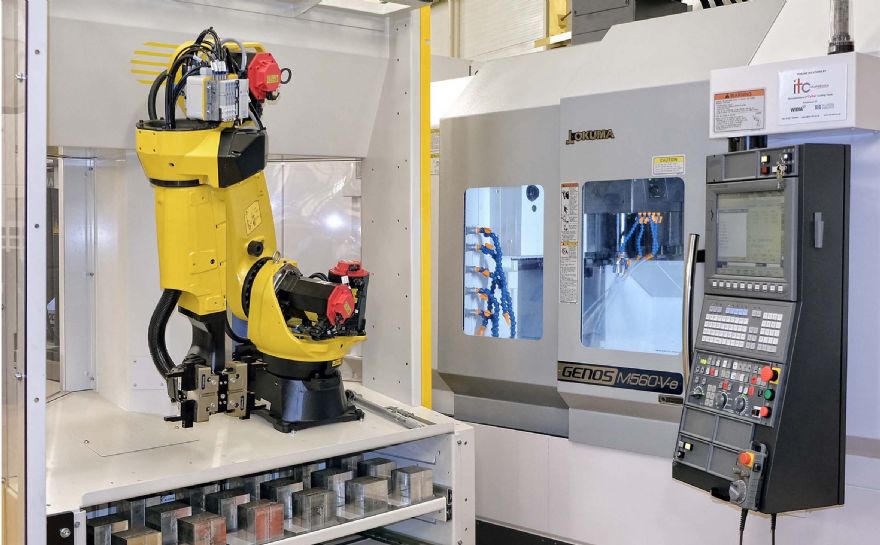
Leatherhead-based
NCMT, a supplier of high technology machine tools and engineering solutions for metal cutting and grinding applications — from stand-alone machines to complete production lines — will be showcasing a range of technologies at
MACH 2024, which takes place 15-19 April at the NEC, Birmingham (Hall 19, Stand 130).
The company is celebrating its 60th anniversary this year. Established in 1964, NCMT was one of the first companies that started out selling CNC machine tools into the UK and Irish markets before being appointed as the sole agent for Japanese-built Makino machining centres. A second agency with Okuma, another Japanese machine tool manufacturer, was agreed 12 years later to sell its range of machining centres, lathes and grinders into the same markets.
In 2005, the Makino-NCMT grinding division was established to develop and sell Makino machining platforms for creep-feed Viper grinding of nickel alloys throughout Europe. In 2015, NCMT was offered the Europe-wide agency for photo-activated adhesive workholding systems manufactured by Blue Photon in the USA.
The latest development occurred at the beginning of 2014, when NCMT signed an exclusive distribution agreement in the UK and Ireland with Israel-based Tritone Technologies, a global leader in additive manufacturing (AM) technology specialising in metal and ceramic applications. Typical AM components will be available to demonstrate the technology and there will be representation from Tritone Technologies on the stand to answer any visitor questions.
Thermally-stable constructionTaking centre stage at
MACH 2024 will be the Okuma Genos M560-V-e vertical machining centre (VMC). Its rigid, thermally-stable construction protects the machine from thermal deformation, which results in high-machining performance for an entry-level machine. The three-axis VMC can process a variety of materials, from titanium to aluminium, and does so without sacrificing dimensional accuracy, finish quality or productivity. The machine will be demonstrated with a Cellro X20 robotic system for component load/unload and storage. The M560-V-e has a 1,050 x 560 x 460mm working envelope and a maximum table load of 900kg.
The 15,000rev/min BT40 spindle moves in the X and Z axes, with the table moving in Y. A 32-position tool magazine is provided and software can be added, including Machining Navi to minimise chatter by finding the best cutting conditions. It employs a microphone to detect the onset of vibration and feeds information back to the control. A change in spindle speed is then recommended so that an adjustment can be made to suppress the chatter.
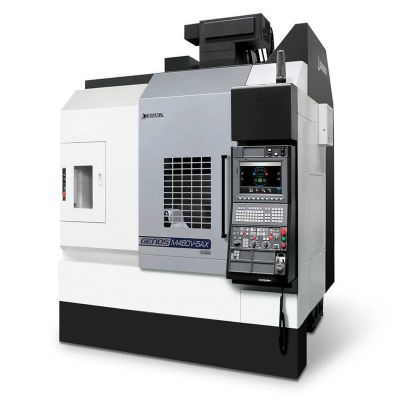
The popular Okuma Genos M460-5AX VMC with a working volume of 762 x 460 x 460mm will also be on display at
MACH 2024 and will be one of the first Okuma machines to be exhibited in the UK with the manufacturer's new OSP 500 control. It was the original five-axis machine in Okuma’s economical, series-built Genos range. The trunnion with rotary table and five-axis simultaneous control give the machine the ability to produce highly-complex components. The machine has a 15,000rev/min 22kW BT40 spindle which is served from a 48-position tool magazine.
Okuma’s Thermo-Friendly Concept is included in the specification, based on feedback from temperature sensors around the machine structure and spindle. It delivers remarkably high accuracy machining in a normal shopfloor environment. Tests have shown thermal deviation to be less than 10µm over a 24hr period, despite a variation in ambient temperature of as much as 8°C.
Ultra-high precisionFeatures such as Okuma’s five-axis automatic tuning system that accurately fine-tunes the geometry of the machine for ultra-high precision, and Okuma’s Absoscale linear encoders in the X, Y and Z axes, are all part of the standard specification, along with ServoNavi AI and ServoNavi SF, which automatically detect workpiece weight and adjust the machine’s feed drives to achieve higher speed production of lighter components.
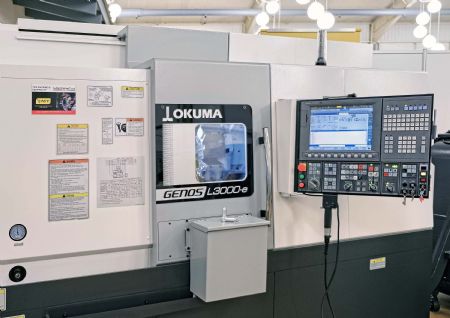
The competitively priced Genos L3000-e-MYW lathe from Okuma will make an appearance at
MACH 2024 fed automatically with shaft-type parts by a Cellro CoMate cobot (cobot). Maximum turning diameter is 300mm and rotational speed of the 22kW spindle is up to 3,800rev/min, all in a compact footprint of 2.5 x 1.9m. The six-tonne turning centre with sub-spindle and a 12-station turret with Y-axis and live tooling is robustly constructed and features an integral spindle motor and rigid guideways for powerful, high-precision machining of a wide range of materials including exotic alloys.
The machine has been designed so that cleaning, filtration and maintenance tasks are simplified. User-friendly features include a separate coolant tank for quick servicing, easy spindle access to speed maintenance and machine set-up, and reduced chip accumulation for less machine downtime during removal. Okuma’s Advanced One-Touch IGF is an option in the OSP control which allows users to describe part geometry such as diameter, length, grooves and threads using simple commands, from which the system draws the defined shape and then develops the part program automatically. An off-line version of the software is available for use on a PC to minimise machine downtime.
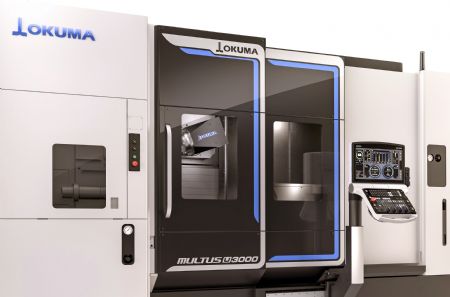
An Okuma MULTUS U3000 multi-tasking lathe will also be demonstrated on the stand which features a 240deg swivelling B-axis head and HSK-A63 (optionally Capto C6), and a 12,000rev/min 22kW spindle for turning or milling components up to 1,500mm between centres. The tool magazine has 40 stations as standard, but is optionally available with a capacity of 80 tools.
The machine is fitted with Okuma’s own linear scales for high-accuracy positional feedback. Servo motors deliver feed rates of up to 50m/min in the X and Z axes, and 40m/min in the 250mm Y axis. Together with the C-axis on the main spindle, the machine is capable of fully interpolative, five-axis (X, Y, Z, B, C) machining of freeform surfaces.
The specification of MULTUS U turn-mill centres can be extended further, giving users an ex-works product that is closely tailored to their needs. For example, a lower turret can be supplied, having 12 live tool stations and a 7.1kW 40.4Nm 6,000rev/min drive. A 22kW counter spindle can be ordered in place of the tailstock. The machine will also be exhibited with Okuma's new OSP-P500 control.
Next-generation Okuma controlThe OSP-P500 CNC system, manufactured in-house by Okuma along with virtually everything else on its machines, will be on show for the first time in the UK at
MACH 2024. It combines highly productive and precise machining with ease-of-use, energy efficiency and safety features to protect against cyber-attacks. Particularly well-suited to high-speed machining applications and achieving top quality surface finishes, the CNC has twice the computing power of a conventional machine control, shortening cycle times by up to 15%.
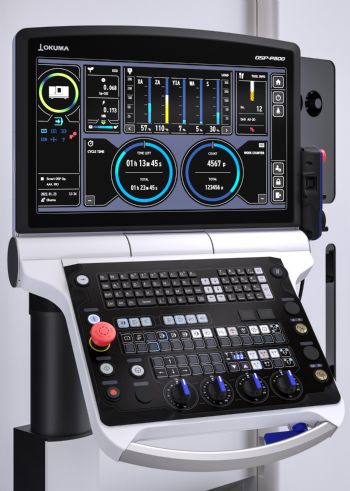
An on-machine ‘digital twin’ facilitates high-precision simulation of machining processes, reducing set-up times and speeding production. By performing these simulations on the machine itself, production can start immediately afterwards. Alternatively, with a ‘digital twin’ on a PC, simulation can be carried out offline while production is in progress on the machine.
Even inexperienced users benefit from the advantages of the control due to its user-friendly interface. A Smart OSP Operation function simplifies programming on the shopfloor by providing automatic guidance through all the necessary steps. People without any prior experience can learn how to machine a component in one day, helping to alleviate the shortage of skilled machine operators.
Thanks to the integration of Eco Suite Plus, the CNC system reduces power consumption. Smart features record and analyse every operating status as well as CO
2 emissions, switching to energy-saving idling if expedient and automatically adjusting the power drawn by peripherals, such as the chip conveyor. Okuma is gradually launching a range of new Green Smart Machines into the market, which will all be controlled by the OSP-P500.
Ultra-fast and compact five-axis VMCIn a space on the shopfloor of less than 3.3m
2, the N2-5XA HMC from Makino is capable of very high-speed machining of components up to 300mm diameter x 270mm high and weighing a maximum of 30kg, including fixture. The machine is ideal for fully interpolative, five-axis machining of complex components made from difficult-to-cut materials like stainless steel, cobalt-chrome and zirconium, as well as titanium- and nickel-based alloys.
Typical applications include the production of dental bridges and medical parts such as femoral knee implants. High surface quality is achieved without the need to use coolant. However, the N2-5XA is equally well-suited to machining a range of other parts within its working volume of 300 x 300 x 230mm, for example impellers and compressor blades for the aerospace industry. The horizontal-spindle design ensures that gravity assists swarf removal, prolonging tool life by avoiding recutting of chips that are frequently harder than the parent material.
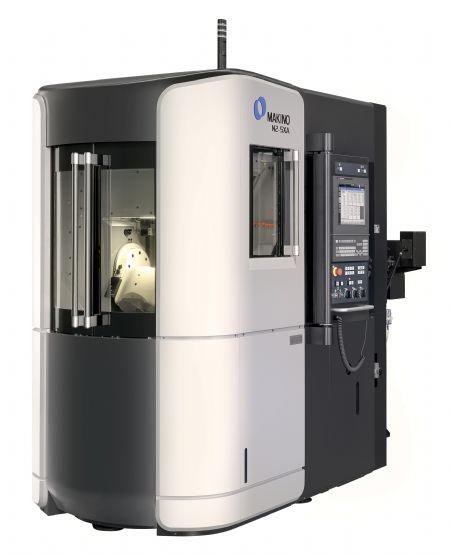
The N2-5XA has direct drive motors powering both the -120 +40 degree swivelling trunnion and the 200mm diameter rotary table. A robust, single-piece bed casting provides sufficient rigidity to enable rapid linear accelerator/decelerator of 1g in X and 1.5g in Z, without compromising accuracy. Coupled with rapid traverse rates of 42m/min in X and Y and 56m/min in Z, the results are short non-cutting times and very high levels of productivity. This is helped further by the ability of the HSK-A40 spindle to rotate from zero to 20,000rev/min and back again in four-fifths of a second.
A notable feature of the machine is the moving-column Y-axis driven by twin ballscrews. It not only provides greater rigidity than a compound table that performs X and Y axis movements, but also enables vertical motion to access the 36-tool magazine. Cutter exchange is executed directly in 2.5sec, without the delay that would be introduced by a tool-change arm.
The show will also mark the first UK appearance of the Makino DA300 five-axis trunnion-type VMC, configured as a production cell with 40 pallet positions on five levels for extended periods of lights-out running. Maximum workpiece size is 360mm diameter x 300mm tall for the eight positions on the top row of the store and 280mm tall on all other levels. Maximum payload per position is 60kg.
The automation package includes integrated chuck, pallet interface and Single Pro6 graphically-driven cell controller, via which it is easy to manage the machine and pallet system. The cell is ideal for five-sided, and fully interpolative, five-axis production of complex components in one clamping. A rigid structure combines with high dynamic motion control to reduce cycle times significantly whilst maintaining accurate performance.
Equipped with integral, direct-drive motors for the swivelling +30 to -120deg A-axis trunnion and also for C-axis rotation of the 340 x 300mm table, the machine deploys a 20,000rev/min 22kW HSK-A63 spindle capable of rigorous milling, drilling and tapping. A 180-position automatic toolchanger (ATC) ensures availability of an extensive selection of cutters to tackle the most complex of parts or component families and support lengthy periods of unattended operation.
Parts may be machined within a 450 x 620 x 500mm working volume at feed rates up to 60m/min. Even the rotary A and C axes are fast at 100 and 150rev/min respectively. Acceleration and deceleration to and from full speed takes just 1.5sec, minimising chip-to-chip times. Accuracy is ensured by scale feedback in all axes. Additional standard features include temperature control by cooling of the machine structure, spindle, ballscrews, bearings and drives.
World’s fastest wire EDM machineMakino's U6 H.E.A.T. Extreme wire-cut electric discharge machining (EDM) centre will also be in he spotlight at
MACH 2024. In addition to using standard wire from 0.1 to 0.3mm, it is optionally possible to run the largest diameter wire — 0.4mm — of any machine on the market. The wire is coated and distinct from the uncoated brass wire that is commonly used in industry.
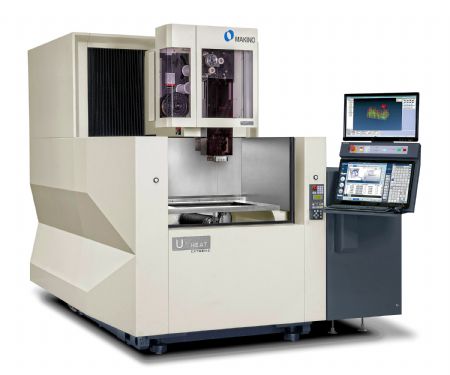
The extra wire thickness, together with the use of a second, booster generator in the machine, allows two to three times higher productivity and heavier duty machining compared with using a standard 0.25 mm consumable. Thicker wire also allows a slower unspool speed, so there is no increase in wire consumption rate.
Part of Makino’s popular U-Series wire EDM machine platform, the U6 H.E.A.T. Extreme uses Bedra copper core wire with a double layer coating having controlled zinc donation. It has been optimised for use with Makino’s generator and is exclusive to the new machine, promoting fast cutting at a reduced wire speed, leading to lower manufacturing cost. Areas of application include aerospace and medical component machining, separating additively manufactured (AM) parts, machining tall moulds and dies and tackling tough nickel alloys.
The U6 H.E.A.T. Extreme also features Makino’s HyperDrive Extreme wire control to raise speed and performance. The system employs servo motor tensioning that provides both jet and jet-less auto threading modes and expands the range and stability of wire tension to overcome the difficult job of reliably threading high-tensile strength and therefore stiff wire.
The machine has a cutting conditions library developed to provide an optimum combination of speed, accuracy, surface finish and wire consumption for both sealed and poor flush applications. Settings for two-pass machining have been developed to provide optimal productivity. To improve ease of use and productivity, the U6 H.E.A.T. Extreme has the intuitive Hyper-i twin-screen control that includes advanced functions to support the needs of operators at all skill levels.
The Makino EDAF3 die-sinking EDM machine on the stand features a rigid, precise structure and integral thermal cooling of the Y- and Z-axis cast components to ensure long-term accuracy. Table size is 700 x 500mm and the dielectric reservoir is built in to the base casting of the machine to improve thermal stability further and minimise the machine’s footprint. Working volume is 450 x 350 x 350mm and maximum workpiece weight is 800kg.
Free access to the working area is due to a programmable drop-tank. Unattended machining is extended by automatic electrode exchange and automated workpiece delivery and removal options. A cooling system maintains the dielectric at a constant temperature for stable burning conditions. A high precision C-axis head is an additional feature and electrodes weighing up to 75kg may be used.
The machine uses Makino’s latest Hyper-i control, which can be factory ordered and mounted on either the left or right, facilitating easy integration of one or more machines with a variety of commercially available electrode and work pallet handling robots. An on-board programming system, Makino Program Generator, has been designed for simplicity of use, while generating aggressive machining programs to meet the demand for shortened lead-times on today’s shopfloor.
Makino’s High Quality Surface Finish and ArcFree technology are standard on EDAF-series machines. Optional performance enhancing features include stabiliser technology involving liquid cooling of the Z-axis ballscrew and nut, allowing cavity floor surface blending to within 1µm. A further option is a fine-hole configuration for precision hole drilling with electrodes down to 0.1mm diameter.
Also exhibited on the stand will be the Blue Photon photo-activated adhesive system. The method is ideal for securing awkwardly shaped parts to allow maximum access to tools for tight-tolerance machining or inspection. The process involves applying an adhesive that is cured by ultraviolet light via an LED spot curing system. After machining is complete, the adhesive contact points can be sheared to free the workpiece by rotating the gripper pins in the fixture plate with a spanner. The residual adhesive can subsequently be removed by application of hot water.
Use of the technique is predicted to grow due to its ability to hold components securely with a shear resistance of up to 200kg per gripper point, while allowing cutters excellent all-round access for machining on five sides. Unlike magnetic clamping systems, it can be used to secure non-ferrous metallic parts, including ceramics and composites.
Blue Photon is ideal, for example, for clamping a turbine blade to enable the fir-tree and wedge face on the root as well as the shroud end features to be machined in one hit, without tolerance build-up. Traditionally, due to clamp interference, multiple operations are required. A novel turbine blade fixture incorporating four gripper inserts has been designed by NCMT that, once adhesive has been applied and cured, holds a blade securely by one side of the aerofoil.
Tests have shown that the clamping force produced by the fixture can easily withstand the rigours of machining. Material removal rate actually exceeded that achieved when the blade was mechanically clamped, as in the latter case the pressure had to be limited to avoid component distortion and marking. Other advantages of Blue Photon workholding are good damping properties to suppress chatter, reduced cost of fixtures for holding complex parts, and elimination of locating lugs on castings.