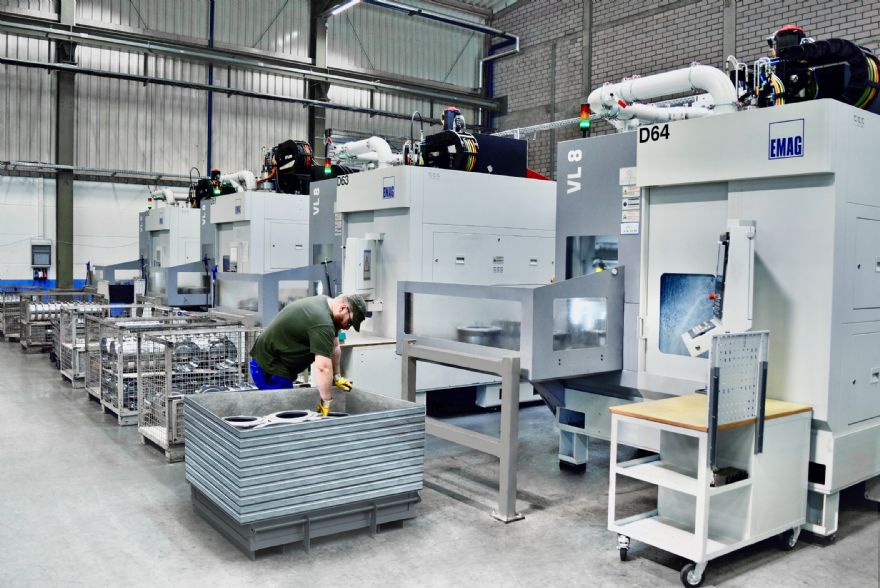
Based in the heart of the Eifel region in Germany, around 50km from Koblenz,
www.bf-daun.de/en Bharat Forge Daun produces rotationally symmetrical series components as a contract manufacture; the company also makes tools and moulds that are used by the ‘forging experts’ at Bharat Forge CDP and Bharat Forge Aluminiumtechnik.
One of the components machined by the company is the forged stator housings used in the hybrid drive of a large German automotive company; and while the dimensional and geometric tolerances of the pot-like shaped component are demanding, the material properties of this forged steel part further compound machining difficulties.
In addition, the customer has continuously increased the required quantities over the years, thereby necessitating Bharat Forge Daun to combine accuracy and efficiency with process reliability. Such requirements led the company to using vertical turning lathes (VTLs) from the German company
EMAG.
Christoph Steffens, head of mechanical engineering at Bharat Forge Daun, said the vertical design of these machines was a key factor in the investment decision. He said: “The horizontal lathes from another manufacturer had caused some difficulties in the past. Chip clusters regularly formed, and these had to be removed manually two to three times per shift. It was therefore obvious to us that we should carry out these processes in machines with a vertical design that offered unhindered chip flow and could achieve maximum process reliability.
“The decision in favour of EMAG was also based on the company’s existing know-how, as it used examples from other customers to show how stator machining is carried out in EMAG machines — along with low non-productive times and high-precision handling processes. Integrated automation includes a pick-up spindle and lateral conveyor belt — and these VTLs feature a stable base body made of the polymer concrete Mineralit.
“The response time and the expertise of EMAG’s service department have also played a key role. We produce five days a week in three-shift operation, and so far we have always been helped with minor faults in record time — in less than 2hr — via the company’s remote service facility.”