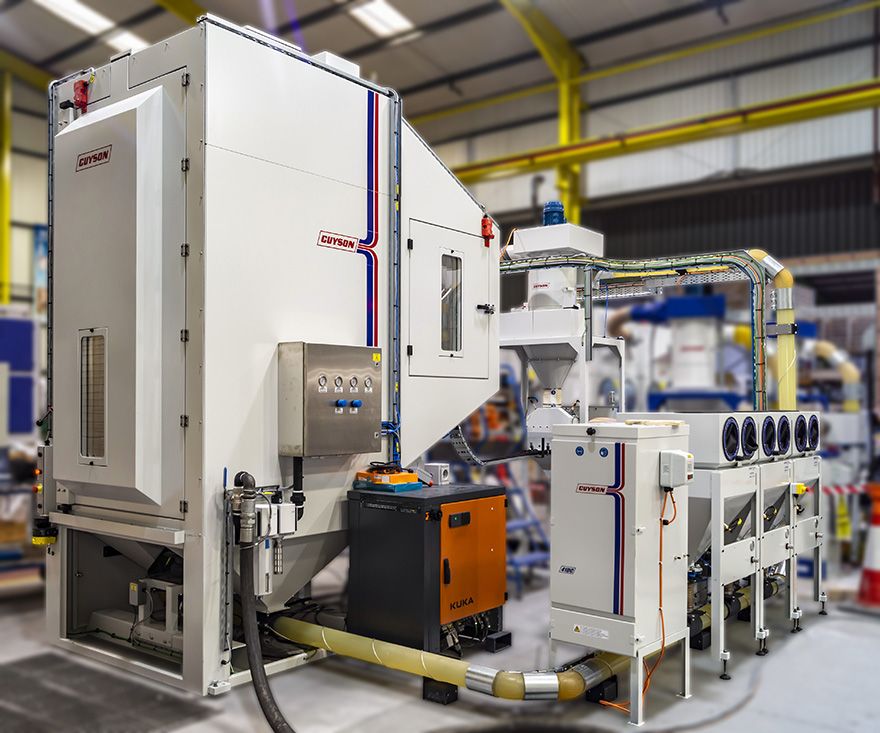
Skipton-based finishing equipment manufacturer
Guyson International Ltd recently installed a specially designed RB10 Robotic blast machine at
Bang & Olufsen, a manufacturer of high-quality audio and home entertainment products. Its designs are characterised by ‘maturity and thoughtfulness’, combining luxury materials with ‘state of the art’ industrial design, creating a distinctive brand niche.
Bang & Olufsen’s latest project, the Beosystem 9000c (pictured below), breathes new life into a classic by pairing a fully restored and reimagined Beosound 9000 CD player from the 1990s with modern Beolab 28 speakers. Limited to just 200 units, each Beosound 9000 CD player underwent meticulous restoration at Bang & Olufsen’s factory in Struer, Denmark, ensuring they meet the brand’s exacting standards.
Guyson International’s RB10 Robotic blast machine played a crucial role in perfecting the Beolab 28 speakers for the Beosystem 9000c. By meticulously blasting the Aluminium Lamella covers, the RB10 ensured a seamless finish that perfectly integrates with the original components. This precision is achieved through the RB10’s advanced features, including a KUKA KR12 R1810-2 foundry plus robot system and two model 900 blast guns, all managed via a user-friendly PLC/HMI graphical display.
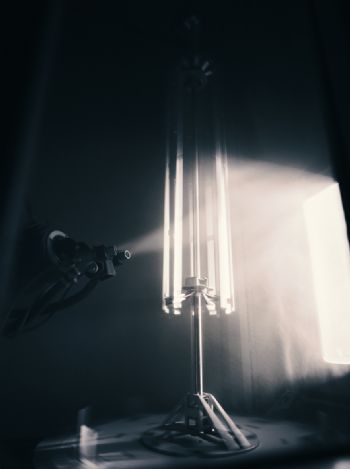
The extraction of dust and associated contaminants is conducted via a Guyson Model C800 Cartridge dust collection unit, working in conjunction with a Guyson Model CY600/16 Cyclone Reclamator. The function of the Cyclone Reclamator is to separate reusable media from dust, blast debris and under-sized media.
It achieves this by extracting everything from the bottom of the blast cabinet. Lighter particulates are then drawn off to the dust collection unit, while heavier re-usable blast media flows down the cyclone body and into a media storage bin to be recycled. The dust and spent media is extracted to the C800 dust collector, where it is then accumulated in a removable dust bin at the base of the dust collector for easy disposal.
The C800 dust collector is fitted with two pleated PTFE filter cartridges which aid with filtration. These are cleaned via automatic air pulses periodically, helping prevent dust buildup that would be detrimental to the extraction process. The media flow on this build is further aided by three combined media refill hoppers. Each can hold up to 100 kg of blast media for initial fill and automatic top-up.
This media is fed into the return ducting from the cabinet to the cyclone, mixing new media with the old, ensuring the optimum mixture for blasting is maintained. The media refill hoppers achieve this by working in combination with the cyclone hopper media level sensors, allowing for the automatic dosing of new beads into the mix to replenish losses experienced due to media breakdown. This allows for prolonged blasting of components, with no interruption to the effectiveness and efficiency of the blasting process.
The RB10 blast machine offers unparalleled adaptability, allowing users to customise blasting parameters and manage operations with ease. With real-time performance updates and the ability to store multiple blasting recipes, Guyson ensures efficiency throughout the machine’s lifespan. Prospective users can experience the benefits firsthand by submitting sample components for free feasibility testing at Guyson’s development workshop in Skipton.
Christian Haugaard Hornebo, Bang & Olufsen process engineer, concluded: “The machine is still performing and able to deliver stunning results. We are very pleased with the outcome and even more so with the first-class service provided by Guyson.”