically reduced our cycle times and increased our tool life while giving us a better surface finish.”
“We had one part with a very deep groove in it and the package enabled us to machine a lot faster because we could in-feed in both directions, so rather than retracting out of the part, we were able to feed straight back in with left and right feed cuts.”