Flexible dovetail-grooving system
Posted on 12 Jun 2014. Edited by: John Hunter. Read 4421 times.
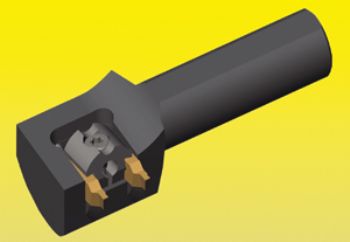
A new grooving system developed specifically for machining radial, axial and internal dovetail grooves is now available from Horn Cutting Tools Ltd, Ringwood (
www.phorn.co.uk). The Series 231 tooling was initially developed to meet the needs of oil and gas equipment manufacturers, but it has already attracted interest from other sectors where high-integrity O-ring sealing is required.
In trials that compared this tooling with alternative products, Series 231 achieved up to five-times the tool life, halved the machining cycle time and significantly enhanced
accuracy and repeatability. The machining process requires three steps, beginning with a standard plunge-grooving operation. This is followed by separate operations using left- and right-handed ‘half-dovetail’ profile-cutting inserts to produce identical dovetail angles to the required specification (a radius on the bottom angle of the dovetail eliminates the possibility of internal burrs). Left- or right-handed standard 221/228-style tool-holders can be used, and Horn’s AS45 coated micro-grain carbide inserts are standard.
A key aspect of the insert development was to maximise toughness and rigidity, hence the cutting ‘blade’ is precision-ground in such a way as to maximise its thickness and eliminate stress points, thereby optimising cutting performance and minimising wear. Horn offers tooling for entry grooves ranging in width from 1.4 to 8.5mm (in six steps); for axial grooving applications, a minimum outer groove diameter between 25 and 40mm applies. A tool-holder has also been developed for internal grooving within a tube of 80mm minimum internal diameter.