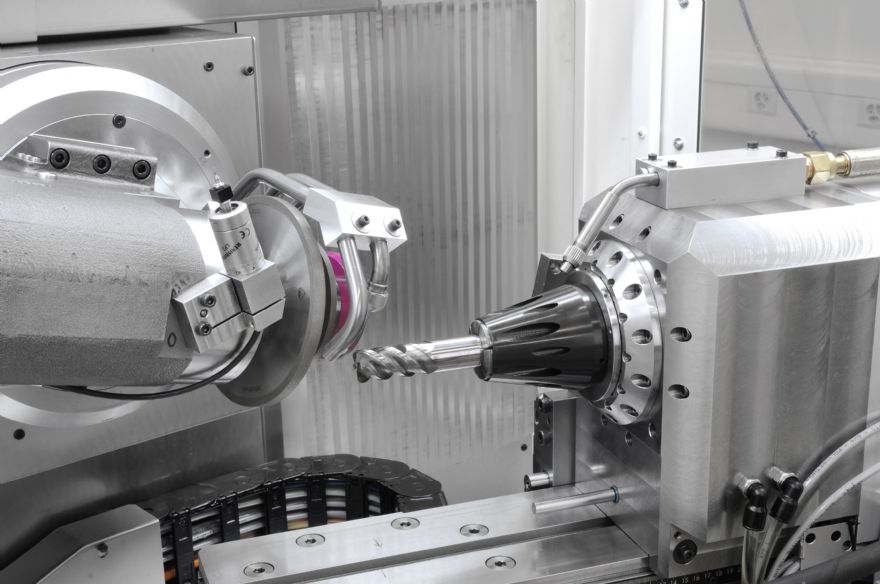
A recent introduction by Rollomatic is the six-axis GrindSmart 830XW tool-grinding machine. This sits at the top of the Rollomatic range and combines advanced hydrostatic guideway technology and linear motors to ensure ‘unparalleled precision and efficiency in CNC tool grinding’; it also uses ‘the same coolant oil’ for the hydrostatic guides, for cooling the grinding spindle, and for the coolant used during grinding, thereby ensuring that the machine is kept at a constant working temperature and maintains a high level of thermal stability during set up and during production grinding.
Rollomatic, which is represented in the UK and Ireland by Coventry-based
Advanced Grinding Solutions Ltd (AGS), offers a wide range of five- and six-axis tool grinding machines. Indeed, AGS says that today in the UK, more rotary cutting tools are manufactured on Rollomatic grinding machines than on all other brands combined.

With its latest GrindSmart 830XW machine, Rollomatic is introducing its vision of ‘Smart Autonomous Grinding’, the aim being to provide end users with a machine capable of managing production with very little human intervention; this capability includes the machine managing offsets to get the first parts manufactured within specification, as well as the ability to achieve unattended production over several days within very tight tolerances, as the machine can ‘interact with optional external robotic and automation systems’.
Chris Boraston, AGS’s managing director, says the Smart Autonomous Grinding programme also includes machine connectivity and communication exchange systems with other equipment such as measuring machines and laser etching, for example.
“One of the standout features of the GrindSmart 830XW is its ability to undertake long-term, unattended production with minimal human intervention. Indeed, Rollomatic’s RMonitor software allows for the fully remote management of production on the machine, as the monitoring software can be linked to devices such as smartphones.
“Also featured on the GrindSmart 830XW is a six-axis kinematic system that allows for the tilting of the grinding wheels to suit various operations, ensuring form accuracy can be achieved within very tight tolerances; and with the arrangement of the grinding spindle axis on this machine enabling freedom of movement on both sides via a total rotation angle of 240deg, both right-hand and left-hand tools can be ground with the same wheel pack.”
Surface finishMr Boraston went on to say that the high damping effect offered by the hydrostatic system results in superior surface finishes and extended grinding wheel life. “The mirror-like surface finish is especially important for the flutes of cutting tools; and compared with machines that do not employ hydrostatic technology, the GrindSmart 830XW machine improves finishes by around 20%. Furthermore, Rollomatic’s six-axis arrangement allows for the grinding point to remain constant during the grinding operation on tools such as ball-nose cutters, those with full radii, and special form tools. This ensures that, compared with machines that only grind with five CNC axes, optimum cutting tool geometry is achieved — including a radius shape accuracy of under 0.003mm.
“Moreover, the machine not only manages offsets and achieves tight tolerances but also interacts with its own internally mounted Fanuc-based robotic automation system. This accommodates 10 workpiece pallets and has an auto-load capacity of up to 4,500 cutting tools.”
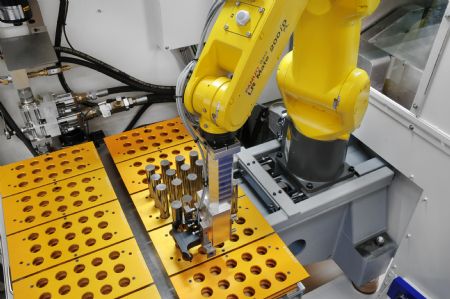
He continued: “The GrindSmart 830XW also includes Rollomatic’s ‘Smart Setup Assistant Function’, which was developed to ensure a first-ground tool was within all specified tolerances. The program generates a grinding path for each operation to be performed on the blank; and once these grinding operations have been carried out, they are measured by a touch probe measuring system, so that grinding wheel corrections can be defined before the first tool is made.
This capability ensures blanks are subsequently ground to the geometry programmed by the operator, taking into account the corrections required to ensure production according to specifications from the first tool. In-process measurement functions are then made periodically by either the probe or laser measuring system to ensure that tools remain within defined tolerances throughout production.”
Also featuredThe GrindSmart 830XW also offers a compact 15-station wheel and nozzle changer that offers a capacity for up to 60 grinding wheels and an arbor-to-arbor change time of 5sec. Additional options include Rollomatic’s Smart Shank Guide, which guarantees concentricity of under 0.002mm for every clamping, saving time and boosting productivity, as it is no longer necessary to automatically probe tools for runout during set up.
Mr Boraston says another option is Rollomatic’s Smart Steady Rest. “A high-precision steady rest for drills and other long tools, this provides stability for the grinding process and allows faster feed rates to be used, thereby ensuring the repetitive quality of tools throughout the production process. Moreover, this facility is not only very quick and easy to set up but also highly accurate.
“
Also worthy of note is that, although designed for manufacturing larger-diameter tools, the GrindSmart 830XW machine can be used to manufacture tools from 1 to 32mm in diameter and with a maximum overall length of up to 300mm. The grinding spindles synchronous motor has a peak power of 14kW with a rotation speed of up to 12,000rev/min; and with a weight of some 5,500kg this is a substantial machine.
“As with all Rollomatic tool-grinding machines, all available cutting tool software is included free of charge, together with free lifetime updates and upgrades. Another benefit that comes as standard is an unlimited hours three-year parts and labour warranty.”