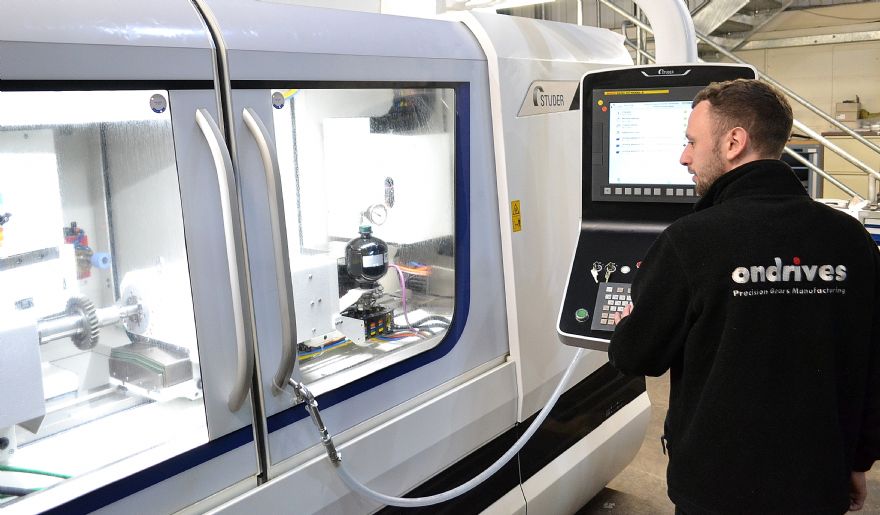
The ability to carry-out the highest standards of cylindrical grinding is a prerequisite when manufacturing high-precision gears and associated components. In order to achieve the required levels of roundness and surface finish, Chesterfield-based Ondrives recently purchased a Studer S31 cylindrical grinding machine from Telford-based
Micronz Ltd.
Ondrives can trace its origins in the precision-gear industry back over 80 years. Based in a 3,200m2 facility, the company has access to a wide range of advanced gear manufacturing equipment, including a Studer S21 cylindrical grinding machine installed in 2011.
The decision to install a second Studer machine was prompted by the need for Ondrives to increase its high-precision internal, external and thread-form grinding capacity to meet ever increasing customer demand for its gear related products.
When compared to Ondrive’s existing S21 model, the Studer S31 has increased the company’s between-centres grinding capacity from 400mm to 1,000mm, while also boosting the efficiency of its precision-grinding work.
Ben Hinchliffe, Ondrives’ managing director, said: “A growing order book and the need to increase our capacity recently created the need for a second high-precision cylindrical grinding machine. We have enjoyed excellent service from our existing Studer S21 and the machine continues to efficiently produce high-quality ground components.
“Having researched the market to ensure that we secured the best possible machine we concluded that, although the Studer S31 cost slightly more than the other machines we looked at, it was by far the most technically capable option. Moreover, the service and support we have received from Studer and its UK agent Micronz have always been first class.
“The Studer S31 was specified with the addition of several options, including a synchronous driven tailstock. This enables our operators to complete grinding work in a single set up, rather than making multiple changeovers. The Studer S31 has more than doubled our between-centres grinding capacity, increasing our precision grinding capabilities and significantly raising our efficiency levels.”
‘Mineral cast base’The Studer S31 has been designed for the cylindrical grinding of individual parts, small batches, and large-scale production runs. It has a centre height of 175mm and is available with between centre options of 400, 650, 1,000 and 1,600mm.
A substantial Granitan base (Granitan is the name of the mineral casting material from which Studer machine bases are made from) forms the foundation this machine, to ensure maximum levels precision, performance and reliability.
Developed by Studer, this material has proven its value over many years, providing “excellent cushioning characteristic to ensure outstanding surface quality of ground workpieces while increasing the service life of grinding wheels.”
Reduced set-up and resetting costs, especially in single-part or small-batch production, are made possible by the S31’s turret wheel-head, which accommodates several grinding wheels and allows complete machining in a single clamping.
Furthermore, the S31’s swivelling wheel-head is equipped with water-cooled roller-based and maintenance-free motor spindles with stepless speed control and the latest generation of contact sensors.
Meanwhile, the machine’s universal workhead enables both live-spindle grinding and grinding between centres; it is equipped with roller bearings and achieves a roundness accuracy of under 0.0004mm; this can be improved to under 0.0002mm during live spindle operations, while fine adjustment allows for taper corrections in the 1μm range.
As with the S31’s tailstock, its workhead is equipped with a pneumatic lifting device to facilitate movement during setup and resetting. The machine can also be equipped with a chuck workhead for grinding chuck parts.
Grinding of shapes and threads is made possible by a C axis that offers position and speed control. This axis also features an indirect measuring system on the drive motor, thereby allowing thread grinding and simple form grinding. For maximum form accuracy, a direct measuring system is mounted on the workhead spindle.
The 90mm travel of the S31’s tailstock barrel simplifies the changeover to a new workpiece, while component families can be quickly set-up with minimal effort, leading to further productivity increases. Furthermore, the synchronous driven tailstock is hydraulically operated and is equipped with an electronic measuring system that allows simple readjustment, with both closing speed and positioning speed individually adjustable via control valves.
Control is via a Fanuc 0i-TF, which incorporates StuderWIN software. This allows programming to be achieved by a novice or by skilled operators thanks to the use of Studer Pictogramming. Meanwhile, StuderFormHSM saves time by enabling fast and efficient form grinding. StuderWIN can also be used to create grinding and dressing programs offline.