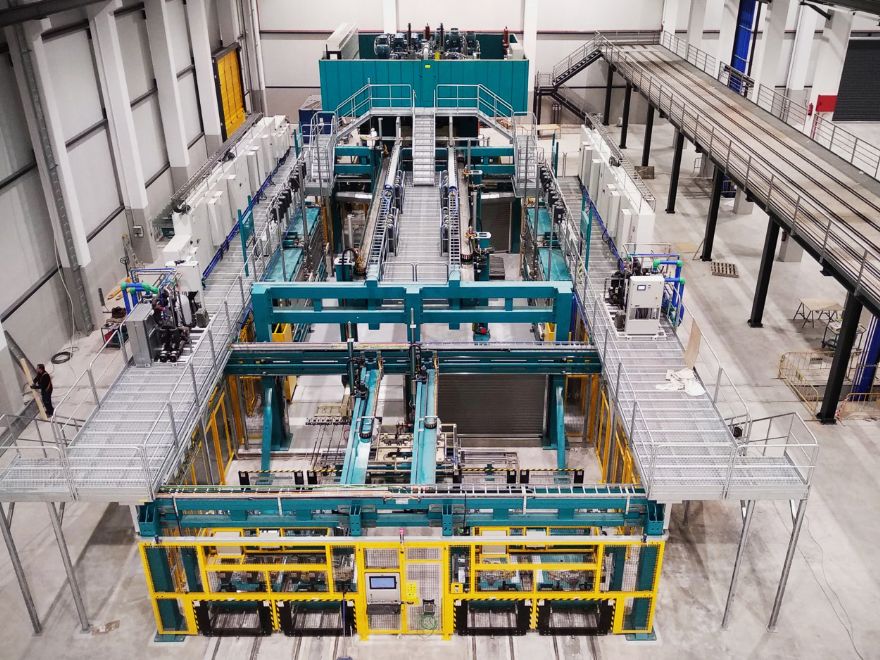
Together with
Gedia,
AP&T — based in Ulricehamn, Sweden — has created what is ‘probably the world’s most advanced production line for manufacturing press-hardened components for the automotive industry’. AP&T’s latest press-hardening production solution allows car manufacturers to produce lighter, safer, and more flexible designs that are both cost and energy efficient. The solution includes AP&T’s servo-hydraulic press and TemperBox, which enables soft and hard zones to be combined in the one finished component.
The first commercial production line containing ‘both innovations’ became operational at Gedia in Germany late in 2019. The same equipment was also later installed at the company’s facilities in Spain and the USA, so it is no surprise that that Gedia and AP&T are ‘pioneering the future of press hardening in the industry’. It is a result of a ‘deeply rooted collaboration’ between the two companies that has lasted a decade.
Gedia has been manufacturing pressed sheet metal parts for the automotive industry since the mid-1950s. In 2005, the company began to take a serious interest in the opportunities that press-hardening technology offers for manufacturing structural parts that combine strength and low weight.
To sound out the market, they contacted AP&T, an early leader of developing production lines for press hardening; and while for years, the two companies kept in touch sporadically without it resulting in any tangible business, in 2012 Gedia sent out an invitation to negotiate and subsequently ordered three complete lines, which became operational between 2014 and 2016, one in Attendorn (Germany) and two in the company’s production facility in Nowa Sol (Poland).
Technically challenging projectMichael Hunger, Gedia’s director and head of sales and marketing Europe and key account manager, said: “It was a technically challenging project that provided useful experiences and sparked the motivation to continue developing and testing new press-hardening technology together.”
When Gedia later received an order for partially press-hardened parts for one of Germany’s major car manufacturers, the company needed a new industry-scale line for serial manufacturing, thereby starting a project that would push the limits of press-hardening technology.
Jörgen Theander, AP&T’s engineer responsible for the project, said: “We not only need to produce a large number of components per hour, but also install the line in the limited space of our existing premises. We started planning the new line in August of 2018 and set the target to have it operational by 1 January 2020.”
Even before the first line was completely installed, AP&T received an order for an identical line for Gedia’s Spanish production facility near Barcelona, and in January 2020 Gedia ordered a third production line of this type. This was for the company’s Dalton, Georgia, factory in the USA, with installation scheduled for the fall of 2021.
Mr Theander concluded: “Together with Gedia we developed what is probably the world’s most advanced production line for manufacturing press-hardened components for the automotive industry. By collaborating, we not only solved technological challenges but also gained valuable experience.
“Compared to earlier AP&T press-hardening lines, the new lines are considerably more energy efficient; they also make it possible to shorten manufacturing cycle times of certain products by up to 20%. Now, collaboration will continue in an attempt to significantly increase annual production hours.”