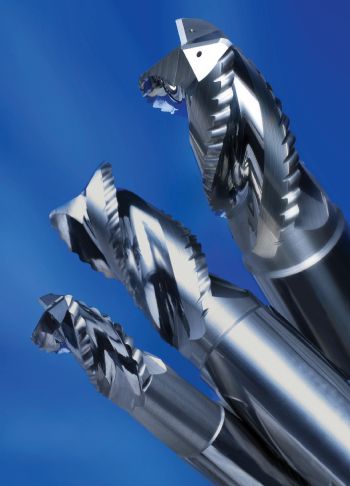
In addition to its solid-carbide cutting-tool technology, SGS Carbide Tool (UK) Ltd’s 200m
2 stand (Hall 5, Stand B42 –
www.sgstool.com) will be home to a full-size model of the Bloodhound Super Sonic Car for which the Wokingham-based company is both a product and project sponsor. “This is the first time the Bloodhound SSC has been exhibited outside the UK,” says Alan Pearce, EU managing director, “and I am sure visitors will appreciate the technical challenges involved with taking a hybrid jet/rocket-powered four-wheeled vehicle up to and beyond 1,000mph. Of course, we will highlight the areas where SGS solid-carbide cutting tools have helped to meet and surpass these challenges.”
A five-axis DMG DMU 75 machining centre will be under power on the stand, producing ‘typical’ customer components in a variety of materials, including aluminium, titanium and carbon-fibre-reinforced plastic. The tooling in use will include SGS’s S-Carb APR range of three- and four-flute roughing tools and the S-Carb APF four-flute finishing tools for machining aluminium, non-ferrous, and non-metallic materials.
Meanwhile, the S-Carb APR roughing tool features three feed holes for spiral through-tool coolant supply, and a high-pressure coolant supply (50-70 bar) assists chip evac-uation at the elevated material removal rates that can be achieved. Designed for optimum finishing of thin-walled components, the S-Carb APF high-efficiency four-flute end mill has twin-feed through-tool coolant supply.
It is equipped with three-stage chatter suppression to remove any negative harmonic influence on the workpiece or the cutting tool, namely: unequal flute spacing (to disrupt any rhythmic pattern); a patented unequal helix design that alters the angle at which each cutting edge enters and exits the component material (eliminating harmonics); and a variable-rake geometry that changes the size and shape of the chip created (to suppress chatter).
A new line of composite cutting tools introduced by SGS will also be highlighted at the show. It addresses the unique challenges of cutting composites by offering a series of four new tools and a further expansion of an existing product range. The new tools are: the Series 120 eight-facet drill designed to eliminate splintering and delamination of the composite stack; Series 31 carbon composite routers that avoid clogging during demanding slotting and roughing applications; Series 25 compression routers, which incorporate a left- and right-hand helix and eliminate the fraying of the material; and the Series 27 variable-geometry slow-helix end-mill, which is designed for milling highly abrasive materials.