Goodman Precision Engineering Ltd (GPE), a market-leading motorsport precision sub-contract specialist, has invested in a new, multi-tasking Doosan Lynx 2100LY turning centre supplied by Leamington Spa-based
Mills CNC, the exclusive distributor of Doosan machine tools in the UK and Ireland.
The machine, a compact 6in chuck lathe equipped with roller LM guideways, a 15kW/6,000rev/min spindle, a 12/24 position servo-driven turret, the latest Fanuc control with 15in touchscreen iHMI, integrated Y-axis (+/-52.5mm) and driven tooling (3.7kW/6,000rev/min), was installed at GPE’s site in Milton Keynes in January.
Since then, it has been used to machine complex, high-precision parts, primarily for a range of motorsport customers that includes many Formula One (F1) teams and Tier One suppliers, as well as machining components for automotive customers involved, for example, in ‘re-imagining classic cars for the electric era’.
The Lynx 2100LY is the first Doosan machine to be acquired by Goodman and is a result of the company’s decision to significantly grow and strengthen its in-house turning capacity and capabilities.
In addition to supplying customers with ‘right first time’ high-quality components made from a range of materials that includes steel, aluminium alloys, stainless steels, titanium, nylon, rubber, ceramics and plastics (including glass-fibre reinforced PEEK), GPE is renowned for machining high-accuracy parts, from powertrain and manifold components to parts for cylinder heads and air jacks, with impressive surface finishes.
GPE director Stephen Reynolds said: “Machining components to exacting tolerances and superior surface finishes (Ra. 0.4µm) from solid or castings is our forte.”
New technologyGPE currently employs 32 people and, to address skills shortage issues, operates an in-house apprenticeship programme. The company has 14 CNC machines — all DNC linked — at its disposal and regularly invests in new technology. It specialises in the machining of prototypes and one-offs through to small batch series.
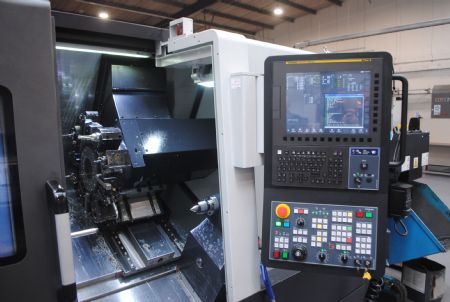
He continued: “We are a milling-led company and as such regularly invest in advanced three- and five-axis machining centres to increase our productivity, improve our performance and win new business in the ultra-competitive motorsport sector.
“While milling still remains the company’s primary focus, we recently made the strategic decision to augment our machining capabilities to include turning, and to provide this as an in-house specialism to existing and new customers.”
The decision was made partly to offset the seasonal ‘feast or famine’ dynamic of working in F1 by expanding the scope and scale of its machining operations and services — as a result the company has created an in-house turning resource. Up until that point GPE was focused, almost exclusively, on providing high-quality milling services to its motorsport customers, and supplementing them with a range of secondary finishing services such as anodising, coating and painting sub-contracted out to its preferred suppliers.
Mr Reynolds explained: “We knew, from experience and via our contacts, that significant organic growth and new business opportunities existed in the motorsport sector if we could offer both existing and new customers a high-quality turning service.”
This focus on growth resulted in GPE acquiring its first lathe in 2019 as well as recruiting an experienced turner to operate it. The company’s strategy to develop its turning capabilities went into overdrive with the outbreak of the pandemic in 2020.
Future directionMr Reynolds said: “Covid-19 caused significant disruption to motorsport across the world with events and competitions being cancelled and postponed. The turmoil created by the pandemic within our core markets and throughout our customer base was a real watershed and resulted in us forensically re-evaluating the business and making strategic decisions about its future direction.”
He added: “In short, we decided, from both a survival and growth perspective, to provide existing customers with new turning services, as well as diversifying into completely new markets.”
Having made the decision to augment its machining operations, the trick for GPE was to get its relatively embryonic turning operation up to the same level and standard as its milling operation - and to do this as quickly as possible.
Mr Reynolds explained: “We created, and are currently implementing, a strategic plan to help us develop and grow the turning side of the business. Multi-axis and multi-tasking lathes with, for example, Y axes and driven tools help us machine complex, high-precision parts in ‘one hit’ and make us more efficient. Multi-tasking machines help us with production scheduling, always an issue with motorsport customers who often expect part alterations and iterations to be machined and delivered in next to no time.”
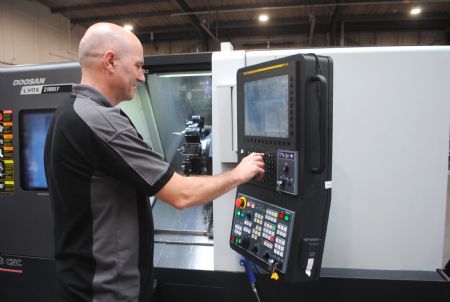
He added: “The machine ticks all the right boxes: it is an advanced multi-tasking machine with a compact footprint. Lynx lathes and turning centres are reliable, versatile and represent great value. The fact that they are backed by Mills CNC’s after-sales services and technical support only adds to their appeal.”
Since being installed the new Lynx hasn’t missed a beat — it is operating 16 hours each day — and its ability to machine parts to completion in one set-up means it is more than paying for itself. As well as being used to machine parts for motorsport customers, the machine has also machined a range of components for the company’s ‘diversified’ customers operating in a variety of industry sectors including aerospace, defence and rail.
Mr Reynolds concluded: “We have a strong reputation in the market for our ability to machine high-precision, complex parts in low volumes and deliver them within budget and on time, every time. The Lynx 2100LY has helped us strengthen our position with existing and new customers requiring exceptional, competitively-priced small turned parts — we are delighted with this investment.”