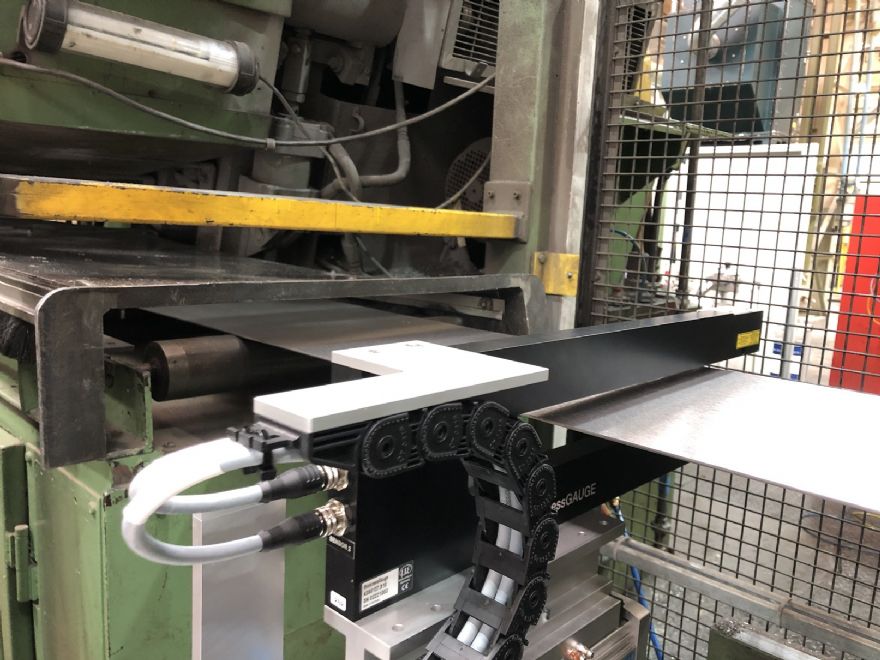
Based in Kilmarnock,
www.mahle.com/en/about-mahle/locations/3520.jsp Mahle Engine Systems UK Ltd is a supplier of aluminium/tin bi-metal and sinter (copper/bronze) bi-metal coils to Mahle Bearings plants globally. To measure the thickness of strip materials, the company has chosen the ThicknessGauge system from
Micro-Epsilon); this is also used to measure the cross-strip profile of the material to check for warp (bowed, curved or tilted) that would adversely affect the downstream cold bonding process.
Charles McMillan, head of quality/process engineering at Mahle Engine Systems UK, said: “The metal alloys that we produce at Kilmarnock are supplied in coils to other inter-group companies where they are used in the manufacture of automotive components such as engine bearings and thrust washers. The quality team at Kilmarnock decided it needed some sort of thickness measurement system for the strip material that the plant produces.
“The strip itself goes through various manufacturing steps, including ovens and rolling operations, to produce the desired strip thickness for customers. We eventually reach a point in our production process where the alloy strip material is ready to be sent to our cold-roll-bonding mill to be bonded onto a steel backing; and while we already have a fixed 100% inspection thickness measurement system and automatic gap control system on the cold-roll-bonding mill, this only gives us information on the bonded material output.
“We never really had any measurements of the incoming steel or of the alloy that we were producing in-house — just sample spot checks using a micrometer. We had used Micro-Epsilon products before, so we gave some strip samples taken from various steps in our production processes to the company, which carried out some process/machine capability tests. At that point, we were confident that the solution would provide us with the measurements we needed.
“We now use the ThicknessGauge to check the thickness of the incoming steel that we purchase, and to check the metal alloys that we produce in-house before we send these for cold bonding. Longer term, we’ll consider installing a permanent 100% thickness measurement system for incoming steel, for example, but currently we are using the ThicknessGauge to help us build up an overall picture of our process and machine capability at the plant.”
As well as thickness measurements, Mahle also wanted to check the cross-strip profile and shape of the strip as it moves through its production process, Micro-Epsilon added a feature in the ThicknessControl software that allows Mahle’s quality team to view the ‘warp’ of the strip material, to see if the material shape is bowed, curved or tilted.