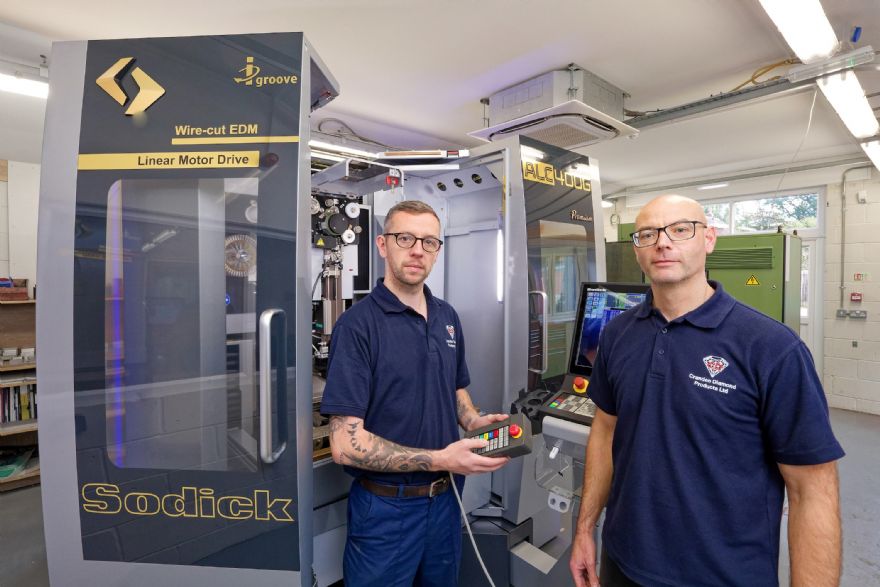
A new Sodick ALC400G CNC wire-erosion machine supplied by
Sodi-Tech EDM is now performing the work carried out by two previous machines at Kent-based
Cranden Diamond Products (CDP), a world-leading manufacturer of precision diamond and CBN (cubic Boron nitride) grinding wheels. Furthermore, CDP is also enjoying a significant boost in precision with its new Sodick machine, helping the manufacturer to meet the growing demands and expectations of its high-profile customers.
Trading since 1984, Kent-based Cranden Diamond Products makes precision diamond and CBN grinding wheels for a number of applications. For instance, the company produces profile wheels with tolerances of ±5µm for the creep-feed grinding of carbide inserts and tooling. Another specialism is resin/polymer bonded wheels for grinding tungsten carbide, ceramics, hardened steels and glass. Cranden Diamond Products manufactures every grinding wheel to order, exporting around 50-60% of its output.
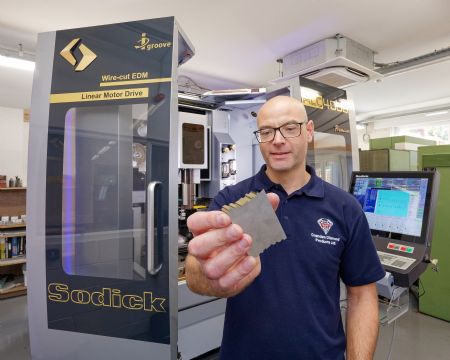
Since the pandemic, increasing tensions in various global locations have led to an increase in defence industry work, for both aerospace and marine applications. Some of this work involves machining challenging composite materials.
Stuart Cleary, Cranden Diamond Products operations director, said: “We are seeing a growing number of military vehicle parts made from Kevlar, for example. Kevlar is extremely difficult to process after moulding, so it requires grinding to final shape using either diamond or CBN wheels. To make these tools, we electroplate crystal particles to very precise engineering profiles that we generate in the grinding wheel.”
Part of the manufacturing process requires the application of wire EDM. Seeking an increase in precision for this critical process, Mr Cleary researched the market for a new machine to replace one of the company’s two ageing models.
First-class after-sales serviceHe added: “I shortlisted two potential machines, one of which was the Sodick ALC400G. We ultimately opted for the Sodick machine because Sodi-Tech EDM has an in-house team of service engineers who know the machines inside out. In the unlikely event of a breakdown we knew that the machine would be up and running again in 24-48hr, not two or three weeks. Even though I am sure we will hardly ever use this capability due to the reliability of Sodick machines, it was the first-class after-sales service of Sodi-Tech that sold the ALC400G.”
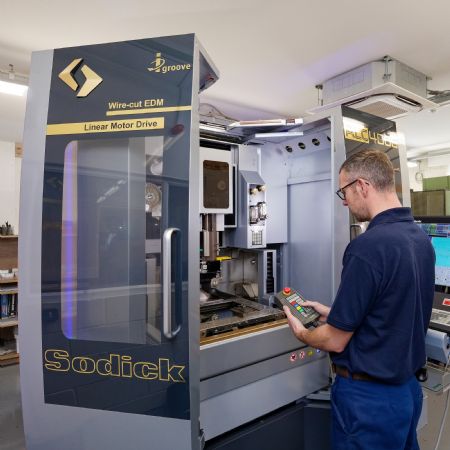
Installed in July 2023, the original intention was to replace one existing EDM with the new Sodick ALC400G. Mr Cleary continued: “Although we bought the machine to enhance precision, its productivity performance surprised us. We soon found it doing the work of both our previous machines. As a result, wire EDM is no longer a bottleneck – we can stay ahead of the curve and better manage our increasing workload. We are so impressed that we are already in discussions about buying another wire EDM and we wouldn’t dream of going anywhere else other than Sodi-Tech EDM.”
CDP finds the Sodick software far easier to use than its previous solution, partly due to the comprehensive training offered by Sodi-Tech EDM. Mr Cleary added: “We sent two of our best younger engineers on a three-day training course at Sodi-Tech’s Warwick facility — James Woollett, our senior programmer wears many hats in the company and is now in charge of all 3-D design engineering. Rory, a former apprentice at Cranden and natural engineer, has taken over the running of our CNC department. The training for the pair made for a very smooth transition from our previous EDM technology to Sodick. Even post-training, Sodi-Tech have been very responsive to any questions we had.”
Business is currently booming at CDP, particularly from a defence industry perspective. The UK is the world’s second largest defence manufacturer after the USA, with demand for precise, UK-engineered solutions soaring.
Mr Cleary concluded: “We have taken on many new employees since the pandemic, including several apprentices. Youngsters see engineering as ‘cool’ and we are attracting some great minds. Investing in machines like the Sodick really helps in that regard.”