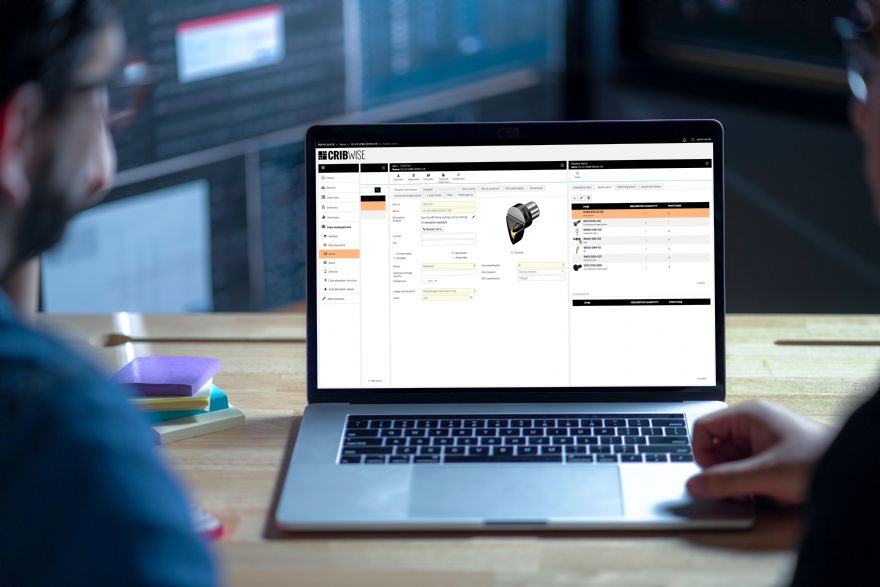
Could an out-of-control inventory be killing its profitability? Joakim Johansson, head of CRIBWISE, a new software package from
Sandvik Manufacturing Solutions, outlines the costs associated with poor inventory management and how cloud-based software could be a simple solution to streamline shopfloor operations.
The impact of the Covid-19 pandemic has forced many manufacturing companies to take a long hard look at efficiencies within their businesses as they have had no option but to cut costs to weather the storm.
A substantial number have opted to implement one-off measures, such as reducing the numbers of staff or reducing their marketing spend, but those that have taken a more long-term approach to increase operational efficiency will still be reaping the rewards long after the pandemic is a distant memory.
An effective tool-management system is one way that companies can streamline their operations and boost their bottom line. An out-of-control tooling inventory is a more widespread problem than many machine shops realise and it can have a big impact on costs — a disorganised tooling inventory can lead to disorganised working practices.
A survey undertaken recently by Sandvik Coromant found that 30-60% of tool stock is uncontrolled and is simply stacked by machines, getting in the way of work, forcing operatives to make detours, and sometimes even posing safety risks.
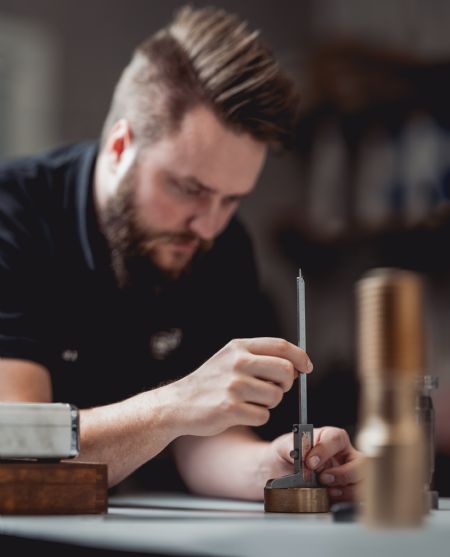
A large tooling inventory makes it harder to find what is needed — operators can waste 20% of their time looking for tools and can cause delays to orders, unnecessary re-orders of tools and costly mistakes. The survey found that 15% of jobs can be halted or delayed due to the fact that a machine shop hasn't got the correct tools. Most strikingly, the survey found that 80% of work is performed with only 20% of the tools available, and that 60% of tools in an inventory will be rendered obsolete before they are used.
There are also ancillary costs associated with an out-of-control tool inventory. These include ‘opportunity costs’ — space used for storage is space that cannot be used for other purposes, such as a new product line, new machinery and offices — money tied up in unnecessary assets is money that could have been spent elsewhere on more profitable endeavours.
Furthermore, vast amounts of time can be spent maintaining and managing a tooling inventory, including ordering tools, putting them away, picking, counting and relocating them. The larger the inventory, the greater the number of transactions and the greater the number of people involved.
Meanwhile time is eaten up by the administrative tasks associated with tooling inventory management — if the tooling is unnecessary or obsolete, this time is wasted. Also equipment is required to load and unload inventory, as well as transport tools to their points of use. All of this equipment must be maintained, and staff must be given training in order to use it safely.
It is also worth noting that insurance premiums escalate in proportion to the size of the inventory being held. This means that an unwieldy and obsolete inventory can lead to a higher insurance premium.
Simple, cost-effective solutionsTraditionally, an out-of-control inventory could be a lengthy and complex problem to solve, but luckily that is no longer the case as there are now simple and cost-effective solutions available.
While larger machine shops have been quicker to adopt the latest technologies – namely cloud-based inventory-management and tool-tracking software – such intuitive and proven solutions are now affordable for smaller shops to take advantage of too.
The software as a service (SaaS) delivery models employed by innovative and disruptive entrants to the market, such as Sandvik’s CRIBWISE, mean that access to highly sophisticated inventory management and tool-tracking solutions can be secured for a nominal monthly fee, making them an attractive option for even the most compact and specialised manufacturing SMEs.
The benefits of adopting inventory management software are numerous: they reduce administrative headaches; using intelligent rule-based systems (the ordering process can be automated); the ways in which tools move through an organisation and around the shopfloor can be streamlined and controlled precisely; and tool inventory management software can also be integrated into existing enterprise resource planning (ERP) systems to simplify the management of orders, the goods-received process and invoicing.
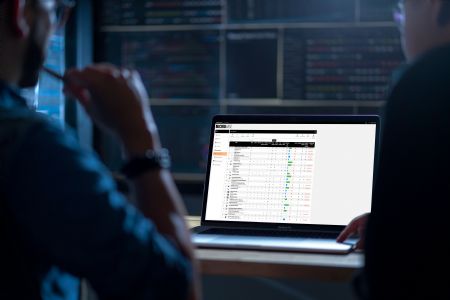
Using inventory management software for tools, costs can be easily controlled. Inventory can be made more visible, tooling can be marked as ‘in use’ rather than ‘out of stock’, eliminating over-ordering. Rules can be set that ensure that operators choose used and refurbished tooling before new. Tooling consumption patterns and spending over time can be tracked to identify areas of improvement.
Moreover, the use of inventory management software for tooling can increase productivity and the amount of time machines can be run. The tools available, where they are on the shopfloor and even the operative that selected them can all be tracked — eliminating time wasted searching for them.
Incoming orders and deliveries can also be tracked, and low-inventory alerts and automatic ordering rules can be established so production delays become a thing of the past.
Key featuresWith a growing choice of inventory managment software available, machine shop managers need to determine the best inventory management software for their businesses. Factors that need to be taken into consideration include: ease of use and the ability to customise it to their needs; it ideally should be vendor-agnostic; capable of hardware-software integrations that encompass all of their inventory (regardless of equipment or tool brand); and it should also be able to function as a stand-alone system, or with various vending machines.
In summary, a disorganised and bloated inventory can have a significant impact on the ability of an engineering company to get parts out of the door quickly, efficiently and profitability. Faced with the complexity of the problem, machine shop managers might be tempted to bury their heads in the sand or stick with the old ways of doing things — however there is now a real opportunity for them to bite the bullet and embrace a new technology that is so easy to use that they might one day wonder how they ever coped without it.